Company says upgrades made to its Regina plant represent its single biggest investment in Canada in the last 10 years
A two-year $14 million project to upgrade the Regina BASF production plant is complete.
The company recently announced that the crop protection production facility has been modernized throughout, including upgrading the mechanical and operation systems, the tank farm and formulation, lab and packaging areas.
The Regina location produces eight brands and has added Basagran and Viper ADV to the list. It will also produce Varisto for U.S. use only.
Next year, the company plans to add Solo ADV and possibly Facet L.
Jon Sweat, vice-president of business management for BASF Canada Agricultural Solutions, said the upgrades represent the company’s single biggest investment in Canada in the last 10 years. The facility can now produce more than 30 million litres of products a year.
Read Also
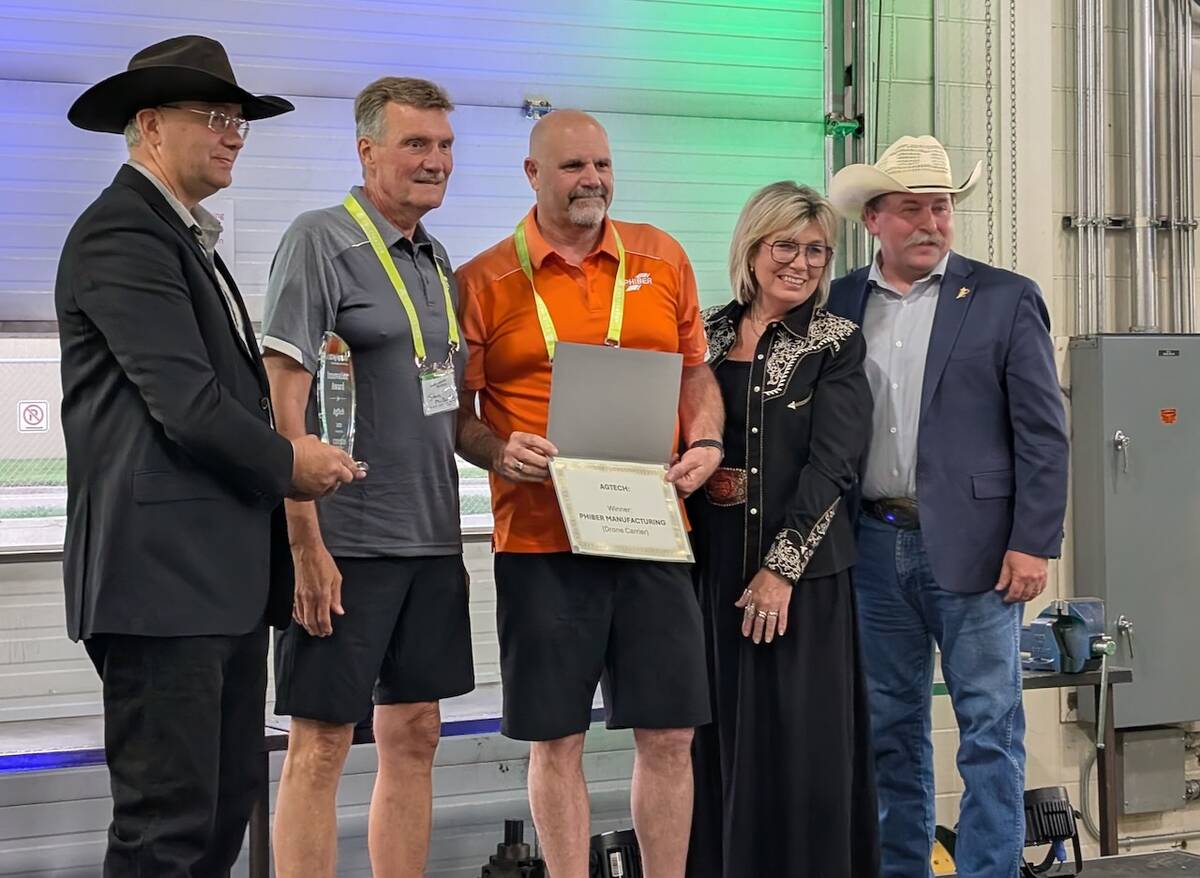
Ag in Motion innovation awards showcase top 2025 ag technology
The 2025 Ag in Motion Innovation Awards celebrated winners across five categories: agronomics, agtech, business solutions, environmental sustainability and equipment.
“That’s a volume that services roughly one-third of all of Canada’s acres just from this facility,” he said.
Although the plant has moved to greater automation, Sweat said there were no job losses. It employs 130 at peak production.
Regina site manager Kaleb Grittner said the facility has moved “from industry standard to cutting edge.”
The facility first opened in 1981 with a three-million-litre capacity.
Grittner said there have been numerous updates but none as extensive as this most recent project.
In the lab, renovations accommodate new machines for better quality control analysis, including a liquid chromatography mass spectrometer that allows staff to separate mixtures and analyze the different components. Grittner said the equipment can detect even trace amounts of leftover materials after rinse-out, meaning farmers can trust what they are getting.
The tank farm, which includes two outdoor and one indoor space, added a 300,000-litre stainless steel tank and now has 25 storage tanks to hold 2.8 million litres of raw material. Every container of raw material is sampled for quality assurance.
Grittner said the company is moving away from multi-use lines, tanks and systems.
“We now have more product specific equipment, which helps reduce the risk of cross contamination,” he said.
“Even prior to these enhancements this facility sported a blemish-free track record of cross contamination and now we have a new more robust system that not only allows us to make products we couldn’t make before but formulate them safer and to the highest quality specifications.”
Improvements were also made in the packaging area. Packing lines are segregated by product and more automation means better product flow and more efficiency.
Grittner said single jugs, for example, no longer need to be hand-managed and are filled by weight instead of volume for more accuracy.
Dan Packer, senior brand manager for herbicides, said it makes sense to move 100 percent of production of Viper ADV, which is used by pea growers, and Basagran products to Regina. Viper was used on 2.7 million of the 4.1 million acres of peas seeded in 2020, he said.
Solo ADV is used on more than 1.5 million acres of Clearfield lentils, making it the most-used product, he said.
Company officials also said BASF is committed to sustainability and is moving to provide Liberty 150 in refillable, reusable 864-litre totes from the Regina plant.
Brant Galbraith, brand manager for canola herbicides, said 14 million acres of Liberty Link canola are grown each year.
While single-use plastic containers are recycled through the company’s partnership with CleanFarms, these new totes will be re-used for five years as long as they continue to be safe and clean.
CleanFarms picked up about 5.5 million containers returned to retailers for recycling in 2019.
Sweat added that, worldwide, BASF will help farmers reduce the carbon emissions required to produce a tonne of yield by 30 percent by 2030.
BASF employs 300 to 400 people, depending on the season, at facilities in Regina and Saskatoon, and farms near Pike Lake, Vanscoy and Regina.