RED DEER – Aerial application technology has advanced rapidly in the past 15 years.
“Aircraft GPS systems can have fairly sophisticated LCD screens and with current light bars, (spray planes) can fly within a couple of feet of their swath,” Agriculture Canada scientist Tom Wolf said during an agronomy update conference this winter in Red Deer.
“You’re seeing a fairly sophisticated piece of equipment that’s doing the spraying now. I want you to understand, as potential clients, what you’re dealing with and what you can ask of the applicator.”
Read Also
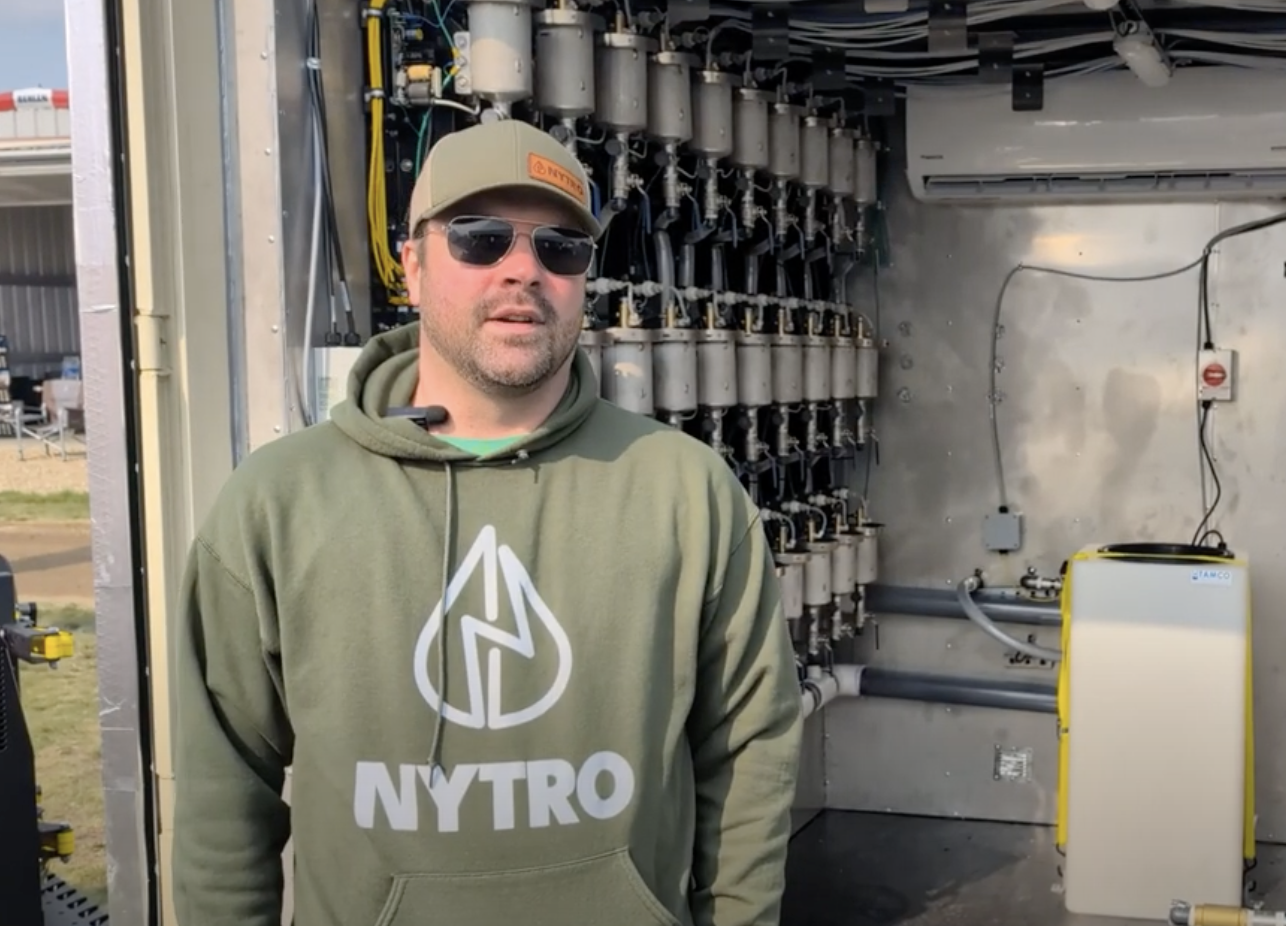
VIDEO: Green Lightning and Nytro Ag win sustainability innovation award
Nytro Ag Corp and Green Lightning recieved an innovation award at Ag in Motion 2025 for the Green Lightning Nitrogen Machine, which converts atmospheric nitrogen into a plant-usable form.
