From the frying pan into the pump could be the new slogan for the first company in North America to make diesel fuel from canola oil.
The pilot plant at Foam Lake, in east-central Saskatchewan, is primed to produce its first batch of the biofuel early this spring.
Zenneth Faye, an adviser to Milligan Biotech Inc., said the shareholder-owned company is getting ready to fire up equipment incorporating new technology developed by Agriculture Canada and the Saskatchewan Canola Development Corporation to process the environmentally friendly fuel.
Read Also
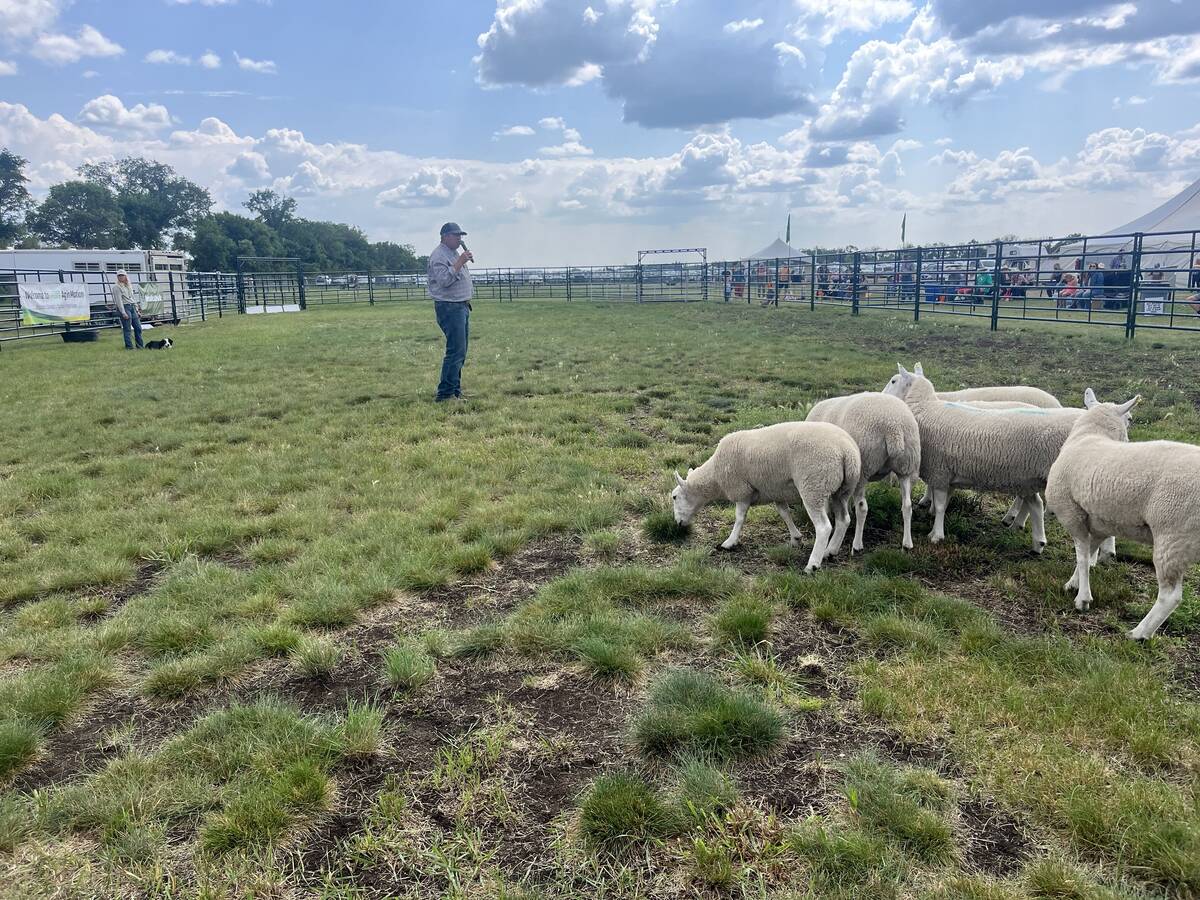
Stock dogs show off herding skills at Ag in Motion
Stock dogs draw a crowd at Ag in Motion. Border collies and other herding breeds are well known for the work they do on the farm.
Some 150 shareholders in the Foam Lake area raised enough seed money to finance the business plan.
Helgi Helgason, chair of the board of Milligan Biotech, said the company wants to keep ownership in local hands.
“Raising the money here locally with shareholders is the first objective but we know there is interest from some of the bigger corporate players,” he said.
The plant will start small in May, processing about 65 bushels of canola a day. The production will be used mainly in research trials.
But the group has bigger plans. In two years, it wants to raise $2.5 million to expand the plant, allowing it to crush 30,000 tonnes of canola to produce 10,000 tonnes of diesel annually.
Turning canola oil into biodiesel involves removing glycerin by adding methanol or ethanol and a reacting agent to create a chemical reaction that causes the glycerin to settle to the bottom of the mixture.
New technology is expected to cut production costs by 20 percent compared to traditional methods, said Faye, who is also a director of the Saskatchewan Canola Development Commission.
The new venture faces a major challenge in securing a consistent supply of lower grade canola to process.
“We wanted to be able to do something with the badly heated canola that’s just being dumped for garbage at this time and give it some salvage value,” Helgason said.
The company will pay farmers a minimum of $200 per tonne for low grade canola, which has been shown to produce the same quality of biodiesel as regular canola. The difference is in the recipe, Faye said.
According to figures from the Canadian Grain Commission, on average about 12 percent of canola in the system, or 700,000 tonnes, is a lower grade, Faye said.
“We could take that spoiled seed rather than the crusher worrying about having to blend it.”
Researchers are probing the possibility of using recycled oil from fast food outlets, now used as a protein enhancer in pet food.
Companies that work in environmentally sensitive industries such as mining, shipping, forestry and recreation might pay extra for a fuel that burns cleaner and won’t damage the ecosystem.
“That is where this product will shine,” said Faye.
Emissions cut
In a 20 percent blend with regular diesel, the canola fuel cuts particulate emissions by 31 percent, carbon dioxide by 21 percent and hydrocarbons by 47 percent, according to Rod MacInnes, manager of the Saskatchewan Canola Development Commission.
New legislation forcing mining companies to decrease particulate matter levels is expected to boost prospects for canola diesel producers.
“If petroleum diesel is no longer acceptable, there is an opportunity for biodiesel as a potential remedy for underground mines,” said MacInnes.
Although he wouldn’t be specific, Faye said forestry companies in British Columbia have expressed interest, as have players in the west coast shipping industry.
Easy clean up of spills is one reason for the interest.
“In 21 days, (a canola diesel spill) will be 100 percent gone, totally part of the ground.”
Because of the high cost of oilseeds, the cost of producing canola biodiesel is about 45 cents a litre or one and a half times more than regular diesel, Faye said. At the pump, 100 percent canola biodiesel would sell for around 90 cents to $1 per litre, depending on the amount of federal tax applied.
The company hopes to cut costs by selling canola meal and glycerin byproducts. Faye said products such as dry cleaning fluid, solvents and paint remover can be made if the biodiesel undergoes a second chemical reaction.
There are three plants in the United States where soybeans are used to produce biological fuels. The practice is more widespread in Europe, encouraged by higher gas prices and government subsidies on oilseeds.
Faye said a major burst in demand for the fuel could not be met by today’s canola production levels.
Even if canola production in Canada grew by 11 percent and the entire crop went into the production of biodiesel, there would only be enough to supply the country’s small vehicle road traffic, he said.