Having the right tractor means having the right tires, but choosing the right tires is a complex dance with compromise – power without traction loss, traction without compaction, weight without flotation and efficiency with power.
Tires are often an afterthought until they begin to fail in the field. For some farmers, buying replacements may be based on what is locally available rather than what will best do the job.
Reed Turner, an Alberta Agriculture traction engineer and researcher, says buying the right tires pays big dividends in fuel savings, driveline wear and tire life while maximizing the tractor’s efficiency.
Read Also
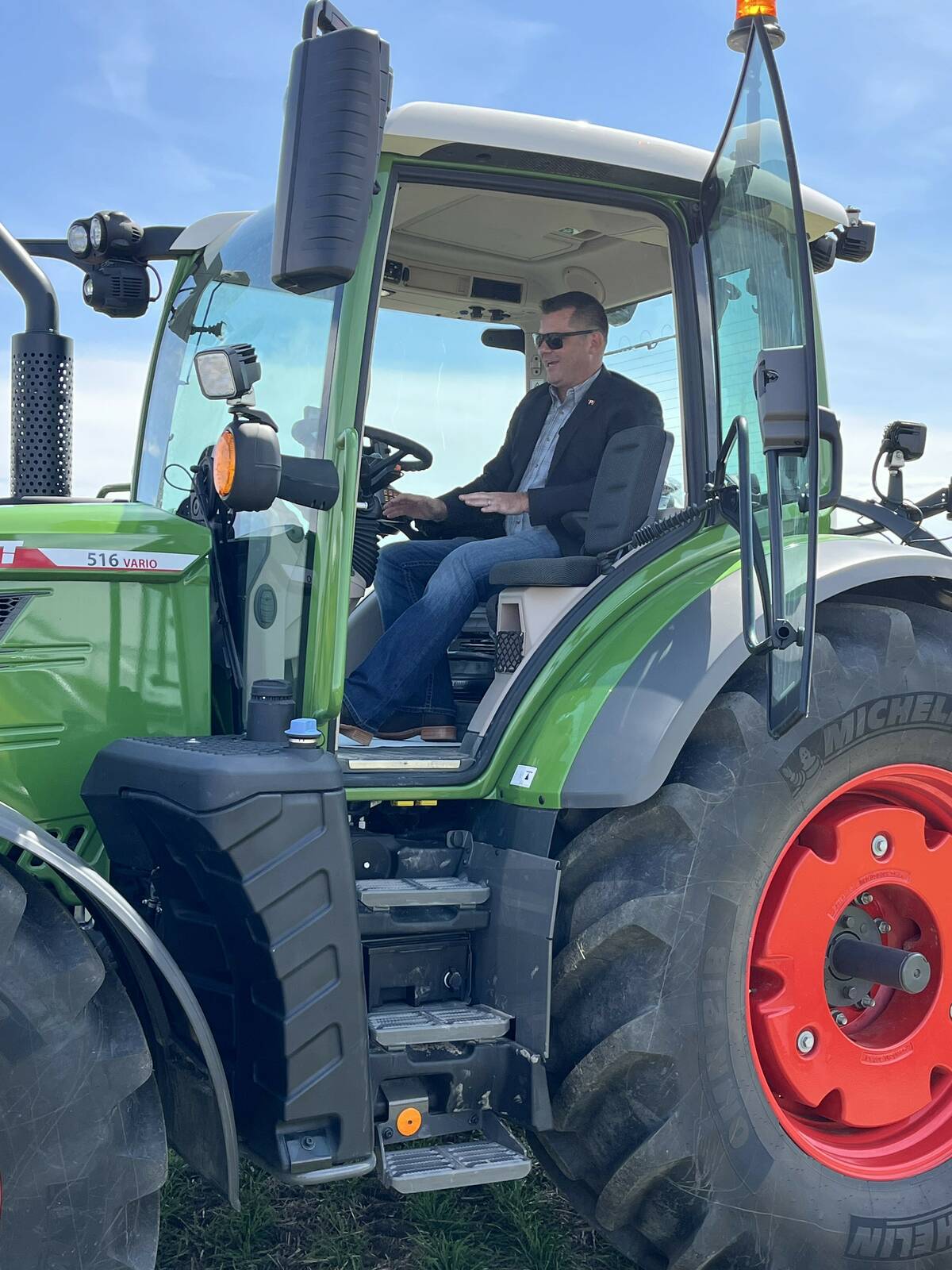
Farming Smarter receives financial boost from Alberta government for potato research
Farming Smarter near Lethbridge got a boost to its research equipment, thanks to the Alberta government’s increase in funding for research associations.