Wolf, who works in Saskatoon, said aircraft used to be powered by radial engines. They were loud, used a lot of fuel, were limited to speeds of 160 to 200 km-h and carried hoppers that were generally limited to 200 gallons.
“They tended to have wider booms, extending out to the edge of the wing tip. You’d get wing tip vortices, which was common a long time ago but is no longer common. They were limited in their swath width. They typically had a 50 to 60 foot swath,” Wolf said.
“Ten years ago, they typically had a single nozzle – often a flat fan nozzle – and you were tied into an application rate or droplet size. If you wanted to change that, you had to invest time to make those changes. They flew lower back then, too.”
Wolf said new aircraft tend to use turbine engines and are more powerful, fuel efficient and quieter. They’re also smaller.
“They can go 160 mph (250 km-h), but the spraying is often done at 140 mph (225 km-h). They will hold up to 800 US gallons, but the common turbines are between 400 and 600 US gallon hoppers. The booms have narrowed considerably and a narrow boom can avoid those troubling wing-tip vortices,” he said.
“There are innovations like wing tips that enhance the aerodynamics of the wing. They’re spraying wider swaths as a result. We’re talking about 60 to 80 feet now.”
Wolf said ground sprayers typically atomize spray solutions by hydraulic pressure. Aerial application atomizes spray by air-shear, in which a jet of liquid exiting a nozzle is broken up by the force of air hitting it. The greater the force, the greater the droplet breakup and the finer the spray.
Shear force can be controlled by air speed and deflection angle. Faster speed and greater deflection into the air stream creates finer sprays.
While spray pressure has some effect, a straight stream exiting out the back of a boom under higher pressure will experience less air shear because the force and speed of the stream overcomes the air shear.
Wolf said the common CP nozzle allows the operator to choose from three deflection angles and four flow rates, making it extremely flexible.
“The CP03 nozzle provides four different flow rates and three different droplet sizes with a single nozzle unit. With a 3/8 inch wrench you can make a change in about five seconds per nozzle.”
The CP09, designed for turbines, also provides various options for spray deflection.
“The more you deflect the spray, the finer the spray becomes. This gives you opportunities for making droplet size selection that you didn’t have easily before,” he said.
“We’re also starting to investigate the use of spinning disks in agriculture. They’re common in forestry, but less common in agriculture. They can adjust droplet size.”
Wolf said factors such as propeller wash, landing gear and wing tip vortices all affect the spray pattern. Since air pressure is higher under the boom than above it, air pushes out past the wing tips and swirls up. Fine droplets in this air will follow, making a swath wider than the wingspan, tapering at the edges.
Uniform patterns are difficult to achieve and require experimentation. To optimize the spray pattern, applicators use booms that are mounted lower and narrower than the wings and have customized nozzle spacing.
Wolf said aerial applicators continue to face three challenges: water volume, spray pattern uniformity and spray drift.
Wolf said typical spray volumes for aerial applicators include one to two US gallons per acre for insecticides, two gallons per acre for herbicides and four gallons per acre for fungicides.
“Let’s face it, they have smaller hoppers and they’re not going to be able to apply 10 or 15 gallons. That’s not a practical reality. What they do apply is the largest volume that’s practical for their cost-benefit equation,” he said.
