The world has a few problems with plastic, or more like a few billion problems.
To name a few:
- The Pacific Ocean has something called the Great Pacific Garbage Patch, an area the size of France that’s infested with plastic bottles, plastic garbage and microplastics.
- In 2019, the world produced 368 million tonnes of plastic, and estimates from National Geographic suggest only nine percent of all plastic is recycled.
- It can take 400 to 500 years for a plastic bottle or plastic coffee pod to decompose in a landfill.
Read Also
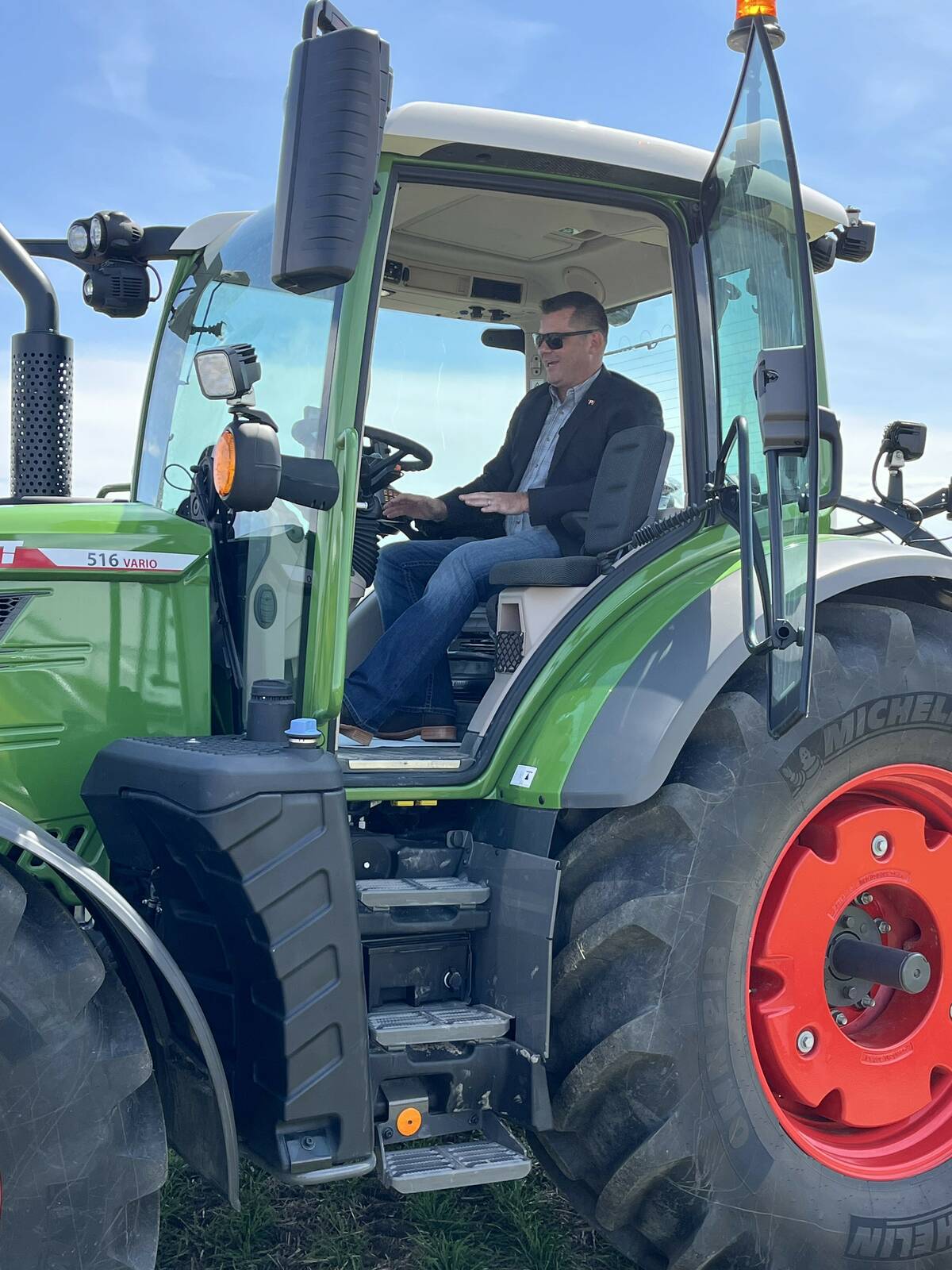
Farming Smarter receives financial boost from Alberta government for potato research
Farming Smarter near Lethbridge got a boost to its research equipment, thanks to the Alberta government’s increase in funding for research associations.
