Transcona, Man. – Horsepower is not the same thing as hydraulic power, a lesson some people are learning this spring as they hook their new upsized air cart to their reliable old tractor.
“There are thousands of 4 x 4 tractors out there with extra horsepower to pull a bigger drill, but they don’t have enough hydraulic power to run the fan,” says Vern Peterson.
Peterson works as an engineer with HyPower Systems, a specialty hydraulic company in Transcona, Man., with seven shops across the Prairies.
Not only are drills getting bigger, but farmers are putting more product down each tube, especially in one-pass seeding operations. Their tractor hydraulics are often maxed out, which costs them in slower ground speed and often a poor seeding job.
Read Also
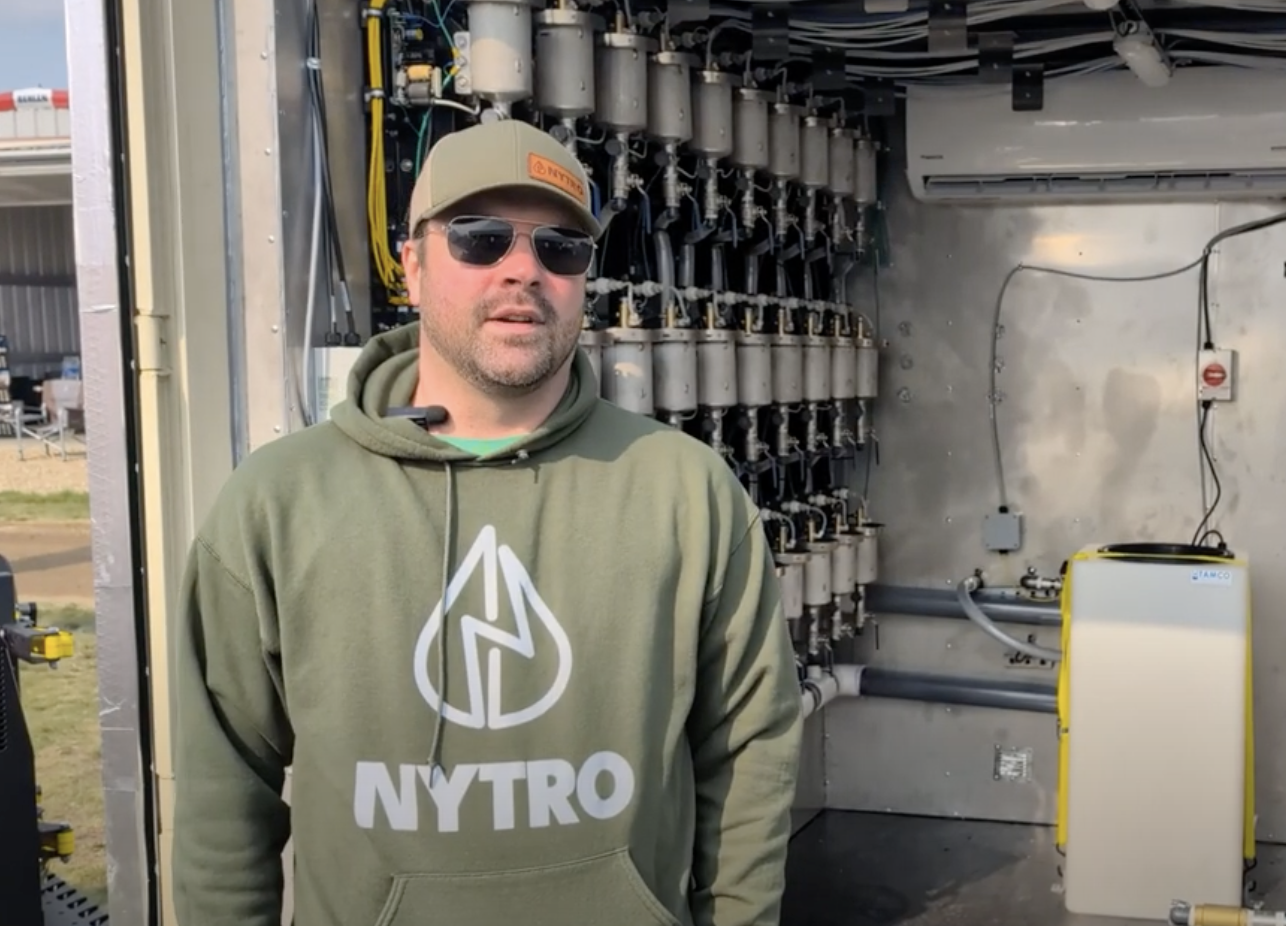
VIDEO: Green Lightning and Nytro Ag win sustainability innovation award
Nytro Ag Corp and Green Lightning recieved an innovation award at Ag in Motion 2025 for the Green Lightning Nitrogen Machine, which converts atmospheric nitrogen into a plant-usable form.
Peterson says producers investing in larger drills, whether a used 60 foot model or a new one in the 70 or 80 foot range, may not be able to afford a new tractor at the same time.
Yet hydraulic demand automatically increases when the drill capacity increases.
Peterson says farmers know that the engine in their 10-year-old tractor has to have enough horsepower when buying a bigger drill, but they don’t always realize how much more hydraulic flow is needed.
“The fact is that many of these tractors have low hours and many years of work left in them. But without a hydraulic upgrade, they can’t handle bigger drills.”
