FARGO, N.D. – As air carts get bigger, the logistical challenge of feeding them grows. With a number of carts now at 500 bushels or larger, seeding strategy has become more critical. When fields get muddy, the problem compounds itself.
“Filling has become the most frustrating part of the whole seeding operation,” says Kevin Anderson, a farmer from Andover, South Dakota, and widely known as the inventor of the Anderson Opener.
“We can be running around out there sometimes like headless chickens.”
Anderson, who is also the man behind the Horsch Anderson air drill, one of the largest available, said the challenge with these high-capacity drills is to keep them working.
Read Also
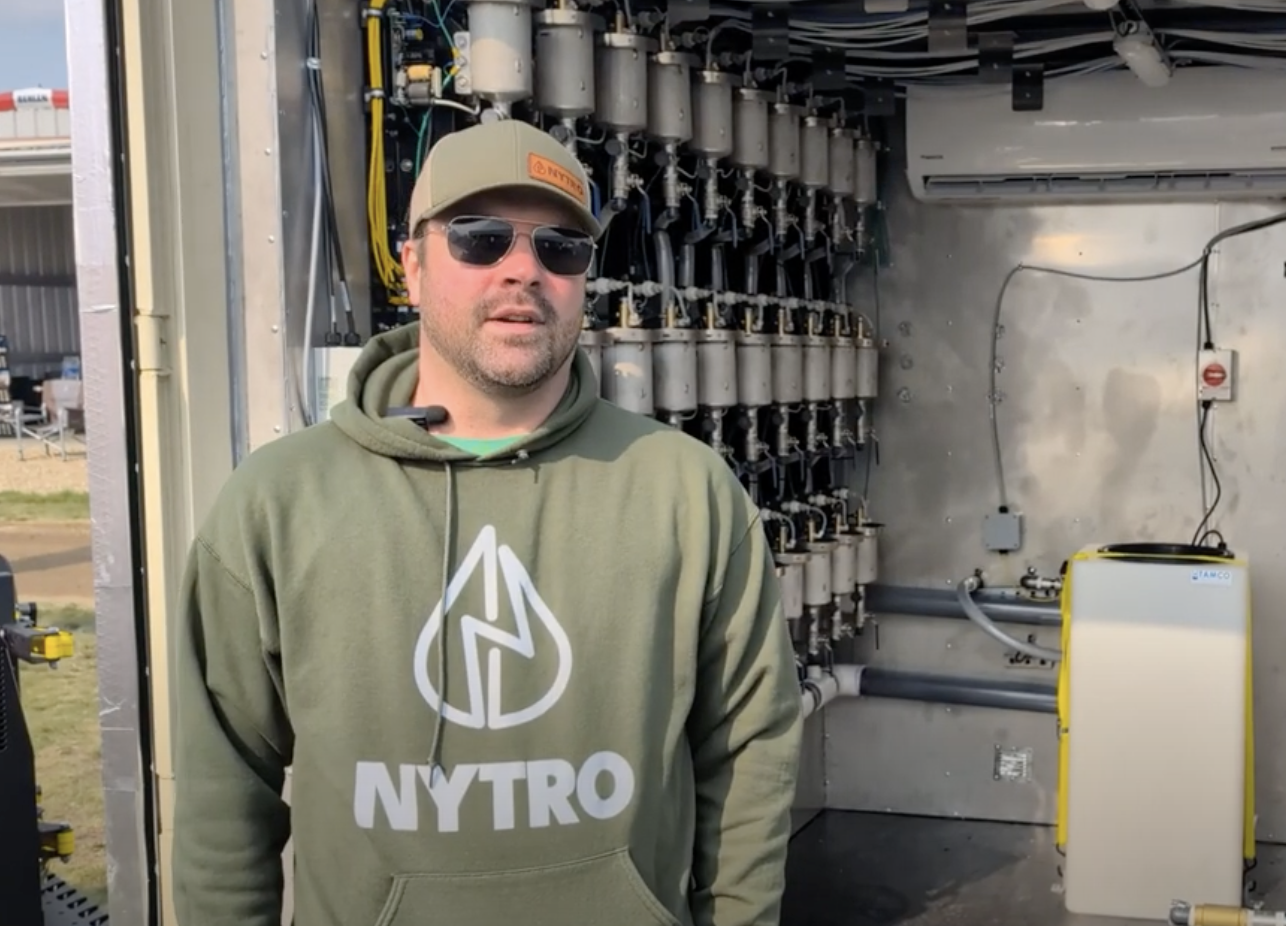
VIDEO: Green Lightning and Nytro Ag win sustainability innovation award
Nytro Ag Corp and Green Lightning recieved an innovation award at Ag in Motion 2025 for the Green Lightning Nitrogen Machine, which converts atmospheric nitrogen into a plant-usable form.
