Experienced no-till farmers say the straw spreader on their combine is the number one item in their implement lineup.
Direct seeding is difficult without a wide and uniform residue spread. If you can chop straw and throw it out in a swath that matches your header width, direct seeding can be achieved without the expense of additional field passes with a heavy harrow, discer or cultivator. As fuel prices rise, extra field passes caused by an ineffective residue manager become more costly.
“The Maximum Air Velocity residue manager is really a zero-till implement,” said Russ Nickel, a Redekop engineering technician who helped develop the new spreader.
Read Also
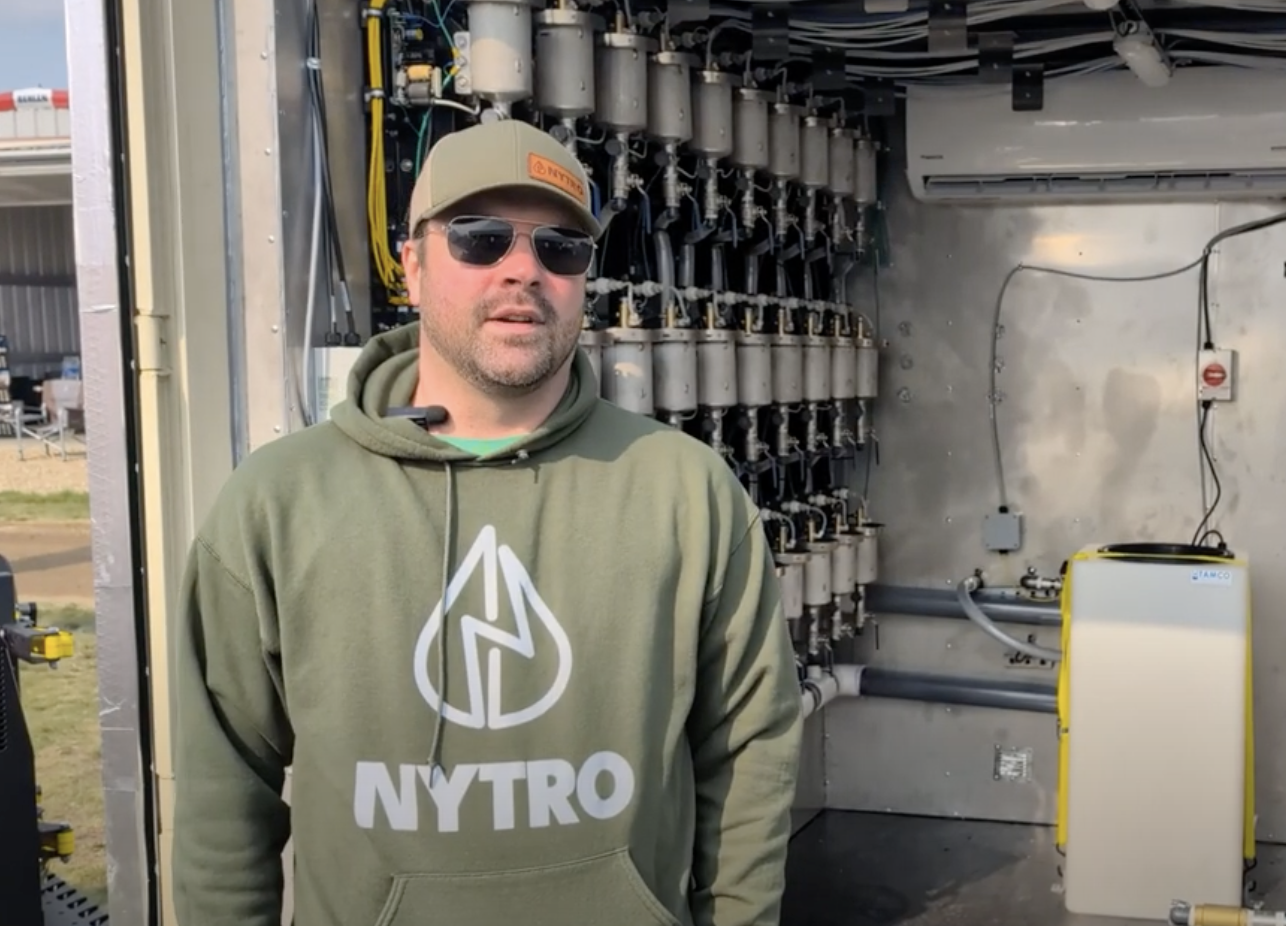
VIDEO: Green Lightning and Nytro Ag win sustainability innovation award
Nytro Ag Corp and Green Lightning recieved an innovation award at Ag in Motion 2025 for the Green Lightning Nitrogen Machine, which converts atmospheric nitrogen into a plant-usable form.