He says the latest generation of grain carts pose similar problems. They have big augers that can plug if the tractor lacks adequate hydraulic capacity.
Peterson says the challenge with tractor hydraulics falls into two time periods. From the early 1990s until 2007, it was usually possible to improve a system without major expense through tuning, tweaking and modifying.
But when the latest wave of big drills and giant grain carts arrived last year, the discrepancy between hydraulic output and hydraulic demand became huge.
At Miller Farm Equipment in Killarney, Man., shop foreman Brian May tells of a customer who bought a new 62 foot drill last fall, with a hydraulic requirement of 24 gallons per minute.
“He was told his Case 9280 had enough hydraulics, but it turns out that was wrong,” says May. The tractor was originally rated at 27 gpm, but with 8,000 hours of use, the pump was putting out much less than that.
“He tried it on his winter wheat last fall and it really didn’t work. When it came time to lift at the end of the field, he didn’t have enough capacity. He had to kick the fan out and then kick it back in after the turn. But you can’t do that when you’re putting on a whole lot of fertilizer. It plugs everything up.”
To find a new pump, Peterson says they got the specifications on the tractor and the drill from Miller Farm Equipment and found a larger pump with the same splines and flange. But, he says, usually it’s not that simple.
Engineers measure the dimensions of a pump in terms of the cubic inches of fluid it will displace in one revolution. The original pump had a displacement of 2.77 cubic inches. The new pump has a displacement of 3.8 cubic inches.
The new pump puts out 30 gpm and can be tweaked to reach nearly 34 gpm. They also called up a bigger charge pump to provide positive flow to the main pressure pump.
May said HyPower’s solution was less expensive than adding an auxiliary pump, but it wasn’t a straight bolt-in swap job.
The pump mounts differently than the original, so they turned it 90 degrees and rearranged the plumbing.
“That extra plumbing definitely drove up the cost. I think the total was about $6,000,” says May.
“He (the farmer) was in just a couple days ago and he says it’s working very well in the field.
“It’s not super fast, but it wasn’t super expensive. If you look at trading up to a newer tractor that was originally built with big hydraulic capacity, you’re looking at a cash difference of $100,000 to $150,000 minimum.
“We also installed an auxiliary pump for another farmer this spring, and I think that ran $8,000 to $9,000.”
Peterson says the trend to bigger drills could mean installing more auxiliary pumps, such as the Atom Jet, on older tractors. Atom Jet is the only pump sold by HyPower and the only auxiliary pump they use when they recommend that a farmer add one. In addition, larger drills could extend the type of work that has been performed for years.
Peterson cited one machining shop that worked out how to install an auxiliary pump driving off the front of the crankshaft.
“It’s a sure-fire cure, but there’s a cost factor when you add any kind of auxiliary pump.”
Peterson says sometimes the solution is complex and costly, but other times it can be a matter of finding the right pump.
“It’s also an easy fix for the handful of tractors built with a (power take-off), but there’s not many like that. And, of course, it’s always a lot more difficult when you have to put the auxiliary pump on the front of the crankshaft.”
One producer devised a solution in which he bypassed the hydraulic motor that drives the power take-off.
To eliminate the double hydraulic inefficiency, he plumbed his auxiliary pump directly into the input line leading to the p.t.o. When he needed the p.t.o., he switched the lines over.
“He basically removed one hydraulic motor from the equation,” says Peterson.
Another solution is to bolt an auxiliary diesel or gas engine to the air cart. The extra engine is dedicated to the fan. Although this system works fine, many producers who tried it have gone back to pure hydraulics because of the added complication and maintenance of the extra motor.
Peterson says that until last year, they were able to solve most problems without adding an extra pump.
“The main component we add is a priority flow divider, something our Saskatoon branch developed. There are thousands of ways to configure a flow divider. The secret is to find the right components for each tractor-drill combination.”
Garett Aubin, a technician at HyPower, says hydraulic flow naturally follows the path of least resistance. If that’s the fan, it can swallow all the oil and leave nothing for the steering cylinders.
“When we design a priority flow divider for any application, we build it so the steering hydraulics always get top priority,” he says.
“The fan gets second priority and the implement cylinders get what’s left over. That could mean your cylinders are slow, but you still have your steering and fan speed. If the fan speed is up so you don’t plug, most guys are willing to tolerate slow hydraulics in the headlands.”
Aubin says he thinks sloppy plumbing is at the root of many hydraulic problems. When the plumbing is cleaned, a bigger drill can be used without expensive modifications to the hydraulic system. He says as tractors and drills get worked on over the years and components are changed, emergency fixes in the field are never properly repaired later.
“Even with an over-sized pump, every system needs smooth, straight lines with gradual bends on the tractor and the drill. You want it to look streamlined,” he says.
“If you have just one undersized hose, it can bring the whole system down to that smaller capacity.”
Aubin says load sensors on newer machines deliver 200 to 400 psi above what the actuator needs.
A poorly plumbed system gives the load sensors wrong information.
“Guys can save an expensive trip to the dealers shop if they just take the time to clean up the system themselves.
“Heat is always generated at the problem spot. Find the hot spot and you find the problem. Keep finding more hot spots until they’ve all been eliminated and you’ll have yourself an efficient hydraulic system.”
Aubin says the quickest way to pinpoint hot spots is with a simple, inexpensive infrared thermometer.
For more information, contact HyPower at 204-231-2328 or visit www.hypower.com.