When Satya Panigrahi looks into the future of agriculture, he envisions a time when prairie farmers no longer use torches and pitchforks to rid their fields of flax straw.
A few years down the road, predicts the University of Saskatchewan researcher, producers will manage their flax straw carefully and sell it for $300 to $400 per tonne.
As well, the fibres derived from flax straw will be used in a range of ecologically friendly products, such as roofing shingles, car and RV panels, water pipes, construction sheeting and cellulose-based building bricks.
Read Also
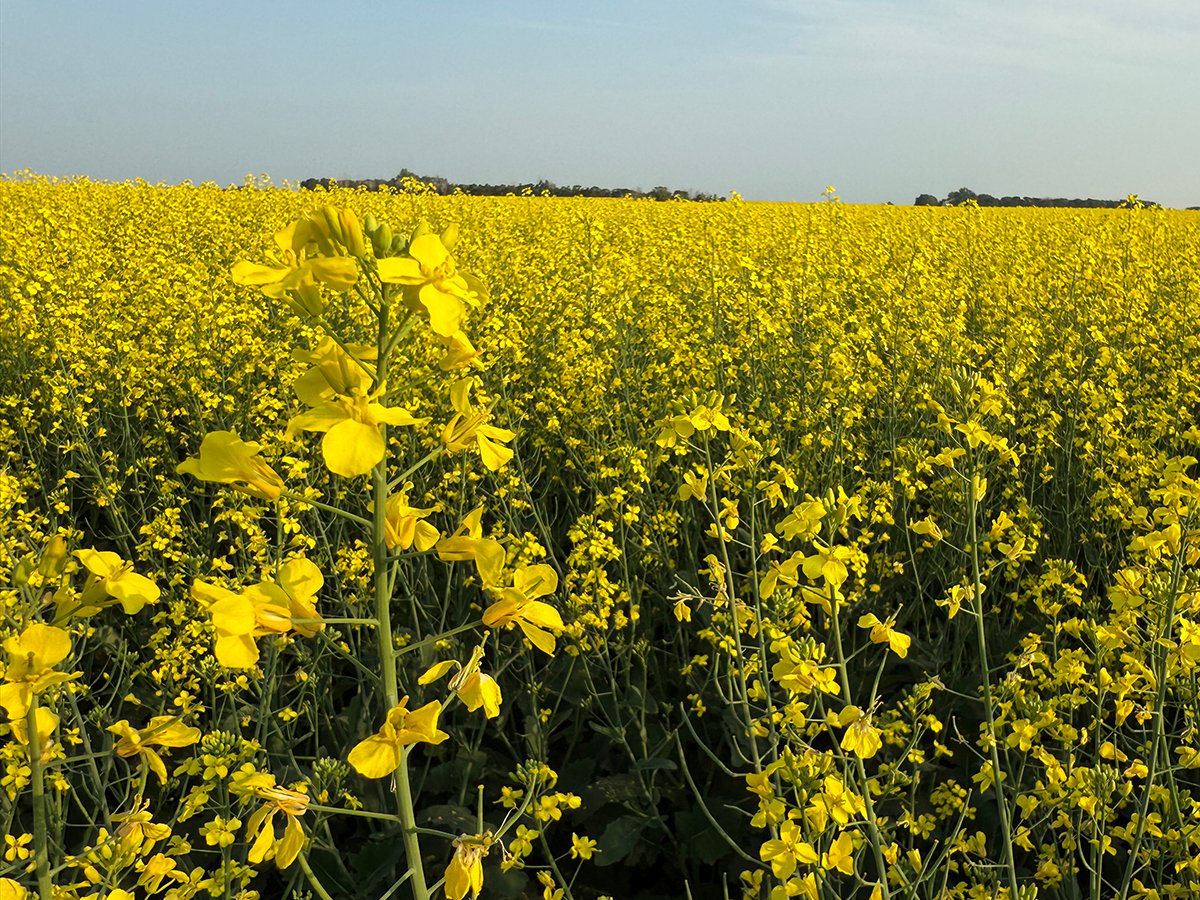
Canola council cuts field agronomy team
The Canola Council of Canada is cutting its agronomy team as part of a “refreshed strategic framework.”
“I am very optimistic because I really believe (that flax based biocomposites) can bring lots of money to our farmers at a very primary level,” says Panigrahi, research chair in material utilization and bioprocess engineering at the U of S.
