ST. PAUL, Minn. – The new AgCommand telemetry tracking system monitors and records the precise location, work function and performance of combines, sprayers, seeding rigs and tender trucks.
The Agco system uses GPS technology to chart implement location and then uses cellphone technology to relay data from on-board sensors to the central unit.
AgCommand can track any factor that can be electronically monitored on a farm implement.
For example, a farmer with four combines working in four different fields can monitor the efficiency and performance of each combine from his office or pick-up truck.
Read Also
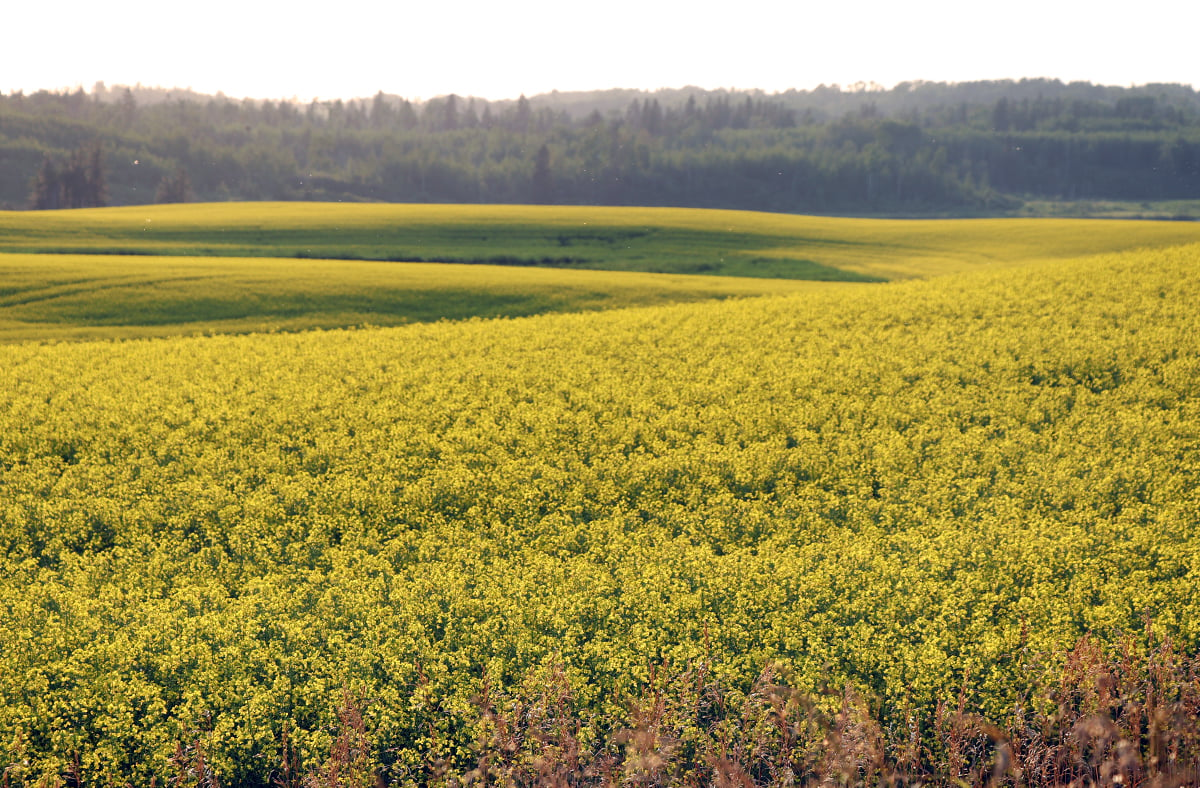
Agriculture ministers agree to AgriStability changes
federal government proposed several months ago to increase the compensation rate from 80 to 90 per cent and double the maximum payment from $3 million to $6 million
“If you have a $300,000 combine sitting idle waiting for the grain cart, you need to know about it so you can remedy the problem,” said Marlin Melander, Agco’s technology training specialist.
