BIGGAR, Sask. – Anyone who has hauled canola seed or granular inoculant bags up an air cart ladder understands the desire to find a better way. Some air seeder manufacturers have devised lifts and other systems, but Richard Elenko came up with his own solutions.
“Most of these air seeder carts have either an eight-inch or a 10-inch auger,” said Elenko, who farms near Biggar, Sask.
“If you’re going to auger a bag of canola, it takes two bags to fill the auger, then there’s all the residuals left in the hopper when you’re done. So most guys throw the bags in the back of the pickup, back up and hand-bomb them up to the top. If you’re putting inoculant in and you’re seeding a couple thousand acres of peas, you know you’ve carried a few bags.”
Read Also
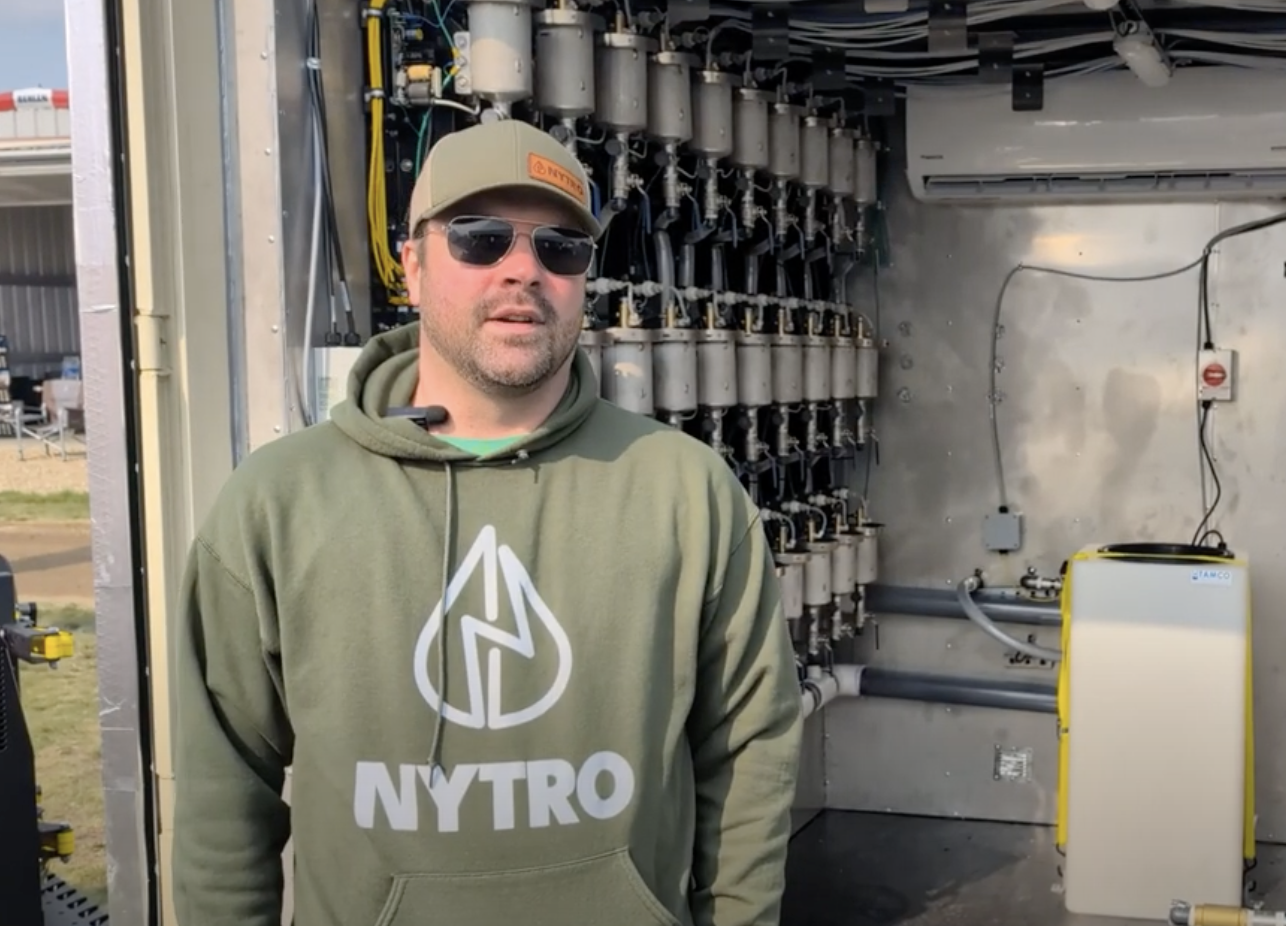
VIDEO: Green Lightning and Nytro Ag win sustainability innovation award
Nytro Ag Corp and Green Lightning recieved an innovation award at Ag in Motion 2025 for the Green Lightning Nitrogen Machine, which converts atmospheric nitrogen into a plant-usable form.
