WINNIPEG – Meeting the letter of the law when disposing of dead livestock has become a complex and costly task for livestock producers.
However, a new composting system developed in Manitoba may have the potential to turn that extra cost into extra profit.
Instead of paying someone to remove dead animals, farmers who use the Biovator can convert carcasses into a composted material that can have commercial value as fertilizer.
“Our largest composter has the capacity to process up to 500 pounds of mortality per day into environmentally friendly material. That works out to 182,000 lb. of mortality per year,” said Biovator representative Shawn Compton.
Read Also
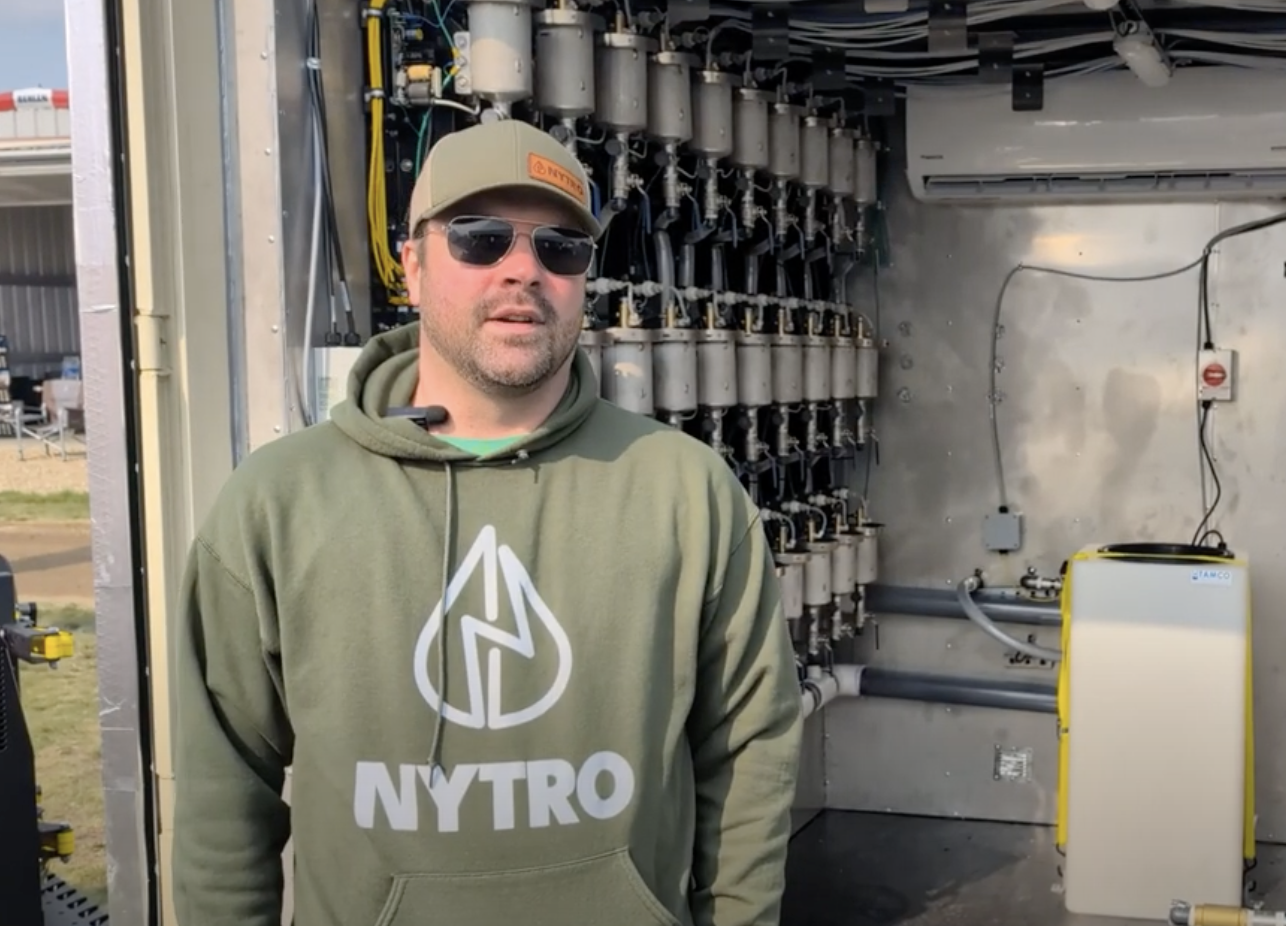
VIDEO: Green Lightning and Nytro Ag win sustainability innovation award
Nytro Ag Corp and Green Lightning recieved an innovation award at Ag in Motion 2025 for the Green Lightning Nitrogen Machine, which converts atmospheric nitrogen into a plant-usable form.
