The big combines that have hit the market in the past few years are working fine, farmers say. Now the headers have become a bottleneck.
The new MacDon 45-foot flex draper is engineered to break that bottleneck by exceeding the capacity of Class 9 combines.
“Until now, producers haven’t always been able to fully utilize the capacity of their big Class 9 and some Class 8 combines,” said Jason Strobbe, MacDon’s product manager for straight cut headers.
“Moving up to a 45 foot flex draper, we deliberately set out to build a header that would exceed the harvesting capacity of most Class 9 combines. Our goal is to be combine-capacity-limited and not to be header-capacity-limited.
Read Also
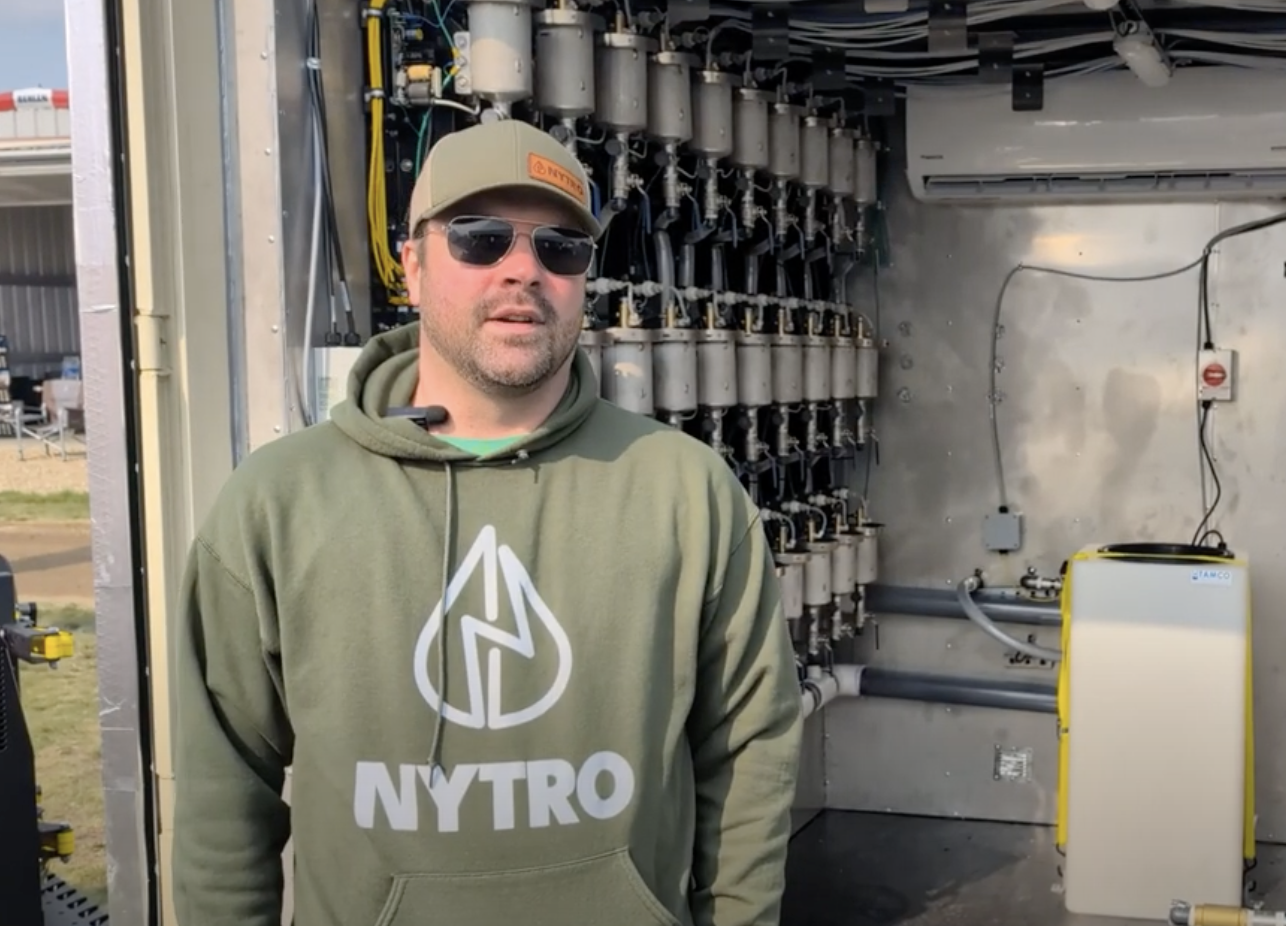
VIDEO: Green Lightning and Nytro Ag win sustainability innovation award
Nytro Ag Corp and Green Lightning recieved an innovation award at Ag in Motion 2025 for the Green Lightning Nitrogen Machine, which converts atmospheric nitrogen into a plant-usable form.
