If you have to resort to mathematical formulas, you’ve lost your audience. Well, brake systems are all applied mathematics, whether it be fluid dynamics, hydraulics or thermo-
dynamics. Suffice to say that when you push the brake pedal you unleash an impressive
series of actions.
I became interested in brake systems when the brake pedal effort on my car suddenly skyrocketed. I didn’t know what had happened, just that both feet pushing as hard as possible on the brake pedal was evidence
of how scared I was.
Read Also
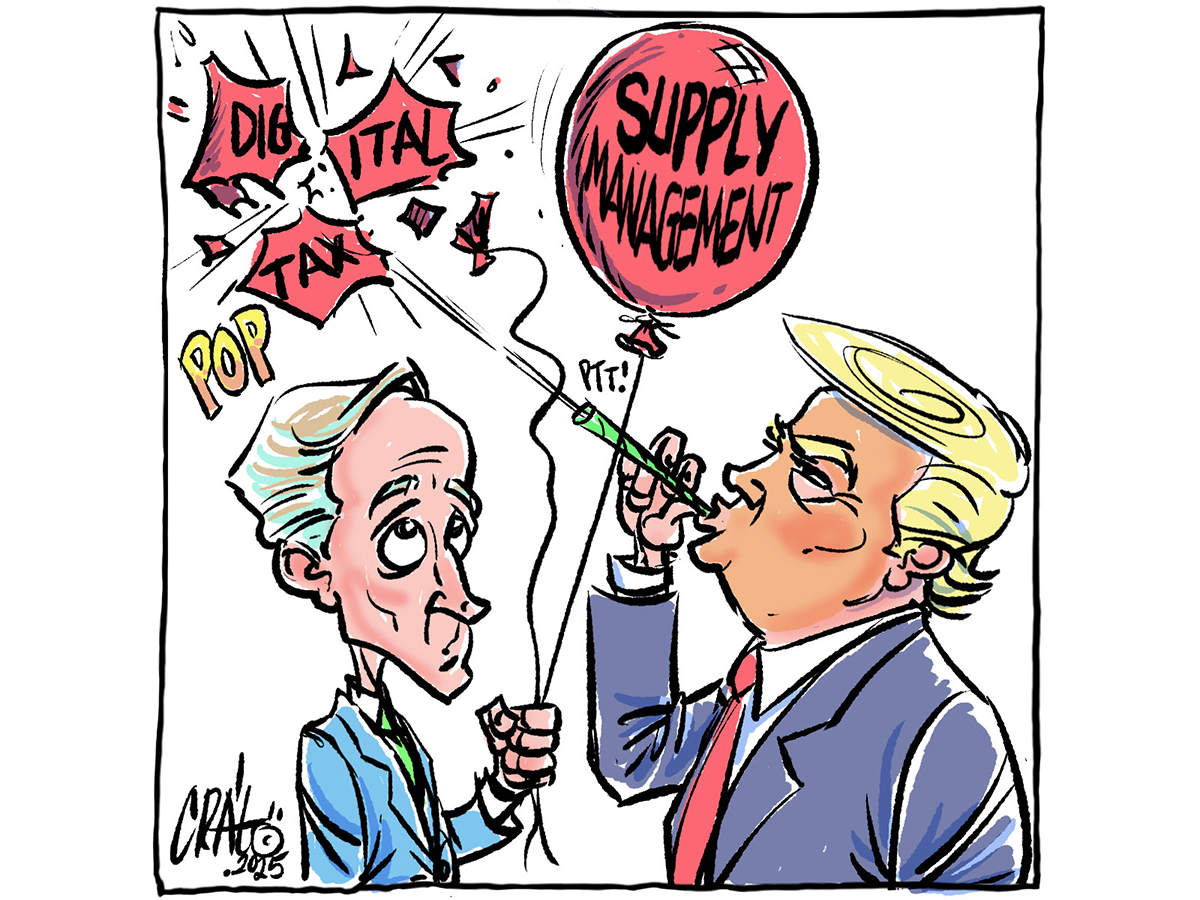
First digital services tax; is supply management next?
