PolyAg Recycling in Bashaw estimates it will recycle 14,000 bags a year, mostly from Alta. and Sask., into resin pellets
BASHAW, Alta. — A new agricultural plastics recycling plant will give new life to old grain bags.
The PolyAg Recycling plant opened earlier this year, but because of COVID-19 has only begun recycling plastic grain bags into resin pellets full time. By the end of the month, the owners expect the plant to operate 24 hours a day, five days a week to keep up with the supply of used grain bags.
“It makes sense socially, environmentally and business sense, but it has to make sense financially,” said Dan Zembal, one of the owners of the facility.
Zembal estimates 14,000 grain bags a year, most from Alberta and Saskatchewan, will be recycled into high-quality, post-consumer resin pellets at their Bashaw facility.
“The system is designed to handle all the material being produced.”
Zembal, along with his partners Danian Flegel and Brad Wilson, all of Calgary, said the idea for the recycling plant took shape when the Alberta government launched a three-year pilot project to develop an agricultural plastics recycling system last year. Saskatchewan launched its mandatory program a year earlier.
“We saw an opportunity to get something going locally,” said Zembal.
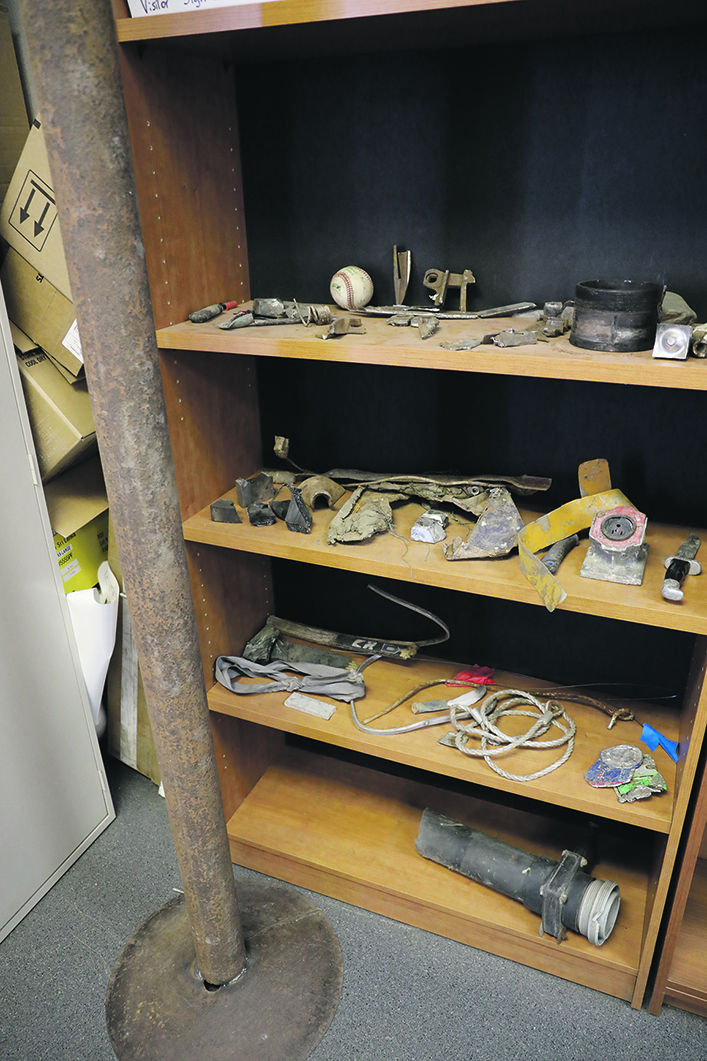
In the past, Cleanfarms sent 70 percent of the materials collected for recycling to end markets located in North America, the United Kingdom, India and Southeast Asia.
Last year as more markets for used plastic closed, Cleanfarms marketed all of the materials collected for recycling to customers in the United States and Canada.
Having a consistent supply of agricultural plastic was key to building the plant.
“It is all about quality and consistency of product,” said Zembal, who plans to set up a laboratory in the old oilfield services building to monitor the pellet quality.
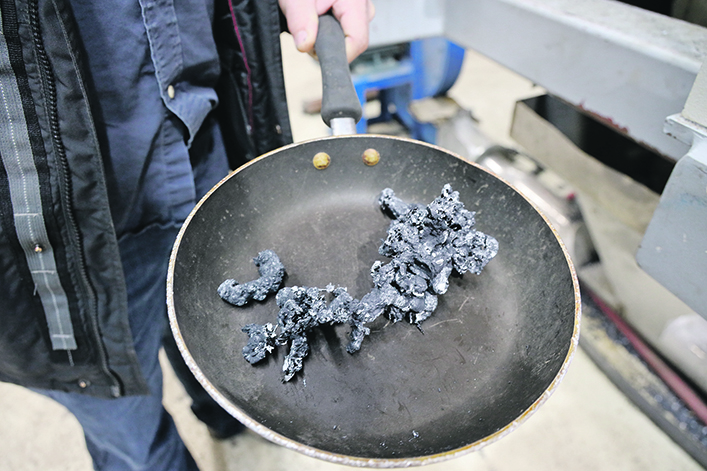
Zembal said they looked to China, the experts in recycling, when they designed their recycling facility. Because they were dealing with dirty grain bags and some silage covers, they were advised to include two washing stations in the plant to ensure a clean final product.
Working with Cleanfarms, the non-profit, industry-funded organization that helps Canadian farmers manage agricultural waste, grain bags are shipped from Alberta and Saskatchewan to the central Alberta recycling plant. PolyAg pays a modest fee to Cleanfarms to cover the cost of shipping to Bashaw.