“Because you apply less volume you must use smaller droplets or be satisfied with a lower droplet density. That’s just mathematics. You’re not going to get that super coverage you can get with a 10 gallon or 15 gallon ground application.”
Wolf said the best strategy for optimum spray performance is to maximize application volume, use coarser sprays to control spray deposit and drift, and retain adequate droplet density across the spray swath.
Wolf said pattern uniformity is the biggest challenge.
“Fuselage, prop and wing aerodynamics distorts spray pattern in the airflow. You can’t get the perfectly uniform patterns that you expect from (ground rigs),” he said.
“There are big improvements by lowering the boom, moving it away from the wing and having cleaner air at the point of atomization.”
Wolf said pilots usually fly in a crosswind, which causes a particular challenge for them because it results in a displacement of the spray, with buildups in certain parts of the air stream.
“With a side wind, you reduce the ability of the spray to escape to the edge of the wing. What we’re doing is working with aerial applicators to reduce upwind boom nozzles, add some on the downwind side and we have seen improvement by doing that.”
The newer spray planes tend to fly higher than older models, primarily because they have a wider wingspan. While Wolf thinks this may make drift worse, other sources have said flying lower doesn’t necessarily control drift better because it can result in ground effect flying and more vortices.
“We’ve got a higher boom, we usually have a finer spray and we have faster speeds,” Wolf said. “That gives the spray more time to be displaced so you have to go to coarser droplets that challenge your coverage.”
He said the best way to manage drift is to spray in low, consistent wind speeds under sunny conditions that encourage thermal turbulence. In higher humidity, it also reduces droplet evaporation. Using coarse sprays and limiting boom width to 65 percent of the wingspan also helps.
Wolf said he conducted a 30 acre trial in 2003 and 2004 that compared the efficiency of aerial and ground applications.
“Aschochyta blight in chickpeas was the issue. (The trial) was replicated twice, with four evening applications. We had the application done by an Ag Truck and a ground sprayer. The Ag Truck was four US gallons per acre and the ground sprayer was 10 US gallons per acre. The applications were done in the same evenings, within an hour of each other. We scouted for disease and sprayed according to scouting results,” he said.
“For the check plots, we saw a pretty rapid progression of the disease over the growing season. When we went with a ground application, the fungicide had a tremendous benefit as the disease progressed. The aerial application was similar. The only statistical departure from the trend was the last sampling date, at which time the yield had already been determined.
“We took it off with a 30-foot straight-cut header, took the tracks into account and measured yield normalized for 90-foot tracks and found no statistical differences in yield from aerial and ground application, although ground with no tracks was the highest yield.”
Wolf said there is still debate over whether air turbulence from the spray plane’s wings helps spray penetrate the crop canopy. He said it’s true air under the wing is compressed, which creates a downward airflow, but the released spray is not able to take much advantage of that.
Spray enters the crop canopy several seconds after the aircraft has passed, by which time the downward airflow has dissipated. Most of the droplets are deposited by gravity and wind, he added.
Stronger and more persistent air movement, such as that generated by the propeller, can affect droplet deposition, but it is limited to a small region of the spray swath.
Wolf said the operator is the most important part of the sprayer, whether on a ground rig or in the air.
“You can do it right or you can do it wrong with the same piece of equipment. A conscientious operator you know and trust, and with whom you have a rapport, is important when you go to aerial. Understand what the technology has to offer you and have a realistic expectation. You’re not going to be able to put on 10 gallons and you’re going to have uniformity issues,” he said.
“I think when we talk about application, a well-done application done at the wrong time isn’t that valuable. An average application at the right time is very valuable. So don’t get too hung up on how you’re going to apply it. Get hung up on doing it at the right time, with disease, insects and even weed removal.
“Recognize you can do a quarter section in an hour, on wet ground, at the right time. You have to weigh that against tracks and other things. Talk to the pilot, ensure volume and droplet size are appropriate for what you want, then call the operator and walk the fields to ensure you’re satisfied with the job.”