It took 2 1/2 years to build a recycling machine out of old oilfield pipe, an anhydrous ammonia tank, a straw chopper and parts of a swather
VERMILION, Alta. — It took farmer, inventor and recycler Danny Farkash about 2 1/2 years to figure out how to build a machine that turns used agricultural plastic into fence posts.
Using old oilfield pipe, an anhydrous ammonia tank, a straw chopper, parts of a swather and other bits and pieces, Farkash built a machine that sucks grain bags in one end and spits fence posts out the other.
“I design and build stuff and somebody had to do something about this plastic,” said Farkash, whose Noralta Farms yard is full of inventions, including a biorefinery to turn used vegetable oil into electricity.
Prairie farmers buy more than 30,000 grain bags each year to use as temporary storage for grain. With limited recycling options, many grain bags end up in landfills. Existing recyclers only want clean agriculture plastic, and agriculture plastic covered with debris is often burned or buried.
Farkash’s machine recycles all kinds of plastic, including dirty agriculture plastic. Farkash is in discussions with local municipalities to take the agriculture plastic sitting at landfills.
Key to creating inexpensive fence posts was finding an inexpensive heat source to heat the plastic to ultra-high temperatures. Luckily, Farkash had stacks of wooden pallets in his farm yard.
“What we’re doing is taking waste products to refine waste products. All these pallets go to the dump and they just run over them with a cat and bury them,” said Farkash, whose machine ticks both environmental and entrepreneurial boxes.
“It’s environmental, it cleans up the planet effectively without government subsidies and we can make a dollar.”
“I’m really big on recycling,” said Farkash, who added some people invest in Bitcoin, but his investments are in pipe.
Attached to his recycling machine is an old Cockshut 1850 tractor that doesn’t run well, but has good hydraulics. The hydraulics run the combine and swather combination intake, which gradually pulls the plastic into the machine where it is chopped into bits and the debris blown out the stack.
The plastic is then fed into a plastic extruder, which goes inside the super-heated burner, made from a recycled anhydrous ammonia tank.
The invention has not been without its drawbacks. Farkash said until they came up with the idea of a telescoping extruder, they had a “terrible time” getting the plastic through the machine.
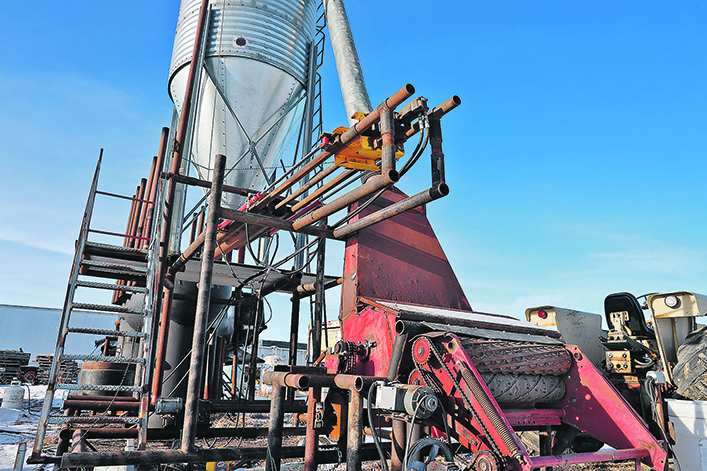
“When we came up with the idea of a telescoping extruder it was great. This cleans the entire machine up as it goes out, loads up again and injects it. We have very little maintenance, but high production,” he said.
Using hydraulic pressure, the heated plastic is injected into moulds, made from oilfield pipe. Once the mould is filled with plastic, it is spun and then set into a cooling water bath while the next mould is filled. When cooled, the plastic post shrinks one eighth of an inch and an air hose pushes the post out of the mould, where it’s caught in a cradle and stacked ready for sale.
When the plant is fully operating, Farkash estimated it will make two posts a minute. He already has orders for 3,000 fence posts.
Farkash was inspired to build his fence post machine to keep his employees busy during the summer. In the winter, they build heavy-duty livestock panels, also made from recycled oilfield pipe.
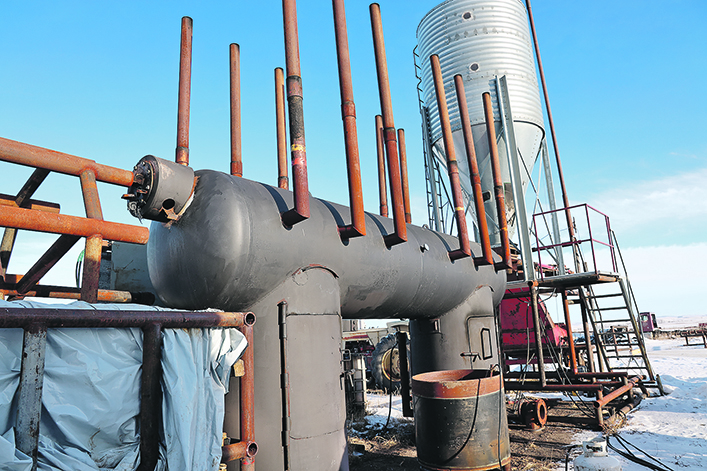
When the staff have caught up with the orders for livestock panels in March they will move to producing fence posts full time.