Grain bags and twine represent half of all plastic generated on farms in Alberta. The other half is bale wrap, silage plastic, super sacks, greenhouse film and containers.
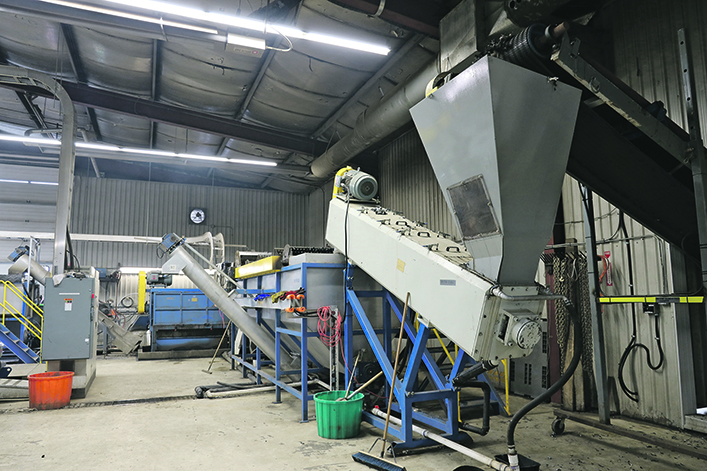
Farmers buy more than 30,000 grain bags each year. Cleanfarms estimates it collects about half the grain bags used in Saskatchewan’s mandatory agricultural plastic collection program at its 37 recycling locations.
Alberta’s program just finished its first year of a three-year pilot program and there are fewer recycling locations. Six new locations were added recently bringing the total collection sites in Alberta to 26.
In a 2019 Alberta grower survey, 32 percent of farmers reported that they return their bags for recycling. Twenty four percent said they took them to the landfill, 20 percent said the bags were stored on farm to deal with later and 14 percent said they burned the bags.
Barry Friesen, executive director of Cleanfarms, said with the addition of the PolyAg facility, farmers now have an option to “sustainably manage plastic on their farms.”
“We’ve had a crisis in plastic management for many years,” said Friesen, whose goal is to have all agricultural plastic recycled.
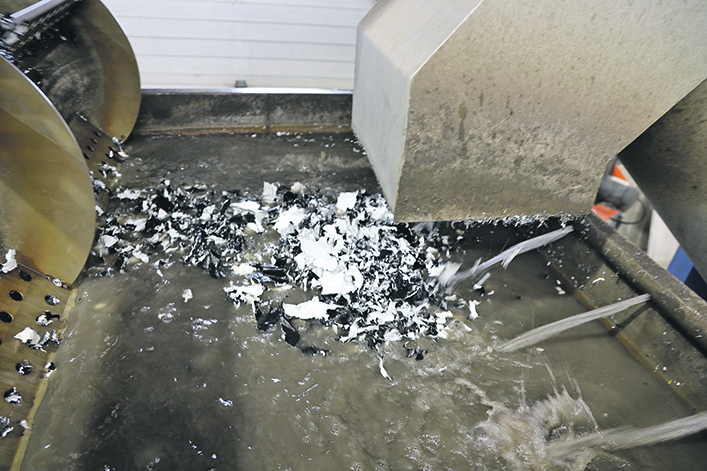
Once at the plant, the bags are shredded into small plastic pieces. A prescreener removes some of the small pieces of plastic and residual grain and other material. The plastic passes through two washing systems to remove any residual contaminants. Once clean, the flakes are dried and densified and passed through a double extruder system, which melts the plastic into long spaghetti-like strands. It is then cooled and cut into small pellets.
The pellets are sold to companies in Ontario, United States, or overseas.
PolyAg is also working with a Westlock, Alta., bag-manufacturing company to supply PolyAg’s resin pellets to be made back into plastic film.
When the PolyAg plant began working almost a year ago, it started with the 186,000 tonnes of stockpiled grain bags across Alberta with mixed success.
“Alberta had to get rid of the legacy stuff. Some of it was in pretty rough shape. It was nice to get past the legacy stuff,” said Zembal.
Mixed in with the legacy plastic was a collection of wood, metal and other debris. In the PolyAg office is a wall of honour lined with a collection of stuff found in the bags including hockey sticks, cutter blades, tires, knives, rocks and an eight-foot pipe welded to a disc used to wind the plastic.
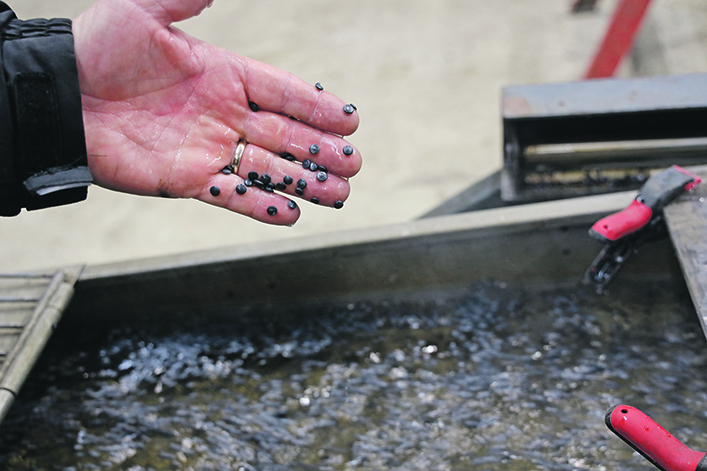
Zembal hopes education by Cleanfarms and municipalities will reduce the debris in the rolled grain bags.
While some silage plastic is hauled to the facility, the plant is designed to recycle only grain bags in an effort to maintain a quality final product.