Elenko’s first solution was to put a small auger with a direct-drive orbital motor along the side of the big auger on the seed cart. The smaller auger transfers product from the back of the pickup to the seed cart hopper.
“We thought ‘we’ve got the auger. We’ve got the hydraulics. Why don’t we put a little auger up there?’ So we bought a little four-inch auger for about $300, then we put in a diverter valve.
“We have all the controls, everything is there for the big auger. So we ‘T’-ed into the line, put another diverter on, put this auger on and with the four-inch auger, it will empty. That four-inch auger cleans right out in a matter of seconds.”
Elenko said the way the hydraulic oil flows, he could run the big and small augers at the same time, but he prefers not to.
“If you’re filling grain, you don’t have enough men to be filling both at the same time. Plus, the truck is in the way so you can’t back up to it.”
While the small auger worked fine, Elenko said he thought there had to be an even easier way, because he was still handling a bunch of bags in the field. Over coffee, Elenko and some of his employees tossed around the idea of having a hopper system in a truck.
The discussion led to the current small tender system he carries in the back of his three-quarter-ton service truck.
The tender started its life as the hopper on an old combine. Elenko put a lid on it and built a frame with legs to sit in the truck box. On the bottom, he mounted a manual slide gate, which opens into the bottom of a four-inch auger. The auger folds for transport with a hydraulic ram and a hydraulic motor powers the auger. Hydraulic power comes from a truck-mounted hydraulic system.
“The hydraulic drive on the auger in the pickup has a reducer gear on it and a bypass on the hydraulics. Given the volume and the size of the pump, it gave us a ratio there where we could get by with a smaller pump and better control,” said Elenko.
“You fold the auger out into the operating position, back up, hit the other lever so the auger starts, open your slide gate, the product flows into the auger and up it goes. Because we have to fold it for transport, when we have enough product in the air cart, we shut the slide, the auger empties, then we can fold the auger back hydraulically. One hydraulic control folds up the auger. The other lever starts and stops the auger.”
Once the tender was working, Elenko realized that judging how much product he wanted to deliver would be difficult.
“If you’re going to finish a field, you might only need a little bit. I like to put enough on to dovetail with my fertilizer, so I can keep a check on my calibration. That way, I’m never 100 acres out of whack if something stops or you get a plug.
“So I said, why don’t we put load cells underneath? This thing holds 40 to 50 bushels and if I only want to put enough for 100 acres in, I can do that. With canola, your seed can be below your sensors and you can still seed 20 acres. This way, I can keep track of my calibration, relative to my fertilizer fills.”
Elenko put load cells under each leg of the hopper to measure how much product he puts into the air cart each fill.
The scale he uses sits on the seat in the truck cab. It’s a 12 volt system that can plug into the cigarette lighter or run off batteries.
At this point, he was still using a forklift to bring a pallet of seed or inoculant bags up to the top of the hopper.
But he still had to hand load them into the tender on the back of the truck.
Elenko felt it might be even more convenient to load the tender from the ground. So he built a small, four-inch auger that can load the tender hopper from the floor of his shop.
“We have it in our shop, beside the pallets of inoculant and canola seed bags. We whip in with the three-quarter ton, we have a set of breakaways on the truck that we plug into the hydraulic auger, the guy picks the bags off the pallet and the auger fills the hopper right in the shop. We can load inside, we don’t have to start anything and it’s out of the wind,” he said.
“We have lights on the augers and tender, in all the right places. When it’s night and you’re unloading canola, when we unfold the auger, the light is shining right into the tank.”
The tender typically carries canola seed or granular inoculant out to the field, but it gets used for other products, as well.
“I’ve been short and we needed another 20 bushels of seed, so we whip up to the bin and get it. I’ve used it for flax, lentils … any time I need a last little bit.”
And just because he now has the tender system, that doesn’t mean Elenko has abandoned the small auger system.
“Last year, I was on peas and the truck was tied up with inoculant. The guys were on canola, so they loaded canola seed bags on a pickup and used the auger.”