So far with this 45-foot header mounted on any Class 9 combine, we have not been header-capacity-limited in any of the crops we’ve been in.”
Farmers who own MacDon 30, 35 and 40 foot flex draper headers report that they often are able to start earlier in the day and run longer at night. Some report as much as two hours more field time in a typical 10-hour day.
Enlarging the head by five feet means producers should theoretically be able to push 12 percent more crop into a big combine, but Strobbe said going from 40 to 45 feet isn’t as easy as adding 60 inches to everything.
“The 45 foot is a direct result of our latest FD70 design,” he said.
“Engineering used much of the existing design of a 40 foot and some new areas of fresh engineering. Adding five feet sounds simple but it’s never as easy as it sounds. Our goal was to ensure that the 45 would perform as good as the other sizes in the lineup and have the same duty cycle for a long lasting performing product.”
He said that the balance of the floatation linkage contains a lot of flexing technology, which makes the FD work as it does. This technology is also largely responsible for the design innovation award the FD70 received from the American Society of Agricultural and Biological Engineers.
How does a farmer size a specific header to match a specific combine? Is it just a matter of, “oh yeah, this will work?”
Strobbe said some producers still use that method, but there is a better way.
“Typically there’s an unscientific method, which consists of the combine model-size-capacity, topography, ground conditions and, of course, the crops to be harvested,” he said.
“In most situations a producer will do research on-line or with their dealer or with other producers who have a similar combine-header combination. But there’s really no set formula.”
The Float Optimizer header height control is an original MacDon system, which senses the header movement relative to the adapter. It sends signals to the combine software to raise or lower the feeder house, depending on the ground contour, to keep consistent ground pressure across the cutter bar.
Strobbe said it’s a simple system that is not exposed to the elements as is a conventional design and it’s compatible with all original equipment manufacturer combines.
Another aspect of the FD70’s performance on all three sizes is that it provides head-first uniform feeding into the combine, which in most conditions can boost the combine’s capacity by up to 30 percent.
The two-section reel maintains a close relationship to the cutter bar when the header is following the ground. The crop is instantly swept head first onto a live moving surface and into the combine feeder with no hesitation or crop bunching.
The three-section frame is coupled to a linkage system, which allows the header to follow surface undulations closely, and it has minimal friction for instant action.
“This close relationship of the reel to cutterbar and the continuous conveying action is gentle on shatter-prone and short crops. That smooth flow is also why you can start earlier in the morning and harvest later into the evening.”
Strobbe said the FD70’s versatility helps reduce capital investment because the headers handle all crops. An upper cross auger is needed for bulky crops such as canola.
For cereal grain, the header is locked into rigid configuration in seconds without affecting overall performance. This eliminates the need for a flex header and a rigid header for different harvesting applications.
“Producers have claimed fuel savings of up to 10 percent because of the smooth feeding into the combine,” he said.
“Combine drives and increased drive belt life have also been claimed because of the smooth crop flow into the combine. Some operators have said their flex draper headers can be shut down quicker when they see a rock coming into the header. An auger header spins a full revolution before stopping, so it’s sometimes too late.
“With the MacDon header and adapter interface, there’s an area where rocks can roll before entering the feeder house of the combine.”
Strobbe said installation requires no combine modifications. The draper and knife drive system are self-contained, while the reel drive, fore-aft, header tilt and raise-lower all function with the combine’s reel drive system.
The 45-foot header will be available for the 2010 model and $98,000.
For more information, contact Jason Strobbe at 204-831-4531 or visit www.macdon.com.