Swathing lentils is a big pain in the neck, literally. The cutter bar runs right down at ground level, often bouncing into the dirt. In wet conditions it clogs with mud, forcing the operator to continuously stop to clean it out.
For aggressive operators who want every plant stem laid into the swath quickly, the attitude only makes matters worse.
Even in the best of harvest conditions, operators must keep both eyes on the cutter bar, one hand on the hydro, the other hand on the steering wheel and a third hand on the throttle.
Read Also
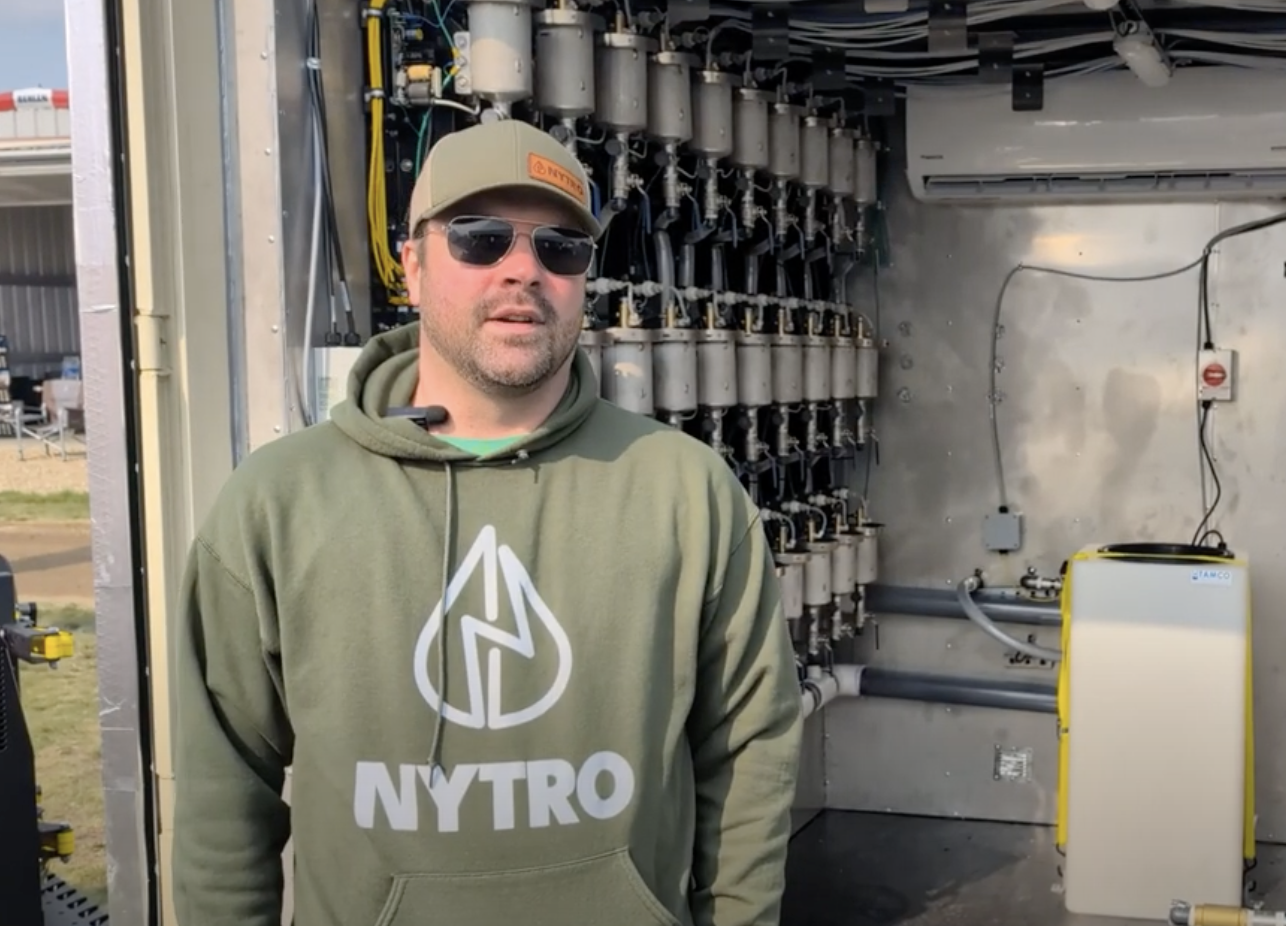
VIDEO: Green Lightning and Nytro Ag win sustainability innovation award
Nytro Ag Corp and Green Lightning recieved an innovation award at Ag in Motion 2025 for the Green Lightning Nitrogen Machine, which converts atmospheric nitrogen into a plant-usable form.
