REGINA – Most combines waste grain because they are improperly adjusted
or maintained, says combine parts builder George Kuchar of Illinois.
“If there is grain in that field that doesn’t leave through the
combine’s hopper or is damaged, then that combine isn’t set properly,”
said the tall American.
After 11 years as a custom combiner and “many more before that” as a
North Dakota grain farmer, Kuchar began building and selling the
modifications he had developed for his own custom threshing equipment.
Read Also
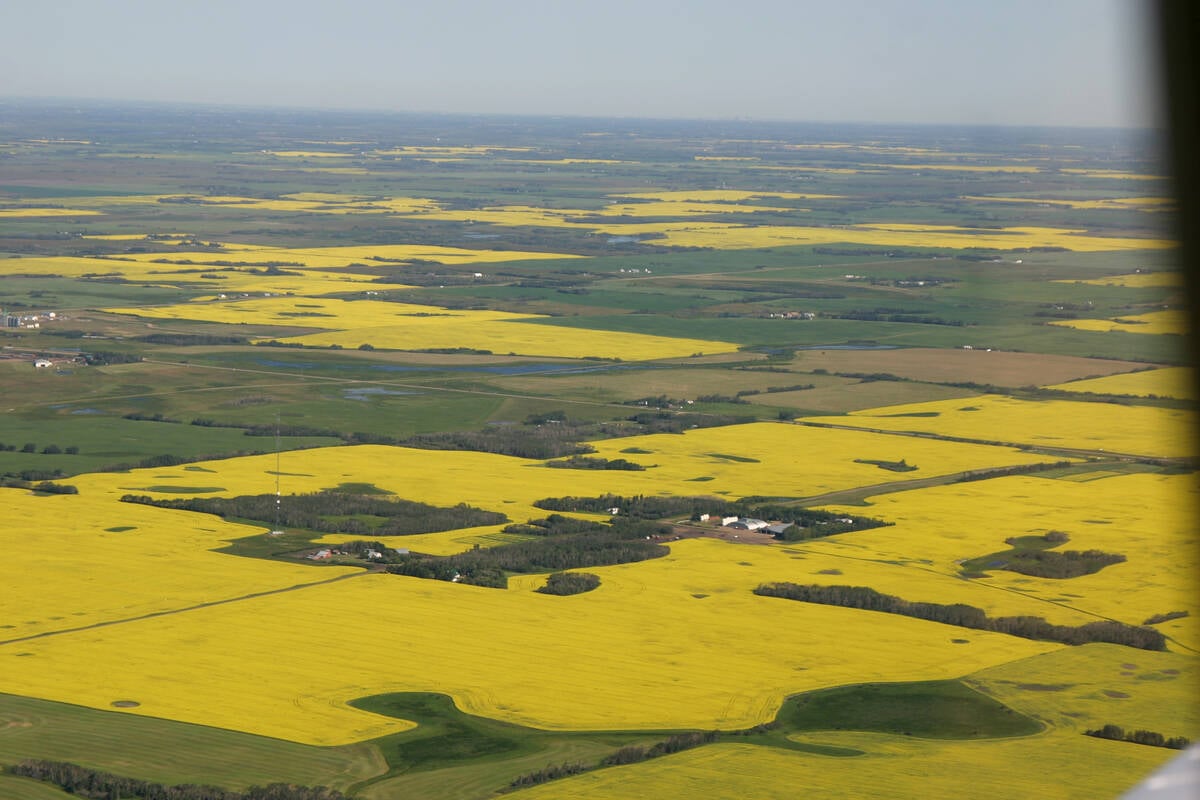
Increasing farmland prices blamed on investors
a major tax and financial services firm says investors are driving up the value of farmland, preventing young farmers from entering the business. Robert Andjelic said that is bullshit.
But he said no modification will improve a combine’s performance unless
the machine is running correctly.
“There is no point to growing a crop only to damage it or leave it in
the field at harvest. It’s like feeding a pig to market weight only to
have it die the week before you were going to ship it.”
Kuchar told farmers attending his seminars on combine maintenance at
the Western Canada Farm Progress Show to evaluate their machines
beginning where the crop “first meets steel.
“It all begins at the sickle. If you didn’t cut it, you didn’t thresh
it. Whether it’s a combine header or a swather, you need a clean cut.”
Sickle timing
Time the sickle in the centre of the cutter head, not at the ends. Poor
cutting or shattering of grain from the heads will occur if the sickle
teeth are not aligned precisely with the cutter bar guards.