The posts, made entirely from plastic, don’t transmit electricity and don’t need insulators. Because they’re made from plastic that doesn’t deteriorate in the sun, the posts won’t deteriorate in the field.
“It means we can build a fence that will never need any maintenance and we can do it cheaper than a wood post. They’re almost unbreakable. You can pound a staple in and it stays in,” he said.
“These will last forever.”
The posts are four inches around and seven feet long, the most common size of fence post.
Read Also
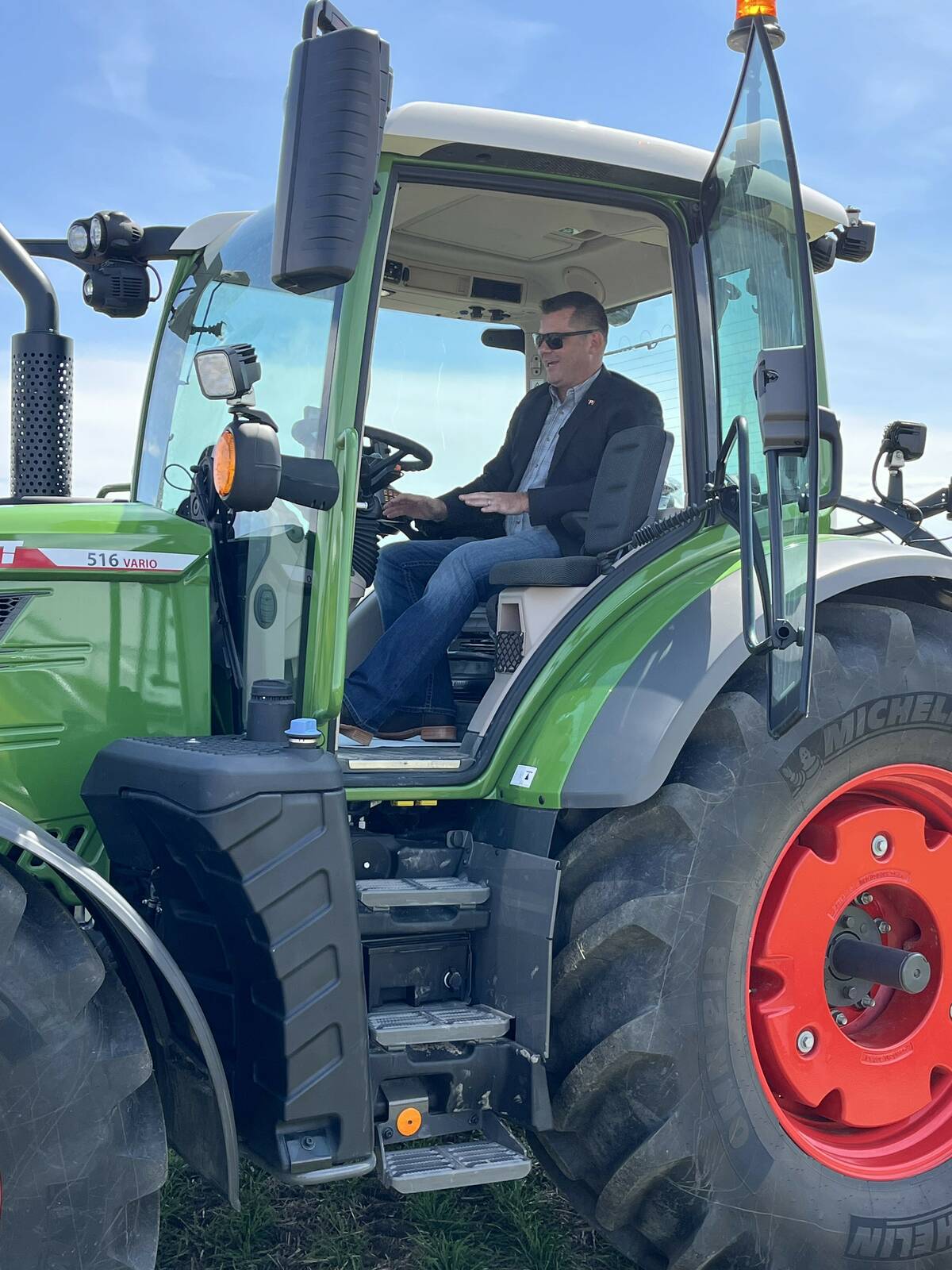
Farming Smarter receives financial boost from Alberta government for potato research
Farming Smarter near Lethbridge got a boost to its research equipment, thanks to the Alberta government’s increase in funding for research associations.
Farkash said now that the original design works, he will concentrate on making it more efficient.