There’s only one way to open a drink or tune the radio: stop the machine and waste valuable swathing time.
It can be enough to make a grown man cry. And to top it off, every operator knows that each acre and each pass are hard on the swather.
Some swather operators seem to have an inherent advantage over others. They seem to run just a little slower. They don’t plug the cutter bar with mud as often. They don’t get mad when things go wrong. Yet they seem to get as many or more lentils into the swath.
Who are these operators? If you ask Laurie Moats or her husband Lee, the answer is that the better swathers are female. The Riceton, Sask., farm couple agrees that women are more patient in the field.
This fall was a prime example, Lee said. Laurie swathed most of their 400 lentil acres without a hitch.
Lee admitted speed is a factor.
“When I get on a machine, the swather or any other machine, I’m what you might call motivated. I’ve got to get going, now. That’s maybe not always the best way to approach things.”
Laurie agreed.
“When we’re doing lentils, I still run the header as low as it can go, but I never seem to pick up much mud. I have to stop once in a while if the knife gets plugged, but not often.
“Lee’s always unplugging because he’s always kind of bouncing along with the field. He goes fast because he’s so impatient. But if you go just a little bit slower, which is where the patience kicks in, you keep the knife out of the dirt. Also, I like to think I put more lentils in the swath than Lee.”
Her husband admited he pushes the limit. He said they both run with the knife an inch or two off the ground.
“But Laurie runs a little slower so she stays out of trouble. She’s just the better operator of the two of us. That’s all there is to it. The next thing I want to do is get her on the seeding tractor. That would be a tremendous help.”
The Moats farm situation is common. Having made a commitment to farming, they have expanded from 840 acres five years ago to more than 2,600 acres in 2006.
Lee has a full-time job in Regina. Family members are available to help some of the time, but most of the field work is done by Lee and Laurie.
Seeding, spraying, fertilizer application, swathing and combining are tasks that require hours of operator attention.
The Moatses know that a conscientious operator can put more grain in the bin and keep the machinery working in the field instead of recuperating in the shop.
“I always enjoyed swathing,” Laurie said. “I didn’t like it much with the pull type, but I really enjoy the self-propelled swathers. The only problem I ever had was trying to go perfectly straight. You want to go perfectly straight and still concentrate on the header hydraulics.”
Lee and the kids addressed this straight steering situation at Christmas 2005 when they bought Laurie a Trimble GPS EZ-Guide Plus with EZ-Steer and T2 terrain compensation. Up to this point, they had farmed without GPS.
They wanted a system that could quickly jump from one implement to the next.
Lee said it’s not often that a product lives up to the advertised claims, but this one does.
“The dealer came out to do the installation and it took him only 15 minutes. When I switch from one machine to another, it really is less than 15 minutes.”
The Moatses looked at all the systems on the market and decided they did not want to plumb into the steering hydraulics.
They wanted a direct mechanical system where the rubber drive wheel actually turns the steering wheel.
They also wanted something that is easily seen and quickly moved from one implement to the next. A main criteria was that it had to work on the hydro swather.
They did a lot of switching in 2006 and the unit logged a lot of acres. The EZ-Steer started in the Deutz sprayer tractor for pre-seeding, then went into the Versatile seeding tractor, back to the Deutz for more spraying, over to the swather, back to the Versatile for seeding winter wheat, then back to the Deutz for fall spraying.
They put more than 500 hours on the system.