“Reel speed is critical to managing the sickle. … It should look from
the side like a giant wheel pulling the combine along. It should be
spinning just a little faster than the forward motion of the machine.
Lift it as high as is practical,” said Kuchar.
Table settings
Tables “should be set to smile at you,” meaning they should be set
lower at the middle where harvested material collects.
Feeding the machine properly begins with the table auger. If the
material doesn’t enter the machine evenly, it overloads some areas of
the cylinder or rotor, or feeds one rotor more than the other.
“It doesn’t matter what type of machine you use, you need to take
advantage of the whole threshing mechanism to get any sort of capacity.”
Kuchar said the table auger should be adjusted to provide 2.5
centimetres of clearance at each end.
“Any tighter and you are pinching the crop material. It rolls, it binds
and fails to feed evenly. All you want to do is get it to the middle of
the table. Let the material that follows push it into the auger
fingers,” he said, demonstrating by pushing the air as if he was
rolling a ball away.
Table auger flighting should reach no more than about 7.5 cm into the
feeder house opening and must be in good condition. Auger fingers
should begin no closer than 45 cm from the end of that flighting.
“All flighting on a combine needs to have a flat, sharp edge. Table
augers are critical for this. Carry a portable grinder with you and
clean it up if it is damaged. When you see material flying up in the
table, this is often the cause …. Straighten any that are bent.
Hard-surface it if you can so you aren’t always spending time fixing it.
“It shouldn’t look like you’re rolling two big ropes up the feeder. You
want it spread across the cylinder evenly when it gets there.
Otherwise, you will not be threshing the grain in the middle of this
roll. And you’re chewing up the stuff on the outside and wasting half
of the cylinder’s threshing area,” he said.
Feeder housing chain
“Set the tension and clearance to manufacturer’s settings. Don’t try to
get fancy here and make sure it is the right way around. So many
machines have them in backwards. You can install them backwards, but
don’t. The crop will slip over the chain and if it is at all tough it
will plug the feeder. When it’s dry it pinches the material rather than
grabbing it and whisking it up to the thresher. You just need to get it
there,” he said.
The leading edge of the U-shaped feeder housing chain bars should be
the taller one.
Concave and cylinder settings
The harvested material should arrive at a concave and cylinder that is
“level and square with equal space on each side in the front … and
always feed the material into a wedge. If it’s a 1/4 of an inch in the
front, then make it a 1/16 at the back.
“When setting the concave, always find the high bar and use it to set
the front and the back, otherwise the grain will work its way to the
widest side and you lose efficiency.
“Canola is different from wheat, is different from corn. Set the
concave for the crop type.
“You need to feed that cylinder to capacity. If it’s running half
empty, then it won’t be doing a job of threshing. The grain is part of
the process.”
He said worn rub bars should be replaced, “no matter how many hours
they have on them. They are cheap relative to the grain you’re tossing
over the back end.”
Straw walkers
Check to make sure they are clean every time you fuel, he said.
Walkers should be clear of bearded heads, straw or corn cobs. Chopper
hammers should be sharp, otherwise they draw extra power and kick
material back onto the straw walkers.
Sieves
“Clean. Clean. Always clean. Air is best and keep any dust buildup out
of here, otherwise they can’t handle the grain.”
A build up of chaff in the sieves will prevent proper adjustment.
“If the spacing varies, the wind will be varied and some grain will be
going over the back end, some into clean grain and the rest into the
return so the machine can have another go at it. Clean grain should go
into clean grain. Nowhere else,” he said.
“Air is the easiest way to separate grain. The more air you can
handle, the cleaner your sample.”
He said if the sieves are set too narrow, the grain winds up being
continuously returned. This results in walker losses, damaged grain and
overloaded returns.
Bearings
“Don’t use a high pressure washer anywhere near a bearing; 3,000 pounds
of water pressure forced into a sealed bearing means that next week or
next month you are changing bearings. Lots of bearings.”
Kuchar recommends using compressed air and long wands for cleaning the
combine in the field.
“Save the high pressure water for the end of the season and then use it
carefully. If you had to take it to the dealer, tell him not to wash it
when he is done.”
Check all bearings, belts, chains, pulleys and sprockets prior to
harvest.
“If it’s worn, loose or in any way not nearly as good as new, fix it or
replace it.”
Monitors
Test all monitors, lighting and global positioning equipment on a few
acres of predictable crop near a home shop where adjustments and
repairs can be made easily and before harvest gets into full swing.
Modifications
“If you are doing everything else,then think about spending money on
after-market modifications. Until then it doesn’t pay,” he said.