Veteran welders who have tried their hand at aluminum tell a common story.
After much difficulty, they weld the broken part back together, but when they try to bolt it back on the machine, it suddenly falls apart into four or five pieces.
It’s happened to just about anyone who has tried aluminum welding before they were trained by someone with experience.
“The biggest problem is aluminum looks very clean when, in fact, it’s not clean at all,” says welding instructor Jason Feal.
Read Also
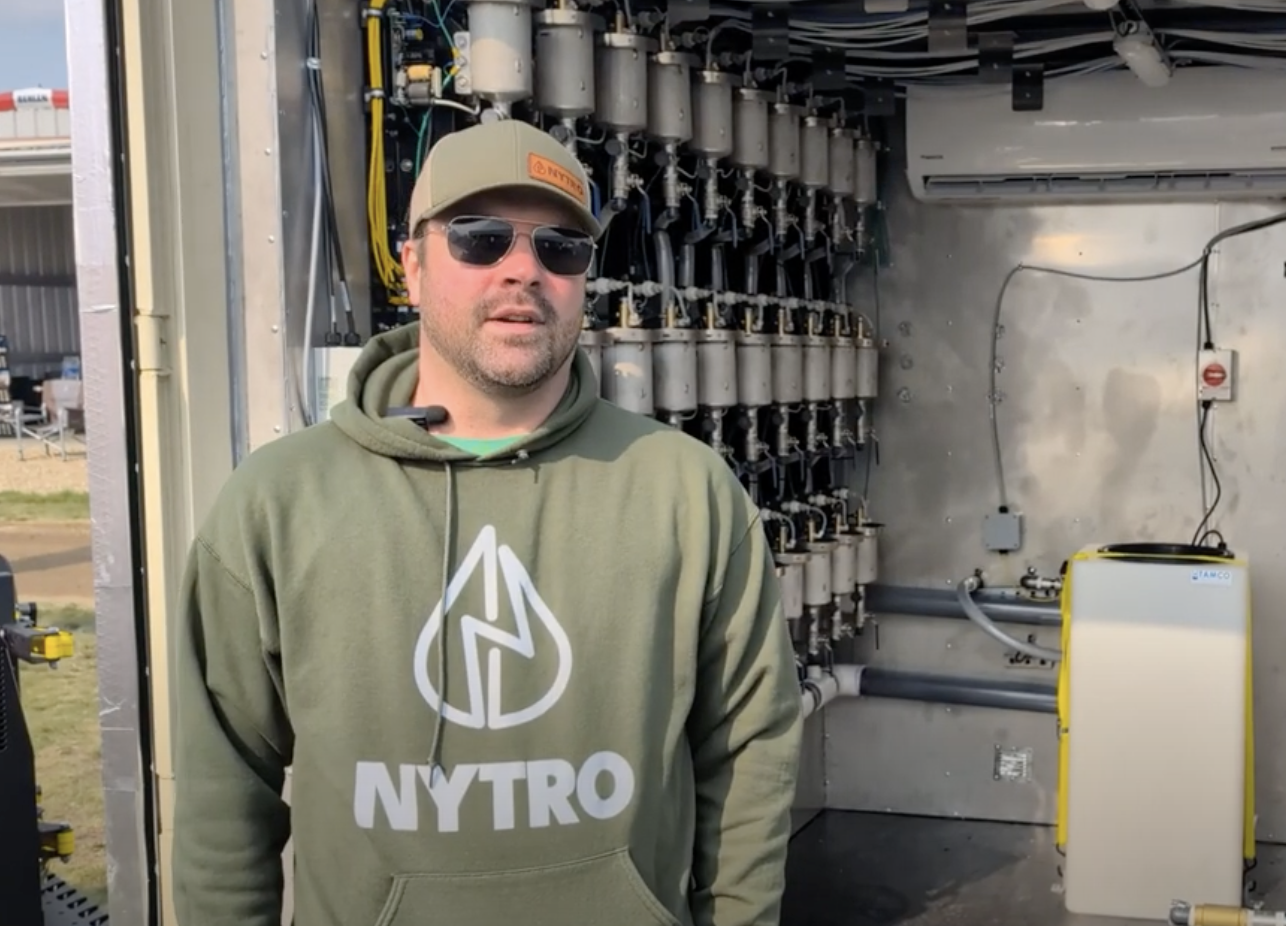
VIDEO: Green Lightning and Nytro Ag win sustainability innovation award
Nytro Ag Corp and Green Lightning recieved an innovation award at Ag in Motion 2025 for the Green Lightning Nitrogen Machine, which converts atmospheric nitrogen into a plant-usable form.
