FARGO, N.D. – It’s a fact of life that presents a significant challenge to producers: farms are bigger and more spread out, implements are wider and law enforcement agencies are stricter about how that equipment should be safely moved on public roads.
Wil-Rich Manufacturing in Wahpeton, North Dakota, thinks it may have an answer. The company displayed a revolutionary folding cultivator frame concept at the 2006 Big Iron Farm Show in Fargo this fall.
The unusual design allows a farmer to fold a large field implement into a compact 14 foot wide unit for transport on public roads and through narrow gates without lifting the side wings. In transit position, the 13 foot cap on the tank remains the cultivator’s highest point.
Read Also
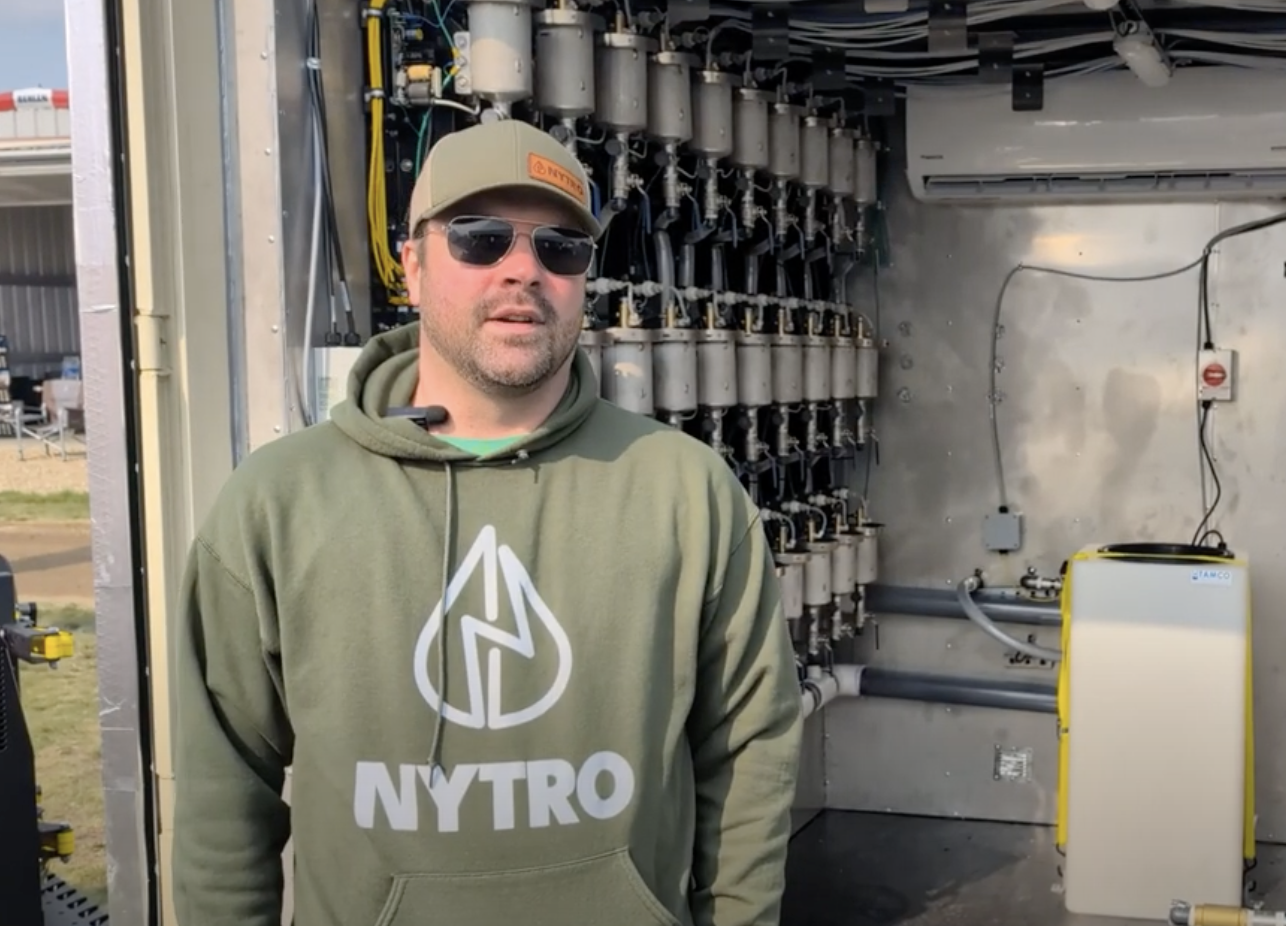
VIDEO: Green Lightning and Nytro Ag win sustainability innovation award
Nytro Ag Corp and Green Lightning recieved an innovation award at Ag in Motion 2025 for the Green Lightning Nitrogen Machine, which converts atmospheric nitrogen into a plant-usable form.
