When Case decided its traditional trailing link suspension had disappeared over-the-hill, their question wasn’t “can we just fix it?” It was, “how do we design the best possible suspension?”
“Our mandate was clear. We were going to design the best sprayer suspension money could buy,” recalls Mark Burns, marketing manager for application equipment.
“There were many reasons to re-invent the suspension. Payloads were getting bigger. Speeds were increasing on the road and in the field. With zero till, fields were rougher. Operators were feeling the physical and mental pain of jostled around for longer hours.
Read Also
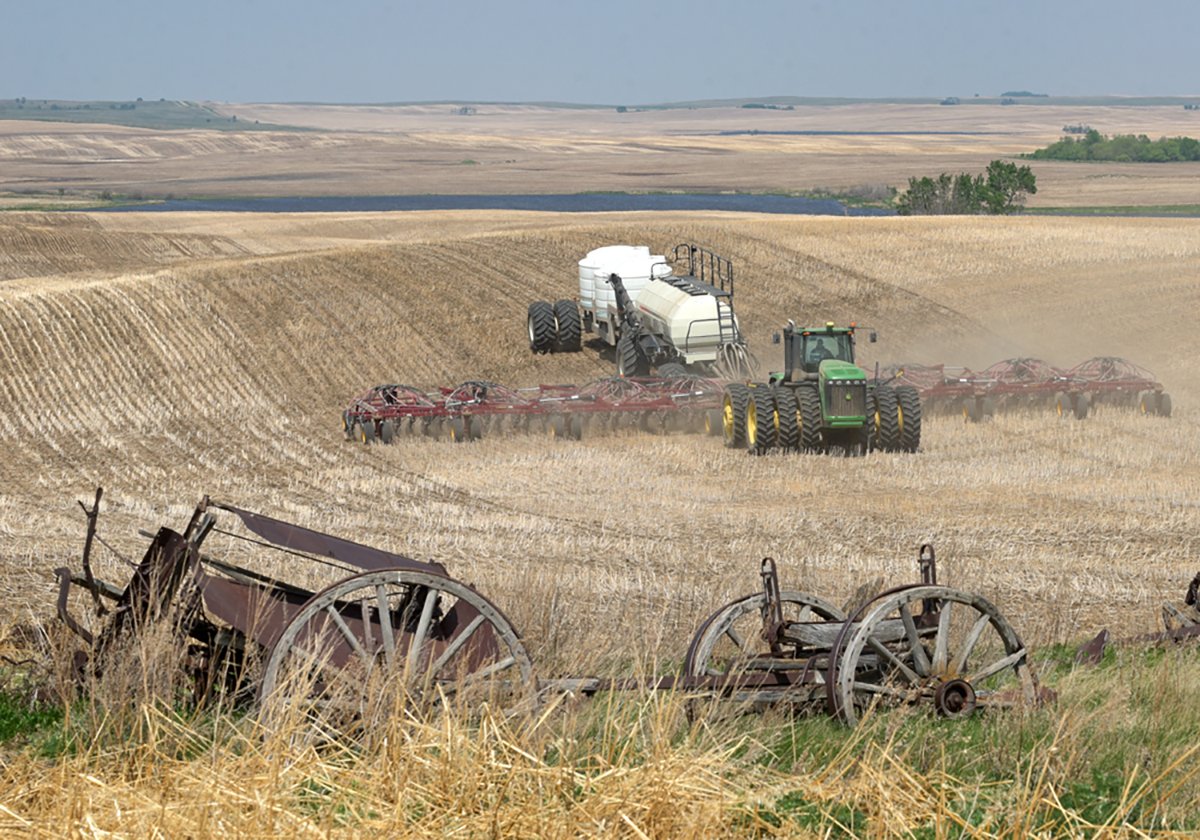
Who owns farm data?
Data privacy is one of the noted issues blocking adoption of digital agriculture on Canadian farms as farmers worry about where their data is going and how it’s being used by companies.
“At Case, our suspensions had been evolving, with stiffer springs and things like that. Some of our competitors had made bigger changes in their engineering, incorporating some of the technology from the larger sprayers into these smaller machines. We didn’t want to simply take our existing trailing link and try to improve it. We definitely wanted to start with a clean sheet.
“After trying every engineering concept we could think of, we ended up with this four bar linkage. Rather than having one single pivot point like we had with the trailing link suspension, we had four pivot points. This gives a wider range of motion, both vertically and horizontally. Each corner has an airbag for a smoother ride to dampen the shock loads, plus there’s a shock absorber.”
Burns says the new four-link design has more components than the previous suspension, and that naturally raises the manufacturing cost. He says they used to have a large upper cast component and a large lower cast component. Now they have a total of nine smaller ones. He suggests that the bean counters were not allowed to interfere.
“Make no mistake, this was a no-holds-barred project. We set out to be King of the Hill in ride quality and now we are. We were not looking for the most cost-effective design. We were looking for best operator comfort.
“In our seven pre-production models, we tested with farmers from the southern states northward into the Canadian Prairies following the season. Operators told us they were more productive because could run at a higher speed without the fatigue they normally experienced.”