“That’s costing you money. The same applies to sprayers, seeding rigs and tender trucks. When the window is open, when it’s time for a machine to work, it has to really work, not sit idle. Every minute a machine is in transit or sitting idle is costing you money.”
Melander said commercial sprayer and fertilizer managers will likely be the first to adopt the system because it will make their tendering process more efficient.
The system can be installed on field implements and tender trucks to minimize waiting times for both.
Outfitting the entire fleet allows the dispatcher to stay ahead of the game by prioritizing which trucks should carry which product to which machine.
The built-in geo-fencing feature helps eliminate application errors by creating GPS boundaries. The system knows when a machine enters or leaves a specific work area and documents transit time between work areas.
It collects GPS location and performance data every 60 seconds. All information is sent to the user’s AgCommand website for instant retrieval.
Melander said knowing the exact location of equipment and which direction it’s headed helps the farm manager keep things rolling.
“If you’re short on grain carts and trucks, or more commonly, if they’re not being used efficiently, then you’ve got expensive combines just sitting.”
He said it’s not the combine operator’s fault if he sits in a field reading a magazine. Instead, it’s the farm manager’s fault.
AgCommand also allows farm managers to fine tune each combine as it’s working in the field. From his portable office, he can study what each combine is doing and help the operator make adjustments.
“You want every kernel of grain that goes into the header to end up in the hopper,” Melander said.
“Once you’ve spent the money to grow the crop, you don’t want any of it on the ground.”
The system transmits information on chaffer and sieve settings, cylinder speed and settings, fan speed and the grain loss monitor.
“If you have two identical combines working side by side and one puts more grain in the bin, then you know some adjustments need to be made,” he said.
“It’s also a good tool for training new operators. You can be somewhere else and still be in touch with a new operator, teaching him how to make the necessary adjustments for maximum yield.”
The in-cab module transfers from one implement to the next in 10 minutes, Melander said.
“The same module is used for combines, sprayers, seeders or any other implement.
“When you move it from your sprayer to your combine, the module reads the situation and automatically reprograms itself to your sprayer. It does the same thing when you move it from your combine to your seeding tractor. It’s about as simple as taking a CD out of your truck to play it in your car.”
Melander said the modules are pre-programmed in advance to recognize and work with specific pieces of equipment.
A service anticipator lets the operator know when service appointments are due. Dealers can also access it for long-distance problem diagnosis.
The problem can often be rectified through the cell network. If not, the service truck knows in advance what to bring to the field.
Deere introduces JDLink
John Deere also has a new telematics system.
Real-time information on location, use, performance and maintenance can be accessed on the JDLink website or sent by e-mail or text message.
The package provides real-time information about the machines in the field, allowing better decisions regarding equipment use, logistics and performance.
It also saves time in the field by coordinating labour and fleet management, sending alerts when fuel is needed, tracking hours of operation and monitoring engine load and idle times.
The telematics hardware comprises a communications modem/controller and wiring harness. It has cellular and GPS antennas.
The controller collects the machine data and wirelessly transfers it to the data server, where it is processed and made available on the JDLink website. Customers also have the option for alerts to be sent in real time via text message or e-mail.
An optional satellite communications module is available for data transfer in remote areas where cellular signals are not available.
JDLink Ultimate will be installed on all 8R Series Tractors for 2011, with one year of complimentary service.
JDLink Select is available for all makes and models.
Service Advisor Remote provides dealers with remote access to a vehicle’s diagnostic data to help minimize downtime.
If a problem develops with a vehicle in the field, service technicians at the dealership or anywhere with an internet connection can access diagnostic information.
In some cases, they can perform software updates remotely.
It also allows them to respond quickly with the correct tools and parts to fix the problem.
JDLink Select features:
- Roadmap/satellite map and driving directions
- Machine hours
- Geofencing
- Curfew alerts
- Maintenance management
- Machine use profile
- Enables Service Advisor Remote on approved platforms
JDLink Ultimate includes the JDLink Select features, plus:
- Machine status and comparison
- Advanced machine use
- Customer alerts
- Export/schedulede-mailreport
- Remote diagnostics via trouble codes