There are other reasons why aluminum welds fail, but cleaning is the biggest culprit.
“When aluminum looks clean and shiny, it’s not,” he said.
“Shine means it’s contaminated. It’s a micro-thin layer of oxide, and you have to get rid of it. You cannot weld shiny aluminum. The best way to get rid of the shine is to mechanically remove it from the weld area with a stainless steel wire brush. Not a regular wire brush. It has to be stainless steel.”
Feal said it must be a dedicated stainless steel brush that has never been used on any other metal.
“Once you brush anything else, it’s trash, or you add it to your collection of regular wire brushes. Then you go out and buy yourself another new stainless steel brush. Only this time keep it under lock and key.”
Problems causelders who try to weld aluminum that has not been correctly cleaned and prepared will immediately notice four closely related reactions:
- They will see a wandering arc and won’t be able to get a puddle started without burning through or distorting the metal.
- The filler won’t blend into the puddle. Instead, it will roll up into a ball.
- The aluminum has surface tension so the material behaves like beads of water on a waxed surface.
- When trying to join two pieces together, the edges curl away from each other and the gap becomes larger.
Visually reading aluminum is tricky because it doesn’t go through the colour changes most other metals do when welded.
If aluminum is over-welded because the amperage and heat are too high, it looks grey to the trained eye. Welders won’t realize they have weakened the aluminum if they don’t notice the colour change, which indicates they have changed the molecular structure of the metal.
“If the parent metal and the filler are rated for 80,000 pounds tensile strength, you can do significant damage with higher amperage,” Feal said.
“If you over-weld, you can lower the tensile strength to 50,000 lb. and not even know it.”
That mistake on an expensive aluminum spray boom or gearbox case can turn a bad day into a worse day.
Feal said experienced welders who have witnessed the results of over-welding now use digital temperature sensors on the aluminum to help them stay in the required heat range.
“If it starts getting too hot, they take a little break. If it’s not hot enough, they turn up the amperage a little bit. Temperature and amperage are so critical with aluminum.”
Gradual pre-heating is essential with aluminum or stainless steel thicker than three-eighths of an inch. Gradual cool down is also important to maintaining the integrity of the weld. Winter welding presents an even bigger challenge.
“If you must weld aluminum or stainless in the winter, make sure the object is brought up to normal room temperature very slowly. Overnight in a well-heated shop is the best,” he said.
“Never take a torch to it when it’s cold. You can create serious stress cracks in an otherwise good component.”
Aluminum welding requires high frequency AC power. Welders using a TIG welder should work with 100 percent pure tungsten electrodes with the green flag.
“The green, pure tungsten has a higher melting point than the red two percent,” Feal said.
“I’ve used the red on thin gauge aluminum up to one-eighth of an inch, but with a lower amperage setting.”
Welders should select a rod that’s a slightly higher grade than the grade of aluminum they’re working with. However, identifying the type of aluminum is difficult, even for the best welders.
“Sometimes you don’t know what the heck you have in front of you, so you’ve got to do everything possible to try identifying the aluminum. If that fails, start out slowly with a safe rod like a 5350. That’s in the middle of the spectrum of the series. Judging by how it performs, you can figure out whether to go higher or lower.”
The 4043 is another safe rod. It’s more malleable and easier to work with and resists cracking.
There is an ongoing debate among aluminum welders about whether to push or pull the pool.
“The jury is still 50-50 on that issue. With MIG, a push technique generally has less penetration. A pull generally has better penetration,” Feal said.
“But personally, with aluminum, I think it’s easier to push the pool than to pull it.”
Some welders say they have had good results brazing aluminum, but Feal isn’t so sure.
“Yes, it can be done, but the results are less than desirable. It’s not as strong.”
Winnipeg Technical College, where Feal teaches, operates as a high school during the day and an adult education school in the evenings. Feal said a lot of farm kids enroll in the courses.
“The farm kids take their welding a lot more seriously than the other students. They’re gung ho to learn metal fabrication and welding. They really investigate things. They want to know why things happen with metals. I suppose, because of their background, they have seen firsthand how important these things are.”