Western Canada was two years behind the United States in developing a grain-based ethanol industry but could be leading the charge on cellulose technology, says Doug Soveran, a leading biofuel researcher.
Construction is set to begin on a pilot plant employing a revolutionary made-in-Saskatchewan technology that creates ethanol out of forestry and agricultural waste.
Other cellulosic pilot plants exist in Canada, but none use a gasification-catalyst technology that greatly increases the yield per tonne of biomass consumed.
The pilot plant will be a stepping stone toward a 100 million litre per year plant to be constructed in Nipawin, Sask., in 2009 if everything goes as planned.
Read Also
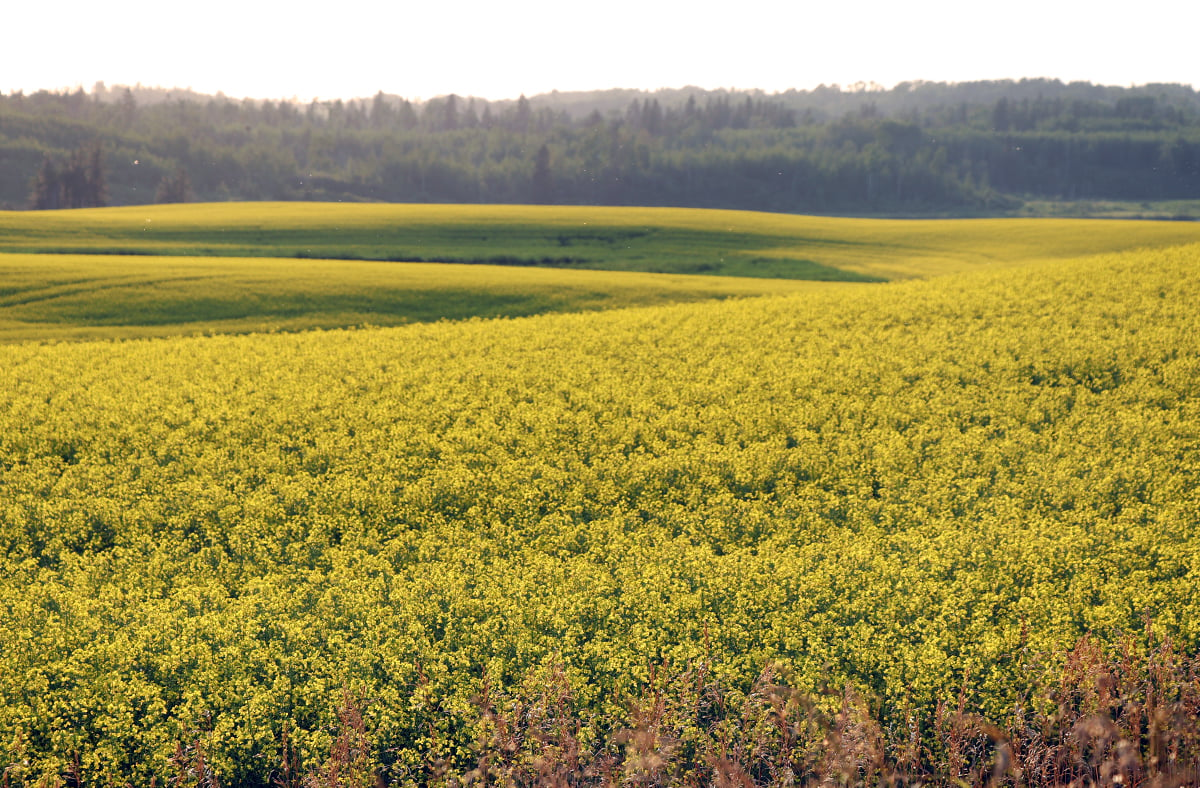
Agriculture ministers agree to AgriStability changes
federal government proposed several months ago to increase the compensation rate from 80 to 90 per cent and double the maximum payment from $3 million to $6 million
“A lot of people talk about (cellulosic ethanol) but I think we’re getting closer to our commercial plant than just about everybody else,” said Soveran, manager of production and processing energy for the Saskatchewan Research Council (SRC), the brains behind the new technology.
SRC developed a catalyst that, when combined with one of the hundreds of off-the-shelf gasification technologies on the market, will deliver 500 litres of ethanol per tonne of biomass. That compares to 300 litres for grain-based ethanol and 350 litres for competing cellulose technologies.
The plant would gasify forestry and agricultural waste material by heating it to between 800 and 1,300 C until the material falls apart into its basic components: carbon dioxide, carbon monoxide, hydrogen and water.
“Then you can make anything you want,” said Soveran.
SRC has created a catalyst, essentially a charcoal-like substance coated with metal additives, that facilitates a chemical reaction that reassembles the basic compounds into ethanol.
Most other proposed cellulosic ethanol plants plan to use an enzymatic hydrolysis process to squeeze fuel out of crop residue and forestry waste. In that process, the lignin in the material goes through untouched.
Gasification technology delivers improved yields because there is better use of the biomass. There is little leftover material to find a home for, just a little harmless ash that can be spread on the ground.
Soveran is confident a commercial-scale plant employing the technology will be able to produce a biofuel that will be cost-competitive with regular gasoline without government assistance.
“You don’t need the subsidies for a cellulose plant. That’s the reason we’ve gone down this path,” he said.
Sherry Michalyca, spokesperson for the Nipawin Biomass Ethanol New Generation Co-operative Ltd., said the commercial-scale plant is expected to cost $180 to $200 million to build.
The original concept four years ago was to construct a 75 million litre facility but with the SRC’s ability to turn one tonne of biomass into 500 litres of fuel, the co-op’s 140 area shareholders decided to scale up to 100 million litres.
The plant will require 150,000 tonnes of biomass per year, three-quarters of which will be wood residue and the remainder agricultural residue, mostly flax straw. The Nipawin region has the ability to produce 500,000 tonnes of biomass per year.
Michalyca said the plant is only one piece of the venture. The co-op intends to aggressively market the catalytic technology it co-owns with SRC.
“That is a real asset and an opportunity,” she said.
The group feels there is probably room for nine other similar-sized plants in Saskatchewan’s boreal forest using the new technology.
Before financiers provide capital for a commercial-scale plant they want to see SRC’s technology in action in a demonstration plant. The co-op is selling class C shares to raise money for such a plant, which is expected to cost $5 to $6 million.
Construction will likely begin in the next two to three months at the SRC’s facilities in Saskatoon or Regina.
Investors want to determine how long the catalyst will last. The hundreds of cubic metres of Aspirin-sized tablets are worth millions of dollars.
“There’s no reason why it shouldn’t last three years,” Soveran said.
He expected they will need to run the pilot plant for only a few months to generate the proof that investors require, paving the way for construction of a commercial-scale plant in 2009.