‘The circle of agriculture’: Twin anaerobic digesters generate electricity and produce enriched manure
The reuse of material is a key tenet of sustainability in agriculture, and Greenholm Farms, in Embro, Ont., just northwest of Woodstock, has taken that to heart.
The owners, Gord and Laura Green, along with their son and business partner, Dave, have discovered that producing methane to generate electricity on their mixed dairy and crop farm creates what Dave calls the “circle of agriculture,” while offering good financial benefits as well.
“What a great thing,” said Dave Green. “You’re helping cows, producing milk. Now you’re taking the manure that you’re taking from the cow and you’re making hydro out of it.”
Read Also
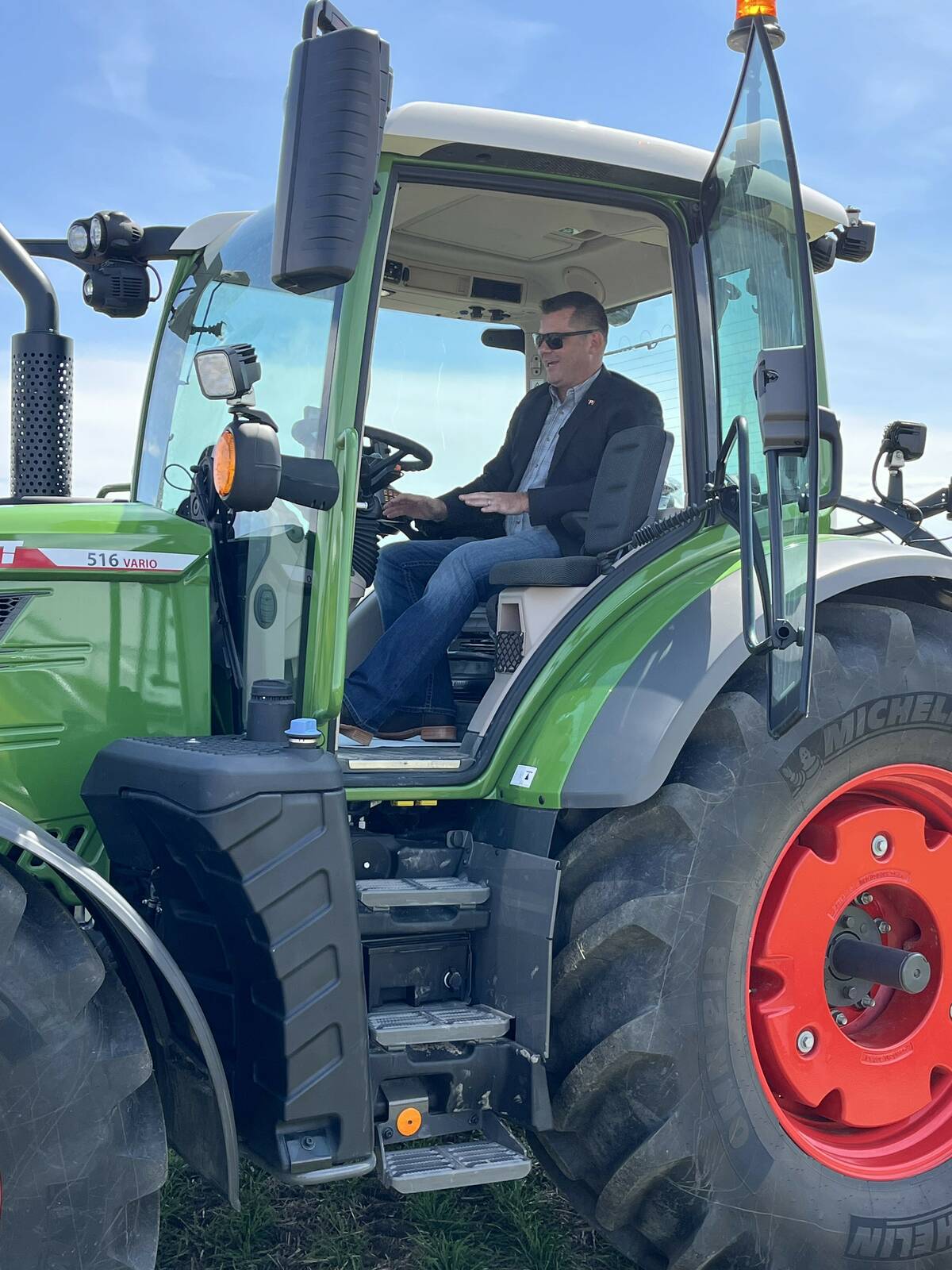
Farming Smarter receives financial boost from Alberta government for potato research
Farming Smarter near Lethbridge got a boost to its research equipment, thanks to the Alberta government’s increase in funding for research associations.
The farm has two anaerobic digesters running full time, producing 500 kilowatts of energy per hour — enough to power about 5,000, 100-watt light bulbs. The energy is sold back to the Ontario government. The cost of running the digesters is about 18.5 cents per kilowatt hour, and the average farm demand is about 30 kilowatts per hour, so there is good room for a profitable venture.
And the end product is manure that is high in nutrients, which serves as good fertilizer for crops.
“(The digester process) makes the manure more like a fertilizer than a manure,” said Green.
“And you talk to a lot of the farmers, they say the same story: ‘man, this stuff really grows good crops.’ ”
“That is the whole circular economy, where we’re making the most out of everything that we’re doing.”
The Greens’ ancestors emigrated from Scotland in 1843, and Dave, who holds a diploma in agriculture from the University of Guelph, is now the sixth generation to work the land. The farm has 250 dairy cows and 800 acres of crops, mainly corn, soybeans, wheat and hay.
Half of the crops are designed for feeding the cows and the other half are cash crops.
