Spreading fertilizer on the surface of fields was a standard practice in Western Canada before it became popular to deep band and seed row place fertilizer. However, there has recently been a move back to spreading fertilizer as growers try to lessen the workload during seeding and reduce their early season financial exposure to inadequate rainfall.
Deep banding continues to be the gold standard when it comes to reducing losses of nitrogen into the environment. However, the yield gains from seeding crops earlier can more than justify the losses and the extra pass needed to top-dress fertilizer pre- or post-seeding, say some.
Read Also
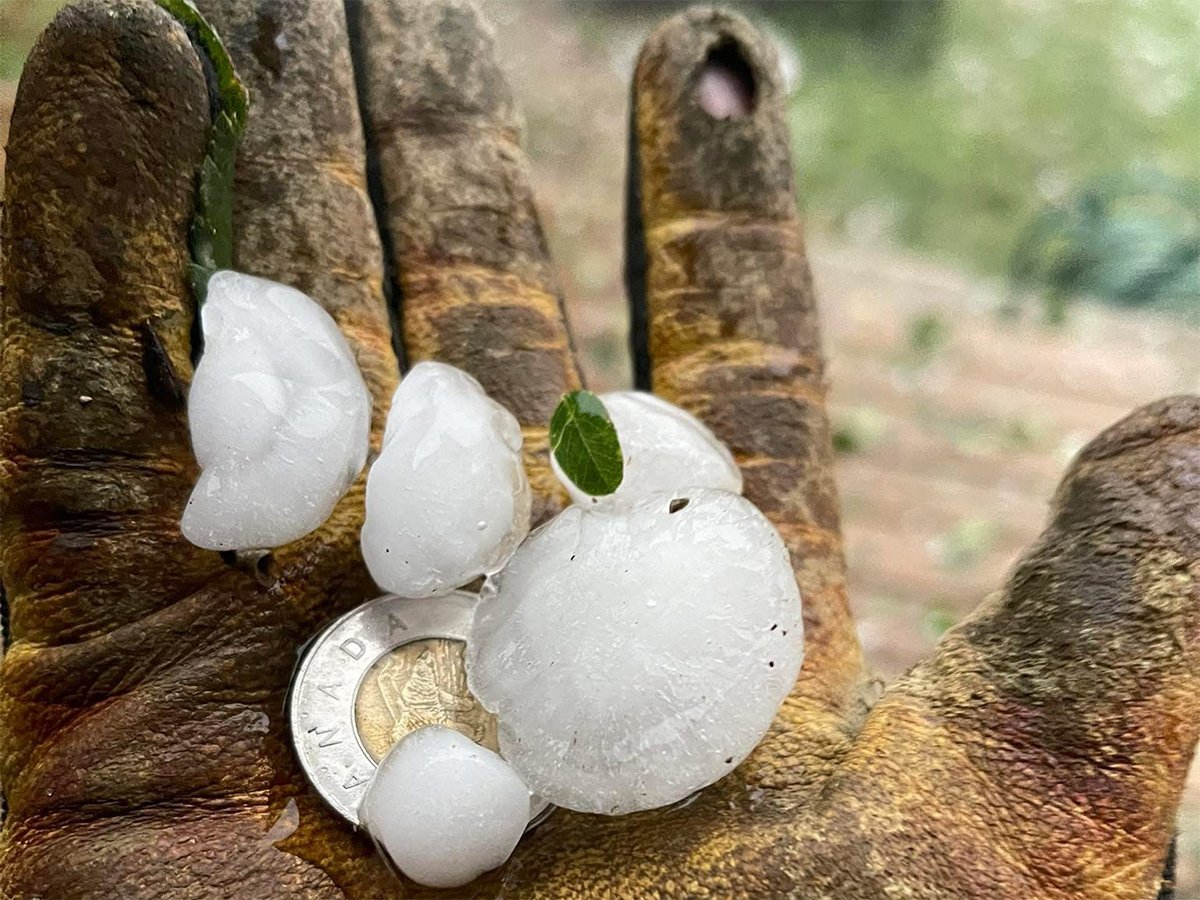
Half million acres of Alberta crops affected by massive hail storm
Late August hail storm catches farmers in prime harvest mode, damaging half million acres of crops in Alberta.
