Although yields were up, beet growers were critical of Lantic Sugar for failing to install ventilation
TABER, Alta. — Alberta sugar beet growers grew a record number of tonnes per acre last year, and ideal weather contributed to one of the shortest harvest seasons ever.
An average 28.51 tonnes per acre were harvested, and 17 to 19 percent sugar content was almost a record as well, said Alberta Sugar Beet Growers director Michel Camps,chair of the association’s agricultural committee.
He told the association’s Feb. 18 annual meeting in Taber that growing conditions favoured beets last year, with only a few acres damaged by hail and frost.
Read Also
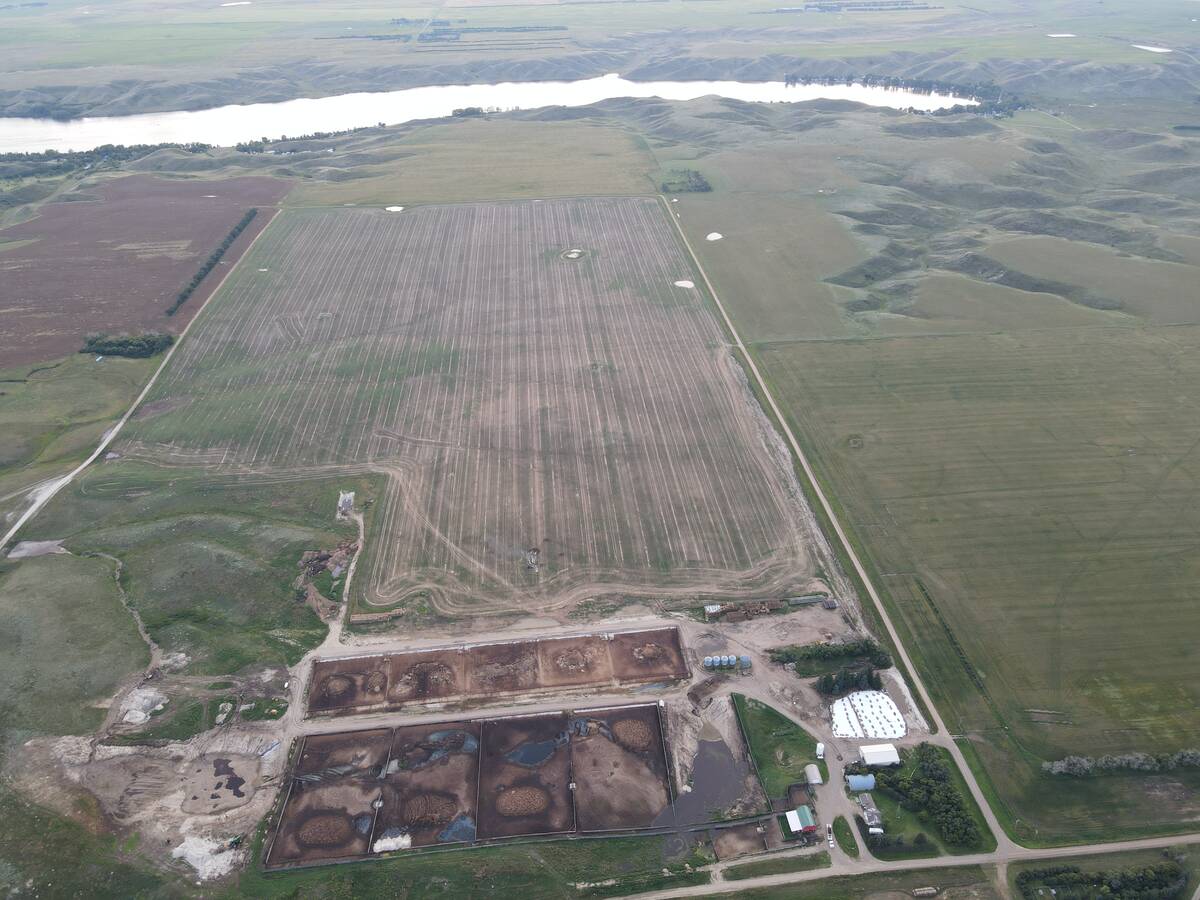
Saskatchewan RM declines feedlot application, cites bylaws
Already facing some community pushback, a proposed 2,000-head cattle feedlot south of Swift Current, Sask., has been rejected for a municipal permit, partly over zoning concerns about the minimum distance from a residence.