“Right now, it (flax straw) is being burned. It is mostly being wasted in Canada and North America but in Europe and China and India and many Asian countries, they are very much interested in it for textile purposes.”
Panigrahi has been working with natural fibres, plastic, composites, biopolymers and bioenergy since the early 1990s.
In the past few years, he has focused his efforts on the development of green technologies and ecologically friendly materials that combine agricultural byproducts such as flax fibre, hemp fibre and lentil hulls with recycled polymers and rubber compounds.
His ultimate goal is to develop biocomposite materials that can be used by manufacturers in Canada and around the world.
The development of such materials will provide value-added opportunities for Saskatchewan farmers, enabling them to turn abundant waste materials into potentially valuable commodities.
If private sector investors throw financial backing behind the concept, he said, Western Canada could emerge as a global hub for biocomposite manufacturing.
Panigrahi and his research team are working closely with private sector manufacturers, hoping to learn more about their manufacturing processes and raw material requirements.
He is also working with other researchers to establish a standard process for managing flax straw in the field.
When left in the field, flax straw weathers and breaks down naturally in a process commonly known as retting.
Properly retted flax straw can yield up to 10 percent more fibre, and the quality of fibre is also optimized.
“From one tonne of straw, you can get around 200 kilograms of high quality fibre and that retted fibre will be worth around $800 to $1,000 per tonne,” said Panigrahi, a chemical engineer in the university’s agricultural and bioresource engineering department.
“So it has huge potential for farmers in Western Canada. It could be a billion dollar industry.”
One of Panigrahi’s most promising creations is the Eco-Brick, a moulded building block that consists of processed flax and hemp fibres.
The bricks are roughly the same size as a cinder block but are made from flax that is cut, retted, cleaned and processed into high quality cellulose fibres.
The fibres are mixed with adhesives and other ingredients and then moulded into uniform blocks that can be used to build houses, barns, commercial buildings and warehouses.
The blocks, which have been produced in limited quantities as a pilot product, are fungus, fire and rodent resistant. Panigrahi said their insulative value is rated at R50 and they are virtually indestructible.
To test their strength and durability, the blocks have been thrown from a moving vehicle and subjected to strength and endurance tests at the U of S’s engineering college.
The verdict? Eco-Bricks appear to have a bright future in the Canadian construction industry.
“They are very strong and they have excellent reinforcement characteristics,” Panigrahi said. “They will also reduce dependence on lumber and insulation products so we’re very excited about their market potential.”
In the next year or so, Panigrahi is hoping private investors will turn the Eco-Brick concept into a successful commercial venture.
An unnamed Saskatoon investor has already thrown his support behind the concept and a small-scale plant being established in Craik, Sask., is expected to begin producing the bricks in the next few months.
“We think we have proven the concept … but from a marketing point of view we really need to work on processing development,” he said.
“We hope that if everything goes well … by the end of the year we might see some bricks being produced in the Craik facility.”
Panigrahi said 80 percent of the flax straw produced in Western Canada each year goes up in smoke.
In Saskatchewan, farmers produce one million tonnes of flaxseed a year and burn almost the same amount of straw.
Burning the straw produces significant amounts of carbon dioxide, one of three greenhouse gases that have been identified as a major cause of global climate change.
If farmers could manage their straw properly and sell it as a raw material, they would reduce C02 emissions and reduce the environmental damage caused by crop production.
At the same time, the commercial success of the Eco-Brick would limit deforestation and the use of timber for construction purposes.
Panigrahi is already working on the second and third generation of Eco-Bricks, which combine flax and hemp fibres with recycled plastics and rubber compounds.
Using different moulding techniques, the raw composite materials could be shaped into custom made dimensions to fit almost any application, he said.
For example, the second and third generation biocomposite materials could be custom-moulded into lumber such as 2 x 4s, 2 x 6s, and 2 x 8s.
Flax fibre is also being tested as a raw material in biocomposite sheeting that could one day replace plywood and oriented strandboard.
Panigrahi said government support for the biocomposite industry is gaining momentum and research in the area has garnered much interest from farmers and small manufacturers across the Prairies.
Support from the Saskatchewan Flax Commission, via producer levies, has also been an invaluable source of monetary and moral support, Panigrahi said.
“To have the entire industry behind you is a huge help,” he said.
“If we have that support, and if the government continues to push the fibre industry, within a few years we will see some really good industry in this province.”