Equipment manufacturers are responding to the shift. Salford and SeedMaster displayed new products at Canada’s Farm Progress Show that were designed for surface applications. Meanwhile, some growers are avoiding the significant financial costs of buying a separate machine or implement for topdressing by building their own implements to attach to their air carts.
Australian producer Michael Pfitzner needed a fertilizer spreader on his 7,000-acre dry land farm, but he struggled to find a product that exactly met the needs of his controlled traffic cropping system.
Producers who practise controlled traffic farming have to be careful not to introduce variability into their fields.
For instance, if their fertilizer spreader has a tendency to lay fertilizer thicker in the middle of its range and thinner at the end of its range, this introduced variability will worsen in the field every time the spreader is used.
“We can actually introduce quite a lot of variability in paddocks,” Pfitzner said.
His controlled traffic system is based on 12-metre sections, with three-metre centres where all wheel and track traffic is confined.
The most economical way Pfitzner found to meet his fertilizer spreading needs for wheat, barley and canola was to build a spreader bar that connects to his Flexi-Coil air cart.
“The issue with a lot of spreaders is spreading product accurately and evenly,” he said.
“They could probably do it easy enough on 24 metres, and I know quite a few of them claim to be able to do it on 36 metres, but in windy conditions or conditions that are not so favourable for spreading that width, it’s going to create some variability with the application.”
Pfitzner took his design to a local fabrication shop, where the boom was built.
The shop combined a three-point hitch boom and an A-frame and extended the hitch on the air cart to facilitate easier turning at the end of runs.
@mottagwa @HolmanFarms pic.twitter.com/lNsw6rTuL1
— Michael Pfitzner (@farmingfitz) June 2, 2016
@ZwarFarms pic.twitter.com/KfcfVGaNRE
— Michael Pfitzner (@farmingfitz) June 2, 2016
The spreader bar was adapted to attach to the hose outlets on the air cart in the same way that the seeder connects, and the drop tubes were installed on the boom at double the row spacing on the drill.
The seeding rows on the drill are 272 millimetres, while the drop tubes on the boom are on 544 mm centres.
There are no splatter plates on the tube openings, but Pfitzner said the boom is able to provide a uniform fertilizer application.
“The benefit of the system is that it’s going to be more accurate than what the other spreaders are, and we can use multiple products,” he said.
“So we can do a sulfur based product as well as a nitrogen based product and vary those rates independently, according to what the paddock needs.”
SeedMaster’s application bar a time saver
Salford’s high-capacity boom spreader takes field advantage in windy conditions
Salford sprayer offers variable rates, hydraulic power
Building the spreader boom to integrate into his existing production system resulted in considerable savings, and Pfitzner didn’t have to worry about incorporating a new controller on his farm.
“To do the same job as this, given that the air cart is 9,000 litres, to get a single capacity spreader, it would have cost more, especially to do variable rate,” he said.
“It would be another controller, and you would have to put the information in to control it. Everything has to be compatible with what you’ve already got.”
It cost about AUS$30,000 to build the boom and get it field ready, but Pfitzner said it would have been much easier and cheaper if he had a pull-between air cart.
“If we did have a tow-between air cart, then we could use a ground glider boom and the cost would be quite a bit cheaper to build it that way,” he said.
Pfitzner said other spreaders are able to travel faster than his fertilizer boom because the rollers in his air cart are spinning twice as fast as they normally would because twice the product is being is metered out.
“We are probably travelling at 14 km-h at high rates with high rates of urea at 160 kilograms per hectare (142 lb. per acre). At what we call standard rates, 60 to 80 kg per hectare (53 to 70 lb. per acre), we travel at 20 to 26 km-h,” Pfitzner said.
“The speed is has to be matched to the rate that is going out. When you’re doing variable rate maps, it’s a little more difficult because you have to match the speed to what rates are going on at a given time.”
Contact robin.booker@producer.com