“For a while there, I had to spray with my old foam marker system because I had the autosteer on the seeding tractor,” Lee said. “That wasn’t fun.”
With all those lentils behind her this fall, Laurie is enthusiastic about the EZ-Steer.
“I really like it. I set it, push the button and away I go. I concentrate on swathing, not steering. Hands off the wheel. All I have to do is run the hydraulics for the header. It really is that easy.”
Laurie said there’s a nudge button she uses to move the swather slightly left or right on some rounds, but it’s not used often. She is looking forward to next year.
“Lee wants me to get on the seeding tractor next. That’s his plan anyway. But I don’t know if I’m ready. The tractor driving doesn’t worry me. It’s just that seeding is a lot more complicated than swathing. There’s a lot going on all the time managing that drill.”
Laurie’s next major goal is the combine.
“We don’t have the autosteer set up for the combine yet, but once that’s taken care of, I want to run the combine.”
Lee said there are drawbacks to direct mechanical steering systems.
“Installing the brackets on the steering column is a real issue in some machines. There are a lot of implements like our combine, with the steering column inside a shroud or a console with gauges and things. I’ll have to cut into that console and custom build a bracket,” he said.
“Mounting brackets is the other drawback. It’s $100 for a couple of strips of metal with some holes drilled in them. I don’t know. Maybe I was in too much of a hurry to get going or maybe I was lazy that day, but I bought the brackets instead of making them. It would have been a lot smarter to build my own mounting brackets for each machine.”
Although neither Lee nor Laurie had previous experience with GPS guidance, they did field test some systems before making their decision.
“We tried a light bar steering system, and I’d have to say it was a huge improvement over my foam markers,” Lee said.
“Then we tried an autosteer, and that was awesome. If light bar guidance is a big leap over visual, then autosteer would have to be an even bigger leap over the light bar.”
Their entire system cost about $8,000. This price included the light bar, full GPS receiver unit, autosteer, cables and the T2 terrain compensation option. The T2 recalculates the machine’s exact position when it’s running on enough of a side slope to move the GPS receiver off centre.
When pressed on the question of why a farmer at Riceton, Sask., would need a side slope terrain compensation device, Lee laughed and agreed that it’s a fair distance to the nearest hill.
“Actually, flat as it is around here, we can still get some significant side slope driving along a roadway or the side of a drainage ditch or along a creek bed,” said Lee.
“We have some land along Wascana Creek, and there’s been some genuine ditching along there over the years. There’s some pretty steep slopes where we would have had skips or misses without the T2.
“It might be of marginal value in an area like this, but you’ve got to consider how far off your centre line would be with the GPS receiver up on the tractor roof, 10 feet off the ground, and you’re driving along a four percent slope. It makes a difference.”
Lee said downtime was limited to one incident when the light bar wouldn’t power up. On the Trimble, the light bar is the brains of the whole system, so when it goes down, nothing works.
They sent it to the repair shop in Manitoba, which sent a loaner immediately and then returned their original light bar once it was repaired. Total lost time was only a couple of days.
Lee admitted the light bar caused him problems at first, when the suction cup didn’t want to stay stuck to the front windshield.
“Then I took Suction Cup 101 and learned how to clean the glass and wet the rubber cup. After that, it stayed put for six solid weeks through all the fall work.”
He added that the manuals and instructions are good, but not excellent.
A slightly more serious problem is the positioning of the EZ-Steer device itself. No matter how things are arranged in the Deutz, Lee said it’s too easy to knock knees on the steering unit.
He said it becomes less of a problem over time as the operator learns to sit back with hands off the steering wheel.
What’s the payback on the EZ-Steer system?
Lee said, “if we have an annual fuel bill of $20,000 and we cut that by seven percent with better machine guidance, then we’re saving $1,400 a year. So that’s a five year payback on fuel alone.
“When you consider other costs like seed, fertilizer and chemicals, the payback is less than two years.”
Laurie and Lee said an immeasurable factor is less stress on the operator. The other intangible benefit is the ability to put people in the cabs so those machines can run a 2,600 acre farm.