BRADA, Sask. – Liquids don’t normally sit well on sharp slopes.
Instead they behave as rainwater does when it washes down the hills to form puddles in a farmer’s field.
It’s a problem when making bottoms for the huge bins in concrete elevators. The floor must be made of concrete, but it must also rise at a 40-degree angle.
How is it done?
The answer seems contradictory: dry concrete.
To pour concrete that will sit at a sharp angle, it can’t have much fluidity. But it still has to be wet enough so the cement can bond the aggregates strongly enough to form a durable bin bottom to bear many tonnes of grain.
Read Also
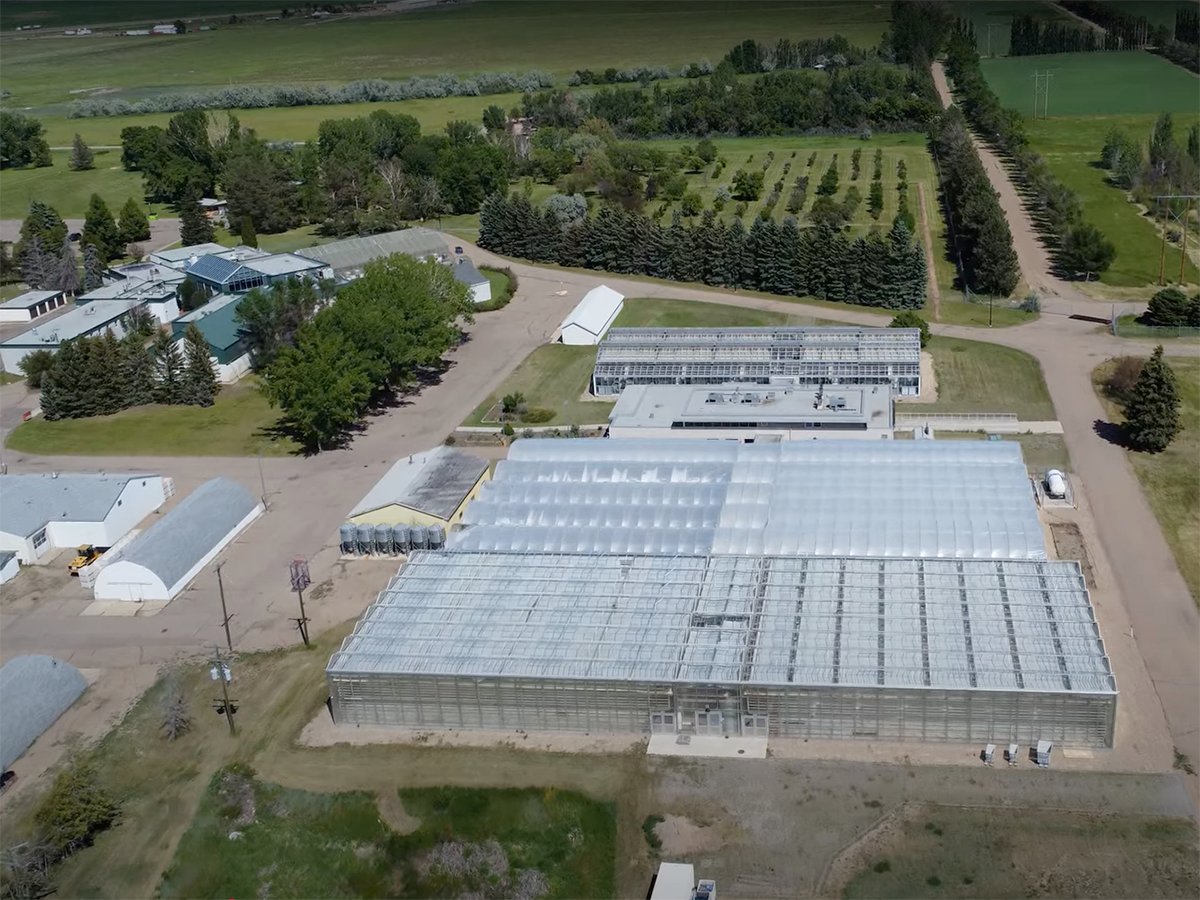
Alberta crop diversification centres receive funding
$5.2 million of provincial funding pumped into crop diversity research centres
“You’d want to have a little bit of input from outside if you were doing it for the first time,” Dave Voxland said wryly. He oversees the Canadian building projects of general contractor J-Sons Inc., the company that is building the network of concrete elevators that Saskatchewan Wheat Pool calls Project Horizon.
Bin bottoms aren’t poured when the main walls shoot up during the week-long miracle of slip-forming. That’s when the elevator rises from a pad on the ground to 39.7 metres high.
Most interior walls are made during slip-forming, as are the long tubes that later become the bins.
Some concrete elevators have all their bins reaching to floor level. To make these bin bottoms, workers can pour a layer of sand into the base, shape the sand to make impressions of the shape of the bin bottom, then pour concrete into the hollows. Once the bottoms have dried, the sand is swept out.
But in the main house of the Sask Pool elevator at Brada, near North Battleford, Sask., that’s not possible. The bins don’t all reach ground level. The bottoms of many will be dozens of metres above the floor.
That means workers have to build wooden platforms on which they’ll pour the concrete. It isn’t an ideal job for people who are afraid of heights.
The wooden platforms support themselves on the crossbeams and steel columns that were put in place during slip-forming. They’re made out of two-by-eights and three-quarter inch plywood.
On top of the sloped wooden platform a lattice of reinforcing steel is arranged. This adds strength to the concrete once the bin bottom is completed, but it also helps hold the concrete on the slope while it’s wet.
Workers use these monkey bars to go up and down the bin bottom as it’s being made.
The concrete gets to the workers through a hose snaked up the outside of the bin and dropped through the “manhole” on top. When the elevator is operational, this same hole will be used to inspect the grain levels.
B in bottoms tend to be poured from the top down. Or they can be started at the bottom, where a thin layer is poured, and worked up to the highest point. Then they can be finished to their full thickness.
The lowest point of the bin bottom has to be clear for the longest time because that’s where the workers get in and out. If they poured the lowest part first and worked up, they’d end up like the proverbial man who paints himself into a corner.
Once the bottom has dried,
the wooden platform is dismantled and the bin is left hanging in the air.
Voxland said all cereal grain
bin bottoms slope at least
36.87 degrees. That is the slope at which most prairie grains naturally slump.
“If you put grain in a pile outside, if you just dump it out of an auger, it’ll form a cone at about that degree,” said Voxland. This is grain’s “angle of repose.”
Practically speaking, that means that grain won’t flow very well from a bin unless it’s sloping that sharply.