Decade in the making | European plant builder saves the day
A biogas co-generation plant is functioning after more than 10 years of running the bureaucratic gauntlet.
Lethbridge Biogas, located in the county just outside Lethbridge city limits, is using manure and other organic waste to produce gas used to generate electricity. The plant began accepting material this spring and is expected to be fully operating within about a month.
Stefan Michalski, a director in the venture, said the plant is the only one of its kind in Canada.
“It was a little difficult to get this done, otherwise this wouldn’t have taken 10 years,” he said Oct. 3 during a tour of the facility.
Read Also
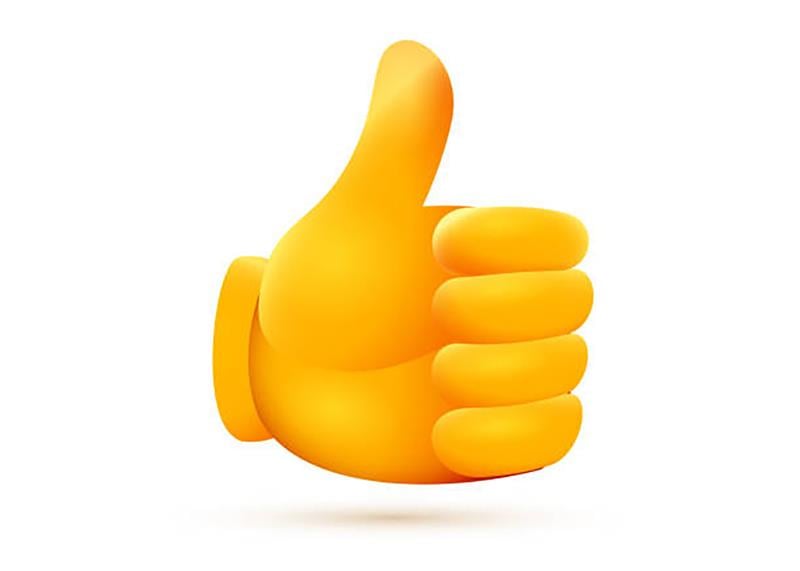
Supreme Court gives thumbs-up emoji case the thumbs down
Saskatchewan farmer wanted to appeal the court decision that a thumbs-up emoji served as a signature to a grain delivery contract.
Local concerns about potential odour, provincial regulations to prevent leakage and federal regulations related to dead stock processing all had to be managed by plant partners.
Additionally there were wrinkles to work through in terms of putting electricity into Alberta’s open market system.
Michalski said a joint venture of local businesspeople was nearly ready to give up on the project when they encountered PlanET Biogastechnik, one of the largest biogas plant builders in Europe. That firm is now a partner in the operation.
Lethbridge Biogas will process organic waste, including livestock manure and all types of food processing material from Lethbridge plants. Availability of feedstock within a small radius was a primary reason for the plant’s location, said Michalski.
Once fully functioning, the plant will also accept dead stock and slaughter waste residue. Its thermal hydrolysis process is a Canadian Food Inspection Agency approved method of destroying prions, the proteins linked to BSE.
The plant will be able to process 120,000 to 130,000 tonnes of organic material per year.
The waste product is put into one of three biodigester tanks, each with a capacity of 4,000 cubic metres. It is subjected to 40 C temperatures in the oxygen-free chambers.
The gas produced by bacteria is used to power two 20-cylinder reciprocating engines that each generate 1.4 megawatts of electricity.
Heat is another byproduct of the process. Michalski said the plant itself requires only about half the heat from one engine, so the firm is exploring ways to use it for drying or providing it to nearby industrial users.
Organic product left over from the process can be used as fertilizer, having been processed into a form more readily accessible to plants.
The multiple types of output are a distinct advantage, Michalski said, adding he is often asked about the plant’s comparison to wind energy.
“Wind is a totally different subject, a totally different ballgame and wind does one thing and one thing only. It generates power, whereas this facility does a lot more.
“It has a waste management aspect, it has a fertilizer aspect, it has a power generation aspect.”
He said Lethbridge Biogas can produce enough electricity to supply the needs of Fort Macleod, a town with a population of about 3,000.
The plant uses state of the art computer technology, enabling operators to run it by cell phone if desired. The four staff might rise to six once it is fully operational.
Michalski said there have been no complaints about odour, an issue that was contentious when the plant was first envisioned. A concrete wall lined with polyethylene surrounds the storage and biodigester tanks, and they sit on a base of condensed clay of the type required for oil and gas facilities.
The tanks themselves are eight metres tall and made of one-foot-thick concrete. They are lined with a double layer of Styrofoam, which is in turn covered with metal cladding.
The material must be stored for about 40 days before it starts producing usable gas that is scrubbed for the engines.
Michalski said co-generation plants are common in Europe. Germany alone has about 6,000 plants, though the Lethbridge operation is bigger than most of those.
Such plants in Europe are offered a guaranteed rate for the electricity they produce, which makes the economics and financing much easier than they are in Alberta.