As we spend long hours on the combine, it’s natural to reflect on the crop production decisions of the past year and what we want to do differently in the next growing season.
Expenses are a big part of decision making and it’s important to look at which expenses were a good investment and which ones did not provide a return.
A producer from west-central Saskatchewan told me that the $250,000 he spent on fungicides this year would look a lot better in his bank account right now. Despite his best efforts, a lot of his crop is going to yield poorly due to disease and flooding.
Read Also
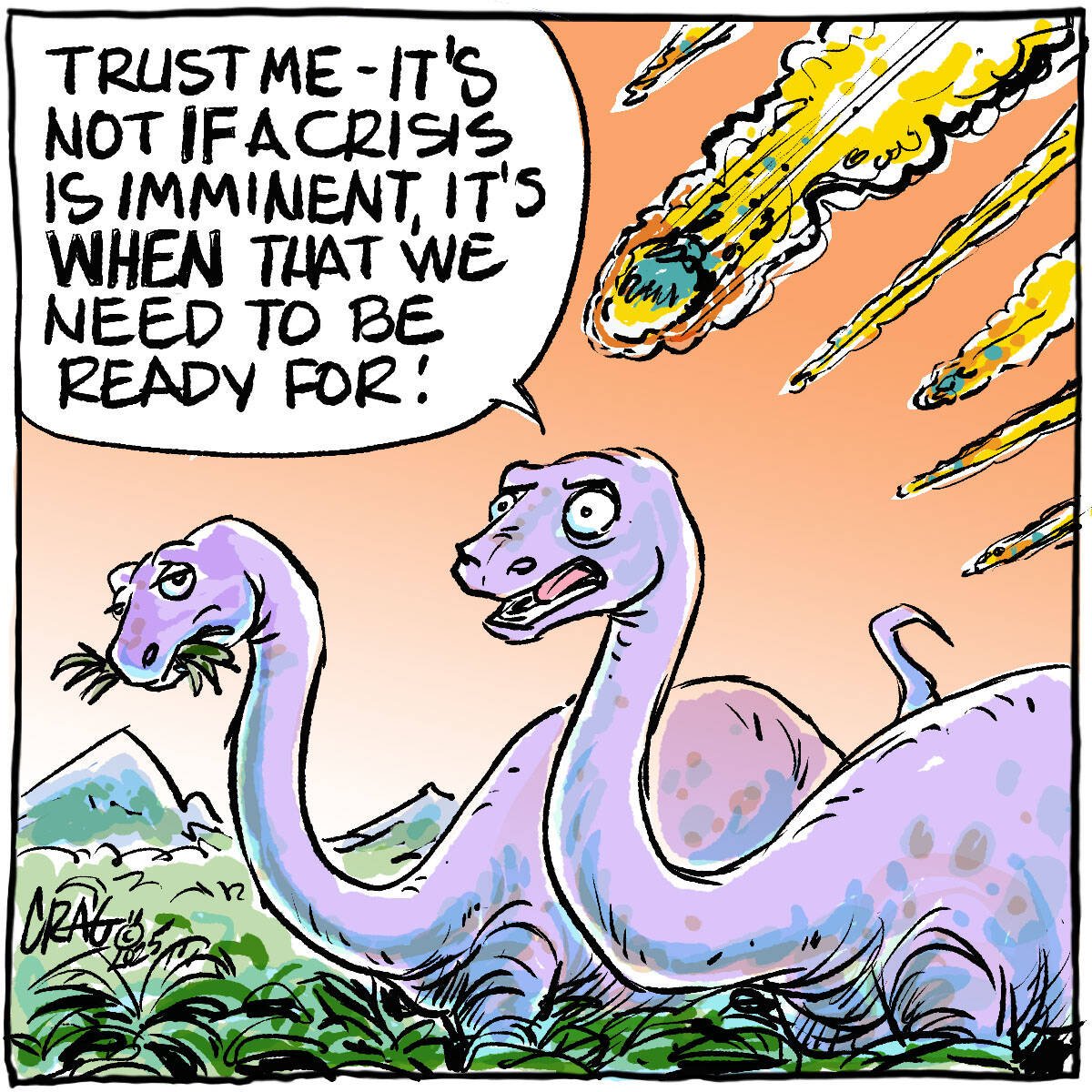
Proactive approach best bet with looming catastrophes
The Pan-Canadian Action Plan on African swine fever has been developed to avoid the worst case scenario — a total loss ofmarket access.
In my case, most of the kabuli chickpeas were sprayed four times, but it has been a losing battle. Most of the pods have aborted due to ascochyta. Some producers have sprayed chickpeas five or six times. Maybe with more applications, the disease could have been held in check.
I’m probably lucky that I didn’t invest in additional fungicide. The crop is still grass green. With abundant August rainfall, it wants to keep growing and is unlikely to mature before the first frost.
In general, fungicides are a difficult investment to assess. You make the application and hope, but it’s difficult to know how much yield or quality you gained. At a typical price of $20 an acre plus application costs, the expense adds up.
Remember the time, not long ago, when most crops were grown without any fungicide?
On the other hand, you usually know whether your herbicides worked. This year, in areas with excess moisture, many fields show spectacular failures. That may spur decisions to use different products, but the value of good weed control is not in doubt.
It’s interesting how some producers will spare no expense when it comes to inputs, but they are Scrooge-like when it comes to employee wages. And then they wonder why they can’t keep and attract workers.
When producers gather to commiserate about expenses, cash rents are not usually part of the discussion. Competition for land is keen and most producers would rather keep this information private for obvious reasons.
But the ticket shock of new equipment pricing comes up all the time. Whether it’s a new combine or just a new header for the combine, the price tag is amazing.
No fungicides are available to control shiny paint disease. It can be difficult to resist the allure of something newer, faster and bigger that has more gadgets.
Equipment costs per acre vary a lot more from one farm to another than input costs. Farmers need to spend money on fertilizer and they need to spend money on weed control. But you can exercise more control over equipment upgrades.
The flip side of that is repair costs. On any major repair job you can’t do yourself, the shop fees and replacement parts often create a nasty bill.
Repair costs have created a throw-away society. Beyond the basics, small engine repair is often uneconomic. A combine that should still have a lot of life left is heavily discounted in value because repair bills could be astronomical.
For a long time, the cost of money has been amazingly low. For years, analysts have warned that interest rates eventually have to rise and we need to structure our businesses accordingly.
The caution may seem like Chicken Little, but it is valid advice. Farm debt levels have been rising and at some point, rising interest rates could become an important business consideration.