Radial
“Radials, radials. Don’t buy bias ply tires,” Turner said.
“Correctly managed radials outperform bias ply designs every time.”
Radials operate at lower pressures with greater sidewall flex. They can be wider and greatly increase overall contact with the soil, spreading the load of the tractor over a greater area.
Lugs
Long tread lug lengths reduce tire life and efficiency and should be used only in wet conditions. Maximum traction in average dry conditions comes from well-worn tires or those that have shallow lug designs that run as parallel as possible to the direction of travel.
Choosing tires begins by looking at the job the tractor must perform.
According to the Prairie Agricultural Machinery Institute, tractors are generally most efficient when they are pulling a load four-tenths of their own weight and have about 2.5 horsepower per kilogram of load.
Tires can then be sized to carry both the load of the tractor and the draw weight of the implement through the soil.
“Placing the largest individual tires available for each tractor and load is what our testing has proved most effective,” Turner said.
“Two larger duals are more effective than triples with a lower cost and narrower profile in transport.”
He said duals can be effective on the front of mechanical front-wheel drive tractors as well as on drive wheels on four-wheel drive and two-wheel drive power units.
Once the tires’ task is established, tire manufacturers can make recommendations on the appropriate model.
Balancing front and rear
When the new tires are installed, a trip to the local scale, with operator’s manual in hand, is required to balance the tractor’s weight.
“I hear from farmers all the time who are prematurely rebuilding their final drive or planetary gears (final drive planet pinion teeth with face galling),” Turner said. “It’s because of poor weight distribution.”
Every wheeled tractor has a recommended weight distribution between the front and rear axles.
Four-wheel drive tractors often leave the factory out of balance, with engine and drive-train components placing as much as 65 percent of the unit’s weight on the front axle. This must be corrected before the machines go to work. A four-wheel drive tractor should have 55 percent of the weight on the front and 45 on the back.
In a two-wheel drive tractor, an appropriate balance is usually 25 percent to the front or “as little as you can get away with and still steer the tractor.”
For mechanical front-wheel drive or front-wheel assist designs, the ratio should be 40 percent of the weight on the front axle and 60 on the back.
Ballast
Ballast should be applied to the maximum level allowed by the man-ufacturer with regard to engine horsepower, tire capacity and the largest load the tractor will draw.
Turner said liquid ballast should be added equally to each dual tire on an axle, not just inside duals.
“Calcium chloride is the most inexpensive ballast (about 10 times less costly per kg).”
Steel ballast kits cost about $3.25 per kg or $13,000 for an average four-wheel drive tractor.
Speed also comes into play. Faster travel requires less ballast because there is less slippage.
Slippage is not only expected, but is required for efficiency and drive train longevity, Turner said.
A fully loaded tractor that weighs 79 kg per engine horsepower has nearly ideal average traction if it is travelling at eight km-h and its slippage is about 10 percent.
At 6.5 km-h, the same tractor requires 99 kg of weight for each engine horsepower, while at 9.5 km-h only 66 kg per horsepower is needed if it is to maintain the same slippage rates.
Goodyear recommends between eight and 12 percent slippage for four-wheel drive tractors and 10 to 15 percent for two-wheel drive tractors.
PAMI research has shown that between eight and 15 percent tire slip gives the best compromise between tire life, fuel consumption, productivity and driveline component durability.
Most operator’s manuals describe methods of measuring tire slip.
As ballast is added to reduce slippage to ideal levels, tire pressure should be kept at the lowest levels allowed by the manufacturer for the weight of the machine.
Too much air pressure or too small a tire carrying too much weight will result in soil compaction and damaged seedbeds or crop. An overinflated tire decreases the tire area touching the ground and carrying the load.
Too much flotation due to underballasting will result in tire slip and surface disturbance.
Softer, larger tires, less weight, ideal slippage, balanced axles and the right engine for the job can extend tire wear.