Farmers can increase storage capacity by moving to bigger grain bins, but those who do need to know more about bin management because bigger bins mean a greater risk of costly damage to the grain, says Joy Agnew, agricultural research services project manager at the Prairie Agricultural Machinery Institute.
“We’re getting a few hints and some basic information … that’s telling us that, yes, this might be a bigger issue than we thought,” said Agnew.
“If grain spoils during storage … it doesn’t even have to spoil to the point where you can’t sell it; even if you lose a grade because any kind of microbial activity, that can be a significant hit on the pocketbook.
Read Also
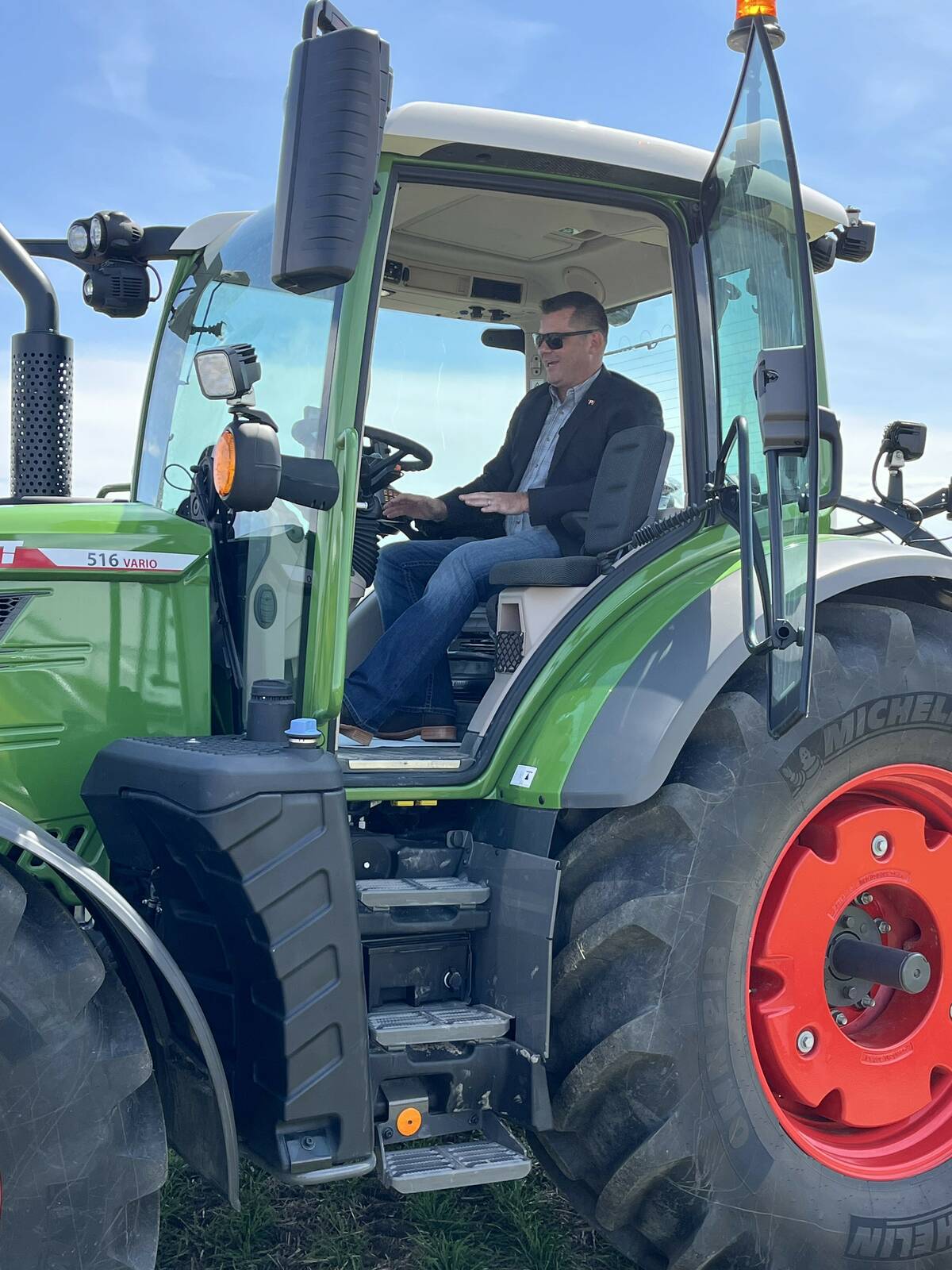
Farming Smarter receives financial boost from Alberta government for potato research
Farming Smarter near Lethbridge got a boost to its research equipment, thanks to the Alberta government’s increase in funding for research associations.
“The more grain in the bin, the higher the risk of that lost revenue. We’re talking about millions of dollars with these really big bins.”
Research tests and modeling suggest there are ways to mitigate risk when using big bins.
Bins as high as 35 feet introduce a different environment inside. The grain can be more densely packed because of the weight and the static pressure can be higher. Managing temperature and moisture, the two key elements of grain health in bins, can take more attention than in smaller bins.