“The message we’re trying to get across is that the tail end of a combine is actually the front end of a direct seeding operation. It’s very easy to seed directly into this fine residue, without additional harrowing.”
As 42-foot combine headers become common, factory spreaders and aftermarket spreaders are only able to provide 30-foot spreads, 36 feet in ideal conditions.
“That spread doesn’t cover the width of the header and that means you either make an extra pass with a harrow or you have difficulty when it comes time for seeding,” Nickel said.
“The MAV gives a reliable 42-foot spread, 50 feet in ideal conditions. We can do this because we have a finer chop and higher velocity airflow.”
The air comes through the chopping zone at 175 km-h, he added.
According to MAV inventor Leo Redekop, residue going through the new chopper is 50 to 75 percent finer than residue from other choppers. He said the only chopper he knows of in the same ballpark was the Swedish-built chopper on the New Holland TX66/TX68, which has since been discontinued.
The unique MAV concept employs two zones. Engineering for the first zone concentrates on chopping residue while engineering for the second zone concentrates on spreading residue. The two tasks are independent of each other.
While many conventional residue managers mount fan blades across the rotor, there are no such blades in the MAV chopping zone. Redekop felt it was inefficient to move solid material with air paddles.
Instead, four rows of paired cutting blades are dedicated to chopping rather than moving straw, using the entire width of the rotor.
The straight blades are 100 percent boron steel and are a bevel-edge reversible configuration. If one side becomes too battle scarred, the knife can be reversed to provide a fresh cutting edge. Optional self-sharpening blades are available. The other significant option is a high density counterknife, called the tight knife bar, for an extra fine chop.
Without fan paddles on the rotor, Redekop had to find another way to generate air movement to move the residue. The solution was to mount six paddle blades at each end of the rotor, outside the chopping zone, which would blast a high volume of air into the chopping zone. These fan blades spin in their own shroud to create maximum air volume and velocity.
“Each piece in the MAV has its own specialty job,” Nickel said.”The cutter blades cut straw. The fan moves air. That’s the way it should be.”
The paddle blades blow air into the chopping chamber from the ends of the rotor. This air flow picks up the finely chopped straw and chaff and carries it out the rear end to the tailboard.
“Because the fans blow in from the ends of the cutting rotor, we have more air flow at the sides than in the middle,” Nickel said.
“But that works out well because the residue naturally flows better through the middle of the rotor than the sides. The sides are where you really need the extra air movement.”
The tailboard is split down the middle, with independent adjustment for each half. This allows the operator to fine tune the spread to match various field conditions. For example, if one side is blowing residue into unharvested crop, that side can be turned down. If the operator is harvesting in strong side winds, the split tailboard can be adjusted to maintain a uniform spread.
The first MAV units were sold in 2004 and had manually adjustable split tailboards. Nickel said future spreaders will feature electric adjustment from the cab. A remote tailgate adjustment kit will retrofit all 2004 units.
Zero till wasn’t the only market Redekop had in mind when he embarked on the MAV project. With the gradual spread of corn and sunflowers into new regions, the company was also looking at the problems with managing these stalky residues.
The new chopper-spreader had to be tough enough to handle corn and sunflower stalks. Where Redekop’s previous chopper had a six-inch diameter rotor, the new MAV is constructed with a heavy seven-inch rotor with a solid steel axle shaft down the middle.
The first MAVs were only available for some models of combines but this year units will be available for all common brands and models found on the Prairies.
Redekop builds two sizes: the 55-inch housing is designed so it can be fitted to all narrow width combines while the 65-inch housing is designed to be fitted to all wide combines. The number of blades can also vary, depending on the intended use.
Producers who want their residue manager to do more work will have to accept that it will eat up more power.
On a few combine models, the original factory straw chopper-spreader drive is left as is. However, most combines require beefed-up drive systems, with heavier pulleys and belts.
“The MAV runs at a higher rpm than other residue managers, so that factor alone requires different pulleys,” Nickel said.
“Plus, you’re running more blades than any other residue manager, you’re chopping finer and you’re creating more air flow. Simple math tells you it’s going to take more power.”
Although maximum benefit is derived from installing the complete MAV modification kit, including the housing and split tailboards, Redekop is willing to sell the rotor by itself for a starting price of about $2,500. The complete kit sells for about $6,800.
Nickel said the company doesn’t expect a big demand for the MAV from areas that typically grow a light crop. He said it’s aimed at producers who want to direct seed, but have to cope with heavy residue.
The other target is regions where corn and sunflower production is expanding.