“One ton of Biovator composted material contains 30.4 lb. nitrogen, 5.4 lb. phosphorus, 6.3 lb. potassium and 2.7 lb. sulfur.”
More importantly, he said, the compost is pathogen-free, which means there’s no problem using it as fertilizer, even on horticultural crops that are sold directly to grocery stores.
“Mortality material such as this requires a composting temperature of 130 F (55 C) for a period of three days in order for it to be pathogen-free. In the Biovator, the material is hotter and it’s there for a longer period of time. It’s free of all known pathogens.”
Compton said the long, stainless steel composting tube is more effective and less labour intensive than conventional bin type composters or home-made barrel systems. It also eliminates the health risk associated with hiring someone to drive onto a farm to pick up carcasses.
“Biosecurity is always a concern,” he said. “By managing 100 percent your mortalities on-site, you eliminates the risk of bringing outside disease into your healthy animals.
“The mortalities are totally enclosed in the Biovator, so there’s very little escape of disease-carrying organisms or odour to bother your neighbours. There’s also no problem with insects, wildlife or rodents. And it eliminates the risk of leaching and contamination of water and soil.”
Compton said the final compost product is a dark shavings-type substance similar to peat moss. It is especially good for eroded knolls.
Bones might also come out of the composter, but they are returned for one more cycle to be totally decomposed.
Compton said producers load the composter with equal amounts of dead animals and wood shavings, which is about half the amount of shavings required for bin composting, or half a cubic foot for each pound of dead animal. Producers who don’t have wood shavings can use other carbon sources.
“The drum turns very slowly,” he said. “It’s fully automated, so the timer turns the electric motor on and off as required each day.”
Compton said each animal needs seven to 14 days to fully decompose, but it’s a continuous flow rather than an all-in all-out system.
The producer can add material at the input door daily and remove compost at the far end of the tube, also daily.
Stainless steel paddles on the tube’s inner wall keep the material moving toward the exit.
The Biovator is actually a tube within a tube, with insulation separating the two surfaces. This is necessary to maintain high internal temperatures and allows the composter to function in the winter.
Compton said that during cold weather, warm moist exhaust air from the barns can be channelled to the Biovator to maintain the required temperatures.
The length varies from 18 feet to 42 feet, depending on the needs of the farm. The input and output ends are the same on all units but a longer cylinder is added to increase capacity.
“The diameter is four feet on all the units and they all have two loading doors that are seven and a half feet by two feet. The system has very low operating costs. We add no heat. The process creates its own heat. The only energy requirement is a one horsepower electric motor that runs only when needed. It drives a reduction unit with two gearboxes.”
Biovator has sold 52 units: 20 in Manitoba, a handful in Alberta and Saskatchewan and the rest in Ontario and the United States.
At the entry level, the 18-foot Biovator has an estimated average annual capacity of nearly 65,000 lb, which is enough to handle a 4,000 head finisher operation, a 300 sow farrow-to-finish operation or an 800 sow farrow-to-early-wean operation. The 18-foot model sells for about $28,000, including the skid frame and controls. Compton said the patent is pending and should be issued shortly. While designed for hog producers, he said the composter can also work in poultry operations, slaughterhouses and food processing facilities.
For more information contact: Shawn Compton at 204-371-0115 or visit www.puratone.com.