For example, canola is considered dry at about nine or 10 percent moisture, but that requires a temperature of 15 C or lower.
To keep temperatures down, many producers use fans to condition the crop. That, Agnew’s research suggests, can be complicated, depending on the size of the bin, the size of the grain kernels, the depth of the grain, the air flow rate from blowers, and even the type of ducting used in the bin to carry air through the grain.
It’s also vital that everything be monitored, with sensors in the grain, to determine whether the material is being kept at the right temperature and moisture rates, Agnew said.
For the most part, air flow through big bins is either for aeration to manage the temperature or for natural air drying to remove moisture from the grain, which requires a higher air flow rate.
Grain drying is most effective at night, when the air is cool and the grain is warm. Air warms up when it passes over the warm grain, increasing the air’s capacity to absorb moisture, Agnew said.
“If you have cool air hitting warm grain you get the situation where you have great capacity to dry.”
Very wet grain needs a high air flow, but if the fan is left on for too long, the grain may start re-wetting as the cooler seeds draw moisture out of the warmer air.
Still, if drying is done during the day, the air is already warm, so it also has the ability to draw moisture out of the grain, just not at the level of cooler air at night.
However, higher air flow has drawbacks. Faster air moving through the grain builds more static pressure, pushing back against the air flow.
“There is pretty strong evidence, in my opinion, that air flow rate definitely matters,” Agnew said. “It’s going to affect your drying rate and it’s also going to affect, probably, your ability to quickly dry and possibly rewet.”
A fan pushing half a cubic foot per minute (c.f.m.) per bushel through 15 feet of grain will see about three inches of water resistance, known as static pressure, which reduces the ability of the air to penetrate the grain.
In big bins, that same air flow rate may face 30 feet of grain, generating 13 inches of static pressure.
“There aren’t a whole lot of reasonably sized commercially available fans for aeration that can handle that kind of pressure yet,” said Agnew.
As well, the type of ducting used to carry the air through the bin can add another half to two inches of resistance.
Kernel size must also be taken into account when considering grain management in big bins.
“You get more resistance because of smaller kernels,” said Agnew. For example, at 30 feet of grain depth at half a c.f.m. per bushel air flow through wheat, there might be 13 inches of static pressure pushing back against the air flow. But for canola, that static pressure might be 20 inches.
There is “more resistance because they’re smaller kernels; smaller kernels means smaller voids between the kernels and it’s through those voids that the air to pass.”
The size and types of fans also enters into the equation, said Agnew.
Stronger fans aren’t necessarily going to deliver the expected result. The faster the fan tries to push air through the grain, the greater resistance there will be to the airflow, she said.
The choice of fan type matters more with high static pressure. Axial, high-speed or low-speed centrifugal, or in-line centrifugal fans are all available for blowing grain.
A half c.f.m. per bushel air flow for 15 feet of wheat will generate three or four inches of static pressure. In that instance, “with a five horsepower fan, you’re going to get a decent air flow rate, no matter which fan you pick. At low static pressure, it really doesn’t matter what type of fan you pick.”
But, a five h.p. fan may not be able to handle anything more than six to eight inches of static pressure.
“When you get high static pressure, that’s when you have issues. …only the high-speed centrifugal is going to give you anything.”
Finding that balance for all these factors is the key.
“You have to understand the relationship between grain depth … and static pressure and how that relates to actual air flow from the fan that you have,” said Agnew.
PAMI tested air flow with peas, starting at about 19 percent moisture. High airflow rate hit the target moisture content of 15 percent in four days. A medium air flow rate took up to nine days, and a lower air flow rate set just for aeration, usually just to adjust temperature, never achieved the desired moisture content of the grain.
Still, the high air flow rate introduced a period of rewetting of the peas because they was cooling down.
The resistance to the air flow depends on grain type (size of kernels), depth of the grain and the air-flow rate itself.
Even a 10 h.p. fan can only handle a maximum of about 14 inches of static pressure.
Are two fans the answer? Tests in two 25,000-bushel bins using 10 h.p. fans showed mixed results. For four feet of canola, the air-flow rate from one fan measured 3.88 c.f.m. per bu. Two fans did not double the air flow rate, measuring 7.31 c.f.m. per bushel because the air flow from the fans start to work against each other. That trend continued as the depth of the grain increased, until at 21 feet, the air flow rate from a single fan was 0.5 c.f.m. per bu., while the rate from two fans was zero.
Interestingly, it was previously thought that the manner in which the grain is stacked in the bin makes a difference in the effectiveness of drying and temperature controlling procedures. But tests suggest that may not be the case. In bins with the same volume of grain, there was virtually no difference between bins that were heaped and bins that were leveled off with the same volume of grain.
“That was not expected to us,” Agnew said. Previous information indicated that “level vs. peaked vs. full had a huge impact on estimated relative trying time.”
Agnew also advised that farmers with big bins invest in new technologies, such as wireless sensors that distribute themselves in the bin. Some even have the ability to transmit information on movement of insects inside the bin, as well as carbon dioxide levels, temperature and humidity.