If Donald Trump doubles down on his trade threats and targets supply management, Canada will find itself between the proverbial rock and a hard place.
Brakes stop vehicles by changing velocity into heat. How well they do this depends on the mass, or total weight of the vehicle, and on the brake design. The best design for stopping and for heat dissipation is the disc brake.
Components consist of a rotor and a caliper. The caliper straddles the rotor. Pushing the brake pedal creates about 2,000 psi hydraulic pressure so the pads in the caliper are forced onto the rotor. This creates friction and heat, thus slowing down the vehicle. Caliper technology is important because this is the part that generates most of the stopping power and heat.
Nearly all vehicle manufacturers use simple slider calipers because of the low cost. The classic is the single piston caliper that has the piston side fixed to the suspension upright and the other side with a moving arm that slides in a groove. The pad directly pressed by the single piston receives full hydraulic pressure. The outer pad receives mechanical pressure transferred through the sliding arm.
When a driver presses the pedal, he can’t tell that this is a minimum standard until the day comes when the slider grooves have corroded enough that the slider seizes and the brakes don’t work. This usually happens after warranty is up and requires new calipers.
The next big technological step up is the twin piston squeeze caliper, where both pads are pressed against the rotor
by hydraulic force from an individual piston on each side of the rotor. The hydraulic pressure is equal on both sides of the rotor.
Squeezers have been on Porsches, Mercedes, Ferraris and a few others since the 1960s. They are still rare today on other production cars.
From the twin pistons we get into four, six and eight piston calipers, with pistons pressing the pads from both sides of the rotor. Most motorcycles have squeeze style calipers, some with four pistons.
In general, as the size of the caliper increases, so does the amount of braking surface and the necessity of even pressure on the pad to keep wear even and braking forces at a maximum.
Corvette is a classic example of innovation within this theory. The C6 Z06 model uses a six-piston caliper with a little pad for each piston.
If calipers create the friction, then rotors have to absorb it and move the heat away from the pads and caliper. Caliper temperatures need to be kept at a minimum because brake fluid boils at about 200 C.
Boiling fluid creates gasses. Those are the enemy of hydraulic systems and can cause system failures at inopportune times. In addition, debris created by the two surfaces rubbing together has to escape, as do gasses created when the brake pad surface temperature increases.
To perform both tasks, rotors need to be made of a material that absorbs heat easily and evenly and then gives up heat easily. Cast iron readily absorbs heat, gives it up easily and is cheap to use. This makes it the choice of manufacturers.
Aftermarket systems use different materials including aluminum to not only maintain but improve heat loss characteristics. At the top end of aftermarket rotors there are carbon fibre discs just like the Formula One cars use.
Once the material is selected, the design of the rotor comes into play. Vented rotors are hollow so air can flow through while internal vanes direct the air to provide cooling.
One Italian Company, Brembo, casts the rotors with a special pattern that improves heat loss by up to 40 percent over a regular cast iron rotor.
Grooves are also cut in the surface of the rotor, either in straight lines or spirals. This is referred to as radiusing a rotor. Another trick for both cooling and debris removal is drilling holes in the rotor in predetermined locations, called cross drilling.
One thing about brakes is certain: once you hook a trailer behind, you add to the work the brakes must do and you must increase maintenance to keep things working properly.
If you intend to spend most of the time with your truck loaded, you may want to investigate brake upgrades. Better to spend a few bucks on the rig before you set the brakes on fire coming down that long hill.
Another tip for extending brake life – keep your foot off the brake pedal unless you are braking. When you “cover” the brake pedal, you often push the pads out so that they drag on the rotor. This creates heat and excessive wear on the pads. Sometimes it will put a heat glaze on the pads that can cause brake squeal or chatter. It also cuts into fuel economy and at a buck a litre, every little bit counts.
Charles Renny is a freelance automotive columnist and a member of the Automobile Journalists Association of Canada.