Given those ugly stats and the environmental consequences, scientists, investors and companies are turning their attention to bioplastic as a possible replacement for the petroleum-based product.
Bioplastic is made from renewable feedstocks such as corn, sugar cane and other agricultural crops, and some degrade in months or years rather than hundreds of years.
Last fall, Fortune Business Insights said the global market for bioplastic could reach US$20 billion by 2027 — growing at a rate of 17 percent annually.
Leaders in Canada’s ag sector are hoping that canola becomes one of the feedstocks for the emerging bioplastic industry. In early January, the Saskatchewan Agricultural Development Fund committed $360,000 to University of Saskatchewan scientists who are studying “plant-based climate-friendly alternatives to plastics.”
“We’re going to be constructing plastics from the extracts we get out of canola,” said Sarah Purdy, who’s part of the lipid quality and utilization team at the U of S.
Purdy will be working with Martin Reaney, who focuses his research on adding value to oilseed and grain crops.
“We produce enough (canola) protein in Canada to provide the protein needs for about 220 million people,” said Reaney, a plant science professor at the U of S.
“So, there’s a trend to do something with all that protein.”
The proteins in canola can be used to make plastic polymers — long and repeating chain of molecules. Polymers form the backbone of a plastic, Purdy said.
“Then there’s other sinapines and sugars (in canola) that can be used to make the plastic more elastic or flexible and you can change the properties … to broaden the applications.”
It’s possible to make many types of plastic from biological materials, but one of the weaknesses of bioplastic is water absorption.
Purdy hopes to resolve that problem by finding and using the right compounds within the canola seed.
Ultimately, the U of S researchers want to generate a final product or develop a novel technology for making bioplastic.
“Then we would be looking for a company … to license that (technology),” Reaney said.
Reaney and Purdy aren’t alone in their research on canola and bioplastics.
Danimer Scientific, a firm based in Georgia, is making bioplastic from canola oil.
The company’s core technology is a biopolymer called PHA (polyhydroxyalkanoate).
PHA is made from a fermentation process in which soil bacteria consumes canola oil. The end product is a bioplastic powder that’s combined with other biopolymers to produce biodegradable plastic resins, used to manufacture food packaging, drinking straws, cups, bottles, trash bags and bottles.
“Based on signed and pending contracts, the company is fully sold out of all production in its Kentucky facility and will use its increased capital base to significantly increase production in seeking to meet the expected current and long-term demand of its customer base,” Danimer said in a Dec. 29 news release.
The U of S scientists will be researching bioplastics made from canola and pulse crops, but there are also hybrid plastics made with biological materials and petroleum.
Such hybrid plastics could meet the definition of a bioplastic.
Further confusing the matter, some bioplastics are not degradable, and some petroleum-based plastics are biodegradable.
“When you see Coca-Cola advertising their plant based plastics, they could be using plant material in making plastic that will never bio-degrade,” Purdy said.
While the definition of bioplastic is hazy, there are benefits from hybrid plastics that use both petroleum and crops as a feedstock. The biological part increases the rate of decomposition, so a plastic bottle or yogurt container doesn’t remain in a landfill for 300 years.
“If you mix a highly bio-degradable material with a less degradable material, what happens … is it promotes the degradation of the low bio-degradable material,” Reaney said.
“There’s a big opportunity there in the hybrid plastics, to increase the (decomposition) of existing plastics.”