While the family members are business partners, Gord focuses mainly on the crops and Dave mainly looks after the livestock.
“My dad was phenomenal for letting go of the reins and giving me free wheel to take things in (new) directions,” he said.
“I think that is a problem that a lot of farmers have.
“Dad … is kind of our main guy for crop decisions and working fields and making those decisions and that’s great. But obviously, we’re working together all the time.”
Dave, 37, enjoys the pursuit of new technologies.
“Innovative ideas, new technologies – that kind of excites me, for sure,” he said.
Green’s thinking on how to approach dairy farming in a sustainable manner has evolved as he learned.
“I grew up working with dad and my grandfather (on the farm) and I fell in love with it. It’s developed over the years.
“I used to be really into the dairy cows and going through 4-H and the show cows, and (I) started to realize there wasn’t much money in the show side of it. I still love working with animals and cattle, but I really got onto making the most profit that I can in a sustainable manner in the progressive side of it.
“My dad has been doing no-till for 25 years. I never even drove a plow; I wouldn’t even know how to do it.”
They bought their first digester under a provincially subsidized program in 2011 and set about learning how to run it.
“We were lucky, we had enough land base and also (the milk) quota that the banks were willing to lend on a new technology,” said Green.
“They were decent about it.”
The second digester was set up four years ago, under Ontario’s now-defunct Feed-In Tariff program, which guaranteed a subsidized price for 20 years, rather than the previous program, which offered capital funding.
Green estimates setting up the methane operation on his farm cost about $2 million.
And then there was the education of a dairy farmer turned power producer.
“It’s been a learning curve, for sure,” he said.
“You’re putting manure (in the digesters), heat it, stir it and the bugs will start to come alive. Normally you want to run it about 38 C, then those bugs will kind of develop and turn into methanogens, and methanogens will eat the organic matter in the manure.
“It takes a month to two months to get the beast rolling. Then you’ve got to be real careful starting to add material to it.”
Learning how to run a digester to produce electricity wasn’t easy, he said.
“I’ve got some years under my belt now. There wasn’t a lot of help at the start because the industry was fairly new, the technology was fairly new.”
Green said digesters are a bit like feeding cows.
“(A cow) loves consistency and it loves the same thing every day. It’s the same thing with a digester. Biology’s a very important thing. If you keep it healthy it’ll produce for you. You can kill it with the wrong material. It’s like a cow with rumen acidosis.”
The mixture of manure and organic matter from industry is key to attaining that consistency.
At the beginning, Green approached clients to funnel organic waste to his operation, but none would commit, instead instructing him to get it going before they would sign a contract to send him material.
So he pursued smaller clients, then he bought a transport truck and trailers and “went out and got this stuff.”
He set up a receiving area for solid organic waste such as material from chickens, bananas, apples, potatoes and feed waste from feed mills.
A sophisticated computer system monitors the digesters.
And since there are now initiatives to steer organic waste away from landfill sites, methane digesters are an ideal fit, said Green.
He has teamed up with other methane producers so they can approach major clients to steer a steady stream of organic waste into their operations.
Aside from providing fuel for the digesters, taking organics from industry allows the farm to collect tipping fees — similar to the charges at landfill sites — which adds to the profitability of the methane system.
The group operation, called Cornerstone Renewables, has helped address the organic feed issue. It’s owned by two beef farmers, six dairy farmers, a greenhouse operator, an agricultural entrepreneur and a research site at the University of Guelph. Some 200,000 tonnes of organic waste are processed at Cornerstone Renewable’s digesters annually.
“That’s a very exciting thing because ultimately, farmers are the solution to that problem (diverting organics),” Green said.
“Because if it’s not going in the landfill, where is it going, it’s got to on the land. Who owns the land? Farmers.
“You used to be able to just dump stuff down the drain and the city would take care of it… But organic processing plants … create a waste product that they had to get rid off. We can take that stuff, run it through the digester.
“The idea that we can feed waste organics to this digester to produce more hydro is basically taking care of waste for them. It’s reducing the environmental impact and it’s making a fertilizer for us to spread on our land. It’s a win-win for everybody.”
The digesters also produce material that looks like compost, which can be used for bedding for the dairy herd, dry cows and the beef operation.
“It saves us a lot in bedding cost and straw; one of the side benefits of the digester that we didn’t foresee.”
Circular agriculture is important because farming is under pressure by a public interested in sustainable production, said Green.
“They’re saying that the dairy industry isn’t very efficient and non-sustainable… Nobody ever talks about the fact that compared to 50 years ago we’re producing twice as much milk with half the cows.… What other industry is able to cut their greenhouse gas emissions with those kind of numbers?”
Green hopes his daughters — Ireland, Stella, Ryerson and Scarlett, aged two to 11 — will eventually take over the farm.
“Do I expect them to take over the farm? No. Would I love it? For sure. If one of them wants to do it, in today’s day and age they can really do it. There are more women in agriculture than ever before … but I’ll help them do whatever they want.”
The next real opportunity for methane digesters is to produce natural gas, which is almost pure methane, Green said.
“You need to be on a high pressure line. It’s developing but it’s going to take a bit of time. It’s more the luck of the location than a lot of things.
“The gas that we produce is anywhere from 45 to 70 percent methane. To dump it into the natural gas line you need to bump it up to that 94 (percent). You do that by scrubbing it and cleaning it. It’s different technology.”
The Saskatchewan Chamber of Commerce recently produced an analysis on renewable energy that contains a biogas component.
Ontario leads the way in methane production on farms with about 20 digesters using manure as the primary feed. Most are on dairy farms, but there are a few on beef farms, and one uses hog manure.
For farmers who are considering methane production, Green advises to get informed first.
“You definitely want to communicate with the guys that have them already to learn whether you want to do it or not.”