Digging ran from Oct. 1-24, and 638,099 tonnes were harvested from 22,364 acres.
“It was a great harvest,” said Gerald Third, the association’s executive director. “There was a great crop. It was brought off the fields in record time and stored.”
Director Gary Vucurevich, who reported on factory operations, said processing began Oct. 9 and ended in mid-February, at least one month longer than expected. By then, the beets had deteriorated while sitting in piles and producer returns on sugar had been reduced.
Vucurevich said the Lantic sugar factory was unable to maintain an average processing rate of 250 tonnes per hour because of boiler problems and other mechanical issues.
Lantic agricultural superintendent Andrew Llewelyn-Jones said in a Feb. 19 interview that equipment issues weren’t out of the ordinary this year.
He said there might have been “some slight reduction” in slice rate because of equipment.
“That’s just normal factory operation, which happens in every processing facility,” he said.
“You have equipment issues throughout campaigns, which we address promptly. But when you get a deteriorated beet, and it im-pacts the processing … that makes it even harder. So it’s a combination of factors.”
Vucurevich said the factory also decided not to use ventilation equipment in the beet piles because it didn’t think it would be worthwhile for what it thought would be a short campaign.
“With the benefit of hindsight, we now know that the decision not to ventilate was a poor one considering a processing campaign that extended well into the month of February,” said Vucurevich.
Third was less measured in his comments.
“It was a disaster, as far as we’re concerned. An absolute disaster,” he said.
“The factory never installed the ventilation because they determined that there was no value in it. There’s no value in it because of the way the growers’ contract is written. They don’t get paid until the sugar is processed. If you don’t get the sugar out of the beet, you don’t get paid.”
Growers are paid on the white granular sugar processed from the beets, rather than on byproducts such as molasses and pulp.
Llewelyn-Jones said ventilation equipment wasn’t installed this year because it wasn’t deemed useful in preventing beet deterioration.
“We have demonstrated over many years that there’s no benefit to ventilation because the beets store just as well without it,” he said.
“In a year like this, it might have helped, but for the growers, the benefit of ventilation would not have manifested itself because the deterioration was so significant.”
Llewelyn-Jones estimated that 1,000 tonnes of beets were lost in storage, which he said isn’t much against a total harvest of more than 638,000 tonnes.
He said growers would still have been paid on the basis of the contract’s extraction guarantee, whether or not ventilation was used in the stored beets.
The extraction guarantee is a formula devised that beet growers association president Rob Boras said covers growers for 82 percent factory efficiency.
“It falls short when we have a tremendous quality crop like we did this year, and we don’t realize the 90 percent plus benefit of it,” said Boras.
“It’s a backstop, but it seems like more often than not it becomes the top as opposed to the bottom.”
Boras said the guarantee would likely be discussed during contract negotiations.
Vucurevich said pile storage was variable at the dumping stations with those in Taber and Vauxhall particularly poor.
“Wide temperature swings resulted in considerable deterioration of these piles as the campaign stretched into January,” he said.
Hot spots identified through infrared photography were dug out and hauled for processing before other beets that appeared to be holding up better.
He said full factory processing statistics were not provided to growers, which made it hard to gauge the progress of processing.
“Factory staff indicated that they quit providing us with all of the information because we were posting it to the ASBG website,” he said.
“In light of the way that processing went, it seemed like a convenient excuse to hide declining numbers.”
Llewelyn-Jones said the information is readily shared with growers.
“We’ll show them exactly what our issues are and what the difficulties are, and we’ve done that on many occasions this past campaign. We’re quite open.”
But he said competitors can also access it when it is posted publicly, which becomes a business issue.