“The hitch slides into itself and out of itself like a telescope,” said Bruce Thiele of Wil-Rich.
The fore-aft centre line of the frame is the hitch, made of a 10 inch square steel tube that slides inside a slightly larger 12 inch square steel outer tube. Low-friction, ultra high molecular weight, or UHMW, plastic liners allow the steel tubes to slide easily without binding. The telescopic tube apparatus extends to the back of the implement to accommodate the length of the steel beams.
Thiele said that as the 10 inch square hitch beam retracts into the field working position, the two wing brace control arms push the wings back and out to their working position. Once the 10 inch beam has fully drawn itself into the larger square tube, it’s latched into the field working position and the two brace arms hold the wings in place. The operator is now set to work.
When it’s time to move to another field, the operator hydraulically de-couples the latches and pulls the hitch beam out to the transit position. As the 10 inch beam pulls forward, the two wing brace control arms pull the wings in tight to the sides of the centre frame section. Once the hitch is extended to the full transit length, the two wings have been pulled forward and can be latched into the transit position.
“The only section that lifts is the short toolbar directly behind the centre section, but even in transit that piece is still lower than the tank,” Thiele said.
The hitch beam can be extended or retracted solely with the hydraulics, or the operator can nudge the tractor forward or backward to speed up the process.
The tool bars are made of hefty seven inch square steel tube.
“With big tool bars like that, a producer can use the frame for just about anything he can imagine. It can handle a seed drill, row crop planter, strip tillage, sprayer boom or just about anything you can think of.”
Wil-Rich wants to make the basic folding frame versatile by designing working tool bars that can be changed in minutes.
Of the two tool bars on each wing, only the front one is permanently mounted to the main frame. This is the tool bar that’s attached to the wing brace arms and carries the lift wheels.
Each rear toolbar is a quick-change unit held in place by tapered joints and three steel pins, said Wil-Rich engineer Al Redman.
“You can remove and replace toolbars in a matter of minutes, without wrenches.”
He said the idea is to make the rear removable toolbars easily affordable and easily installed so a farmer can have them set up for different functions.
“This basic design with the tools mounted on a quick change tool bar is adaptable to many kinds of agricultural implements. I can see where a guy might have four, five or even eight different tool bar setups for different functions and different row spacing.
“If you can use one machine to replace maybe four other implements, that’s a tremendous cost savings for producers.”
Redman said Wil-Rich also has a 90 foot folding implement on the drawing boards, but no prototype.
“For 90 feet, we’re looking at a separate wing tip that folds up in the same manner as the 60 foot prototypes we have now. Plus we’ll be looking at a requirement of 500 plus horsepower for the tractor, so that changes things. There’s still a lot we need to learn about this design.”
He said the six prototypes now in operation use a drawbar-style hitch. However, he feels it’s necessary to explore the possibility of using a three-point hitch on high horsepower tractors for production models.
Wil-Rich expects to have six prototypes in farmer’s hands by next spring.
These will be 66 foot implements specifically built for in-field testing by row crop farmers.
Redman said the prototypes are all built with rubber tracks, partially to support the weight of the loaded machine and partially because this is the option that most producers now order when they buy field implements for seeding and cultivation.
The basic concept and the first prototypes came from a bean farmer in Indiana who built his first folding frame unit five years ago. Since then, he has built one unit a year to incorporate upgrades that he or Wil-Rich have developed.
His prototypes are shipped to Wil-Rich for testing and evaluation and then shipped back to Indiana and sold to local farmers, where they continue to be studied.
Wil-Rich expects the 66 foot folding frame implements to be commercially available for 2008 and the 90 foot units at a later date.
For more information, contact Bruce Thiele at 701-671-4404.