“With a 500 bu. cart, a producer should do 1,000 acres a day with just two men in the field plus a driver for the semi. Now, that’s a long day, for sure, but that’s not working round the clock by any means.”
Anderson’s solution is the Terra Tender, a 750 bu. cart on tracks with three separate compartments that are adjustable to three volume configurations. The three unload augers reduce filling time to three minutes, feeding into a 500 bu. cart. Total time for the stop is less than five minutes.
“You do not want to take the time to drag that expensive drill rig over to the approach at the side of your field,” he said.
“That’s wasting money. You want a system where the drill operator communicates to the tender cart so the tender is always at the exact correct spot waiting just as your product tank needs filling. And once the two rigs are together, you want the fill to be fast. Five minutes max.”
However, Anderson said there’s more to efficiency than fill time.
“You don’t want to stop your drill and trip out of your AB line on the guidance system. For optimal utilization of that big machinery investment, you want to remain locked into your AB line and have the tender come to you.”
Anderson has already sold 30 Terra Tender units.
He said the fill operation is pretty standard. The tender operator backs up to the product cart and turns on the three conveyor belts. He goes up top to make sure everything is lined up correctly and flips a switch to open the slides and begin filling.
Although Anderson has auger and cup augers available, most units are ordered with eight-inch belt conveyors, which are plumbed in series. The combined hydraulic requirement for the three conveyors is 20 gallons per minute. The spouts are designed to make sure that all corners of the compartments are filled.
“Our thinking is that a 500 bu. product cart is big enough for anyone. That gives you 80 to 100 acres per fill at just about any rate. If you get much bigger than 500 bu. for the cart, you’re going to create a whole new set of problems in the field.
“So what we wanted to do was leave the cart at 500 and figure out a way to make it more efficient. Obviously, the way you do that is to keep it moving. Reduce the idle time to an absolute minimum.”
Anderson said farmers who run two or more drills use the Terra Tender differently.
“It’s a different team organization in these situations because the drill operators are no longer the people in charge. Now it’s the tender operator calling the shots. They no longer run a cart until it’s empty. Instead, the tender operator hustles around the field making sure the drills never get close to the empty mark. You put your most experienced person on the tender rather than on a drill.
“In the next few years, the big tender cart will take the position in the planting operation that the grain cart has taken in the harvest operation.”
Anderson said much of the idea for a big tender cart came from watching farmers use their grain carts to feed their drills in extremely muddy seeding conditions.
“That works well if you have no other choice, but that’s not to say that a grain cart can do the work of a tender cart. The grain cart has only one compartment, so it complicates the fertilizer chore. A dedicated tender cart has split compartments to match the compartment sizes of your drill tank. You can easily double up and use your tender cart as a grain cart, but it’s complicated to do it the other way around.”
The Terra Tender has three compartments, each with a big side window that allows the operator to check levels.
Inside are two removable hopper dividers fastened with bolts. The dividers are curved, which means the volume of two compartments can be changed by removing a single divider and flipping it around so the curve faces the opposite direction. Only two sets of mounting brackets are welded to the hopper wall, so no extra protrusions can hang up the product. When the tender is used as a grain cart, the dividers can be removed.
With a 750 bu. capacity, a B-train will fill the Terra Tender twice at seeding. At harvest, two dumps with the same Terra Tender will fill the same B-train with grain.
Anderson admitted that tracks are an added expense, but said they’re worth the money for three reasons:
Wet conditions: “We can build the Terra Tender with tires if that’s what the customer really wants, but we don’t recommend it. The obvious thing is that in wet conditions, you can still move product around on a freshly seeded field without making a mess of things.”
Compaction: “Even in a dry year, you’re compacting your soil when you drag your drill over to the approach six or eight times, or use the approach area to fill a tender on tires. You never get a crop off those acres. Never. But with a tracked tender, you can haul product anywhere your tractor can go and you have no concentrated areas of compaction.”
Overloading: “The other thing we’re seeing a lot of now is big grain carts coming off the assembly line with tracks instead of tires. The tires can’t take the load of a fully loaded 1,000 bu. grain cart. The tire companies are starting to refuse warranty when they know their tires have been overloaded. So the cart manufacturers have no choice when they build the big carts.”
Anderson decided early in the design stage that the Terra Tender must be able to fill itself at the edge of a field as easily as it fills the product cart in the middle of a field.
“For loading the tender, we use a 10-inch conveyor mounted on the opposite side from the three fill conveyors. This conveyor is controlled from the tractor. It has a boot for the bottom of the semi, so when the semi pulls up, the tender boot swings out and takes on whatever it needs.”
The Terra Tender also comes equipped with two winches at the back, allowing the operator to quickly hook up two anhydrous tanks to ferry out side-by-side to the drill.