A pair of driven rubber tracks that can fit both the air cart and the combine can save a crop both in the spring and autumn.
That’s the conclusion of Grand Prairie, Alta., farmer Devin Linden after running the same set of Griptracs on his Case 8010 combine, a 425-bushel Morris air cart and an 800-bushel Seed Hawk air cart.
“We paid about $50,000 for the tracks five years ago and we’ve really gotten our money’s worth,” said Linden, who farms 4,000 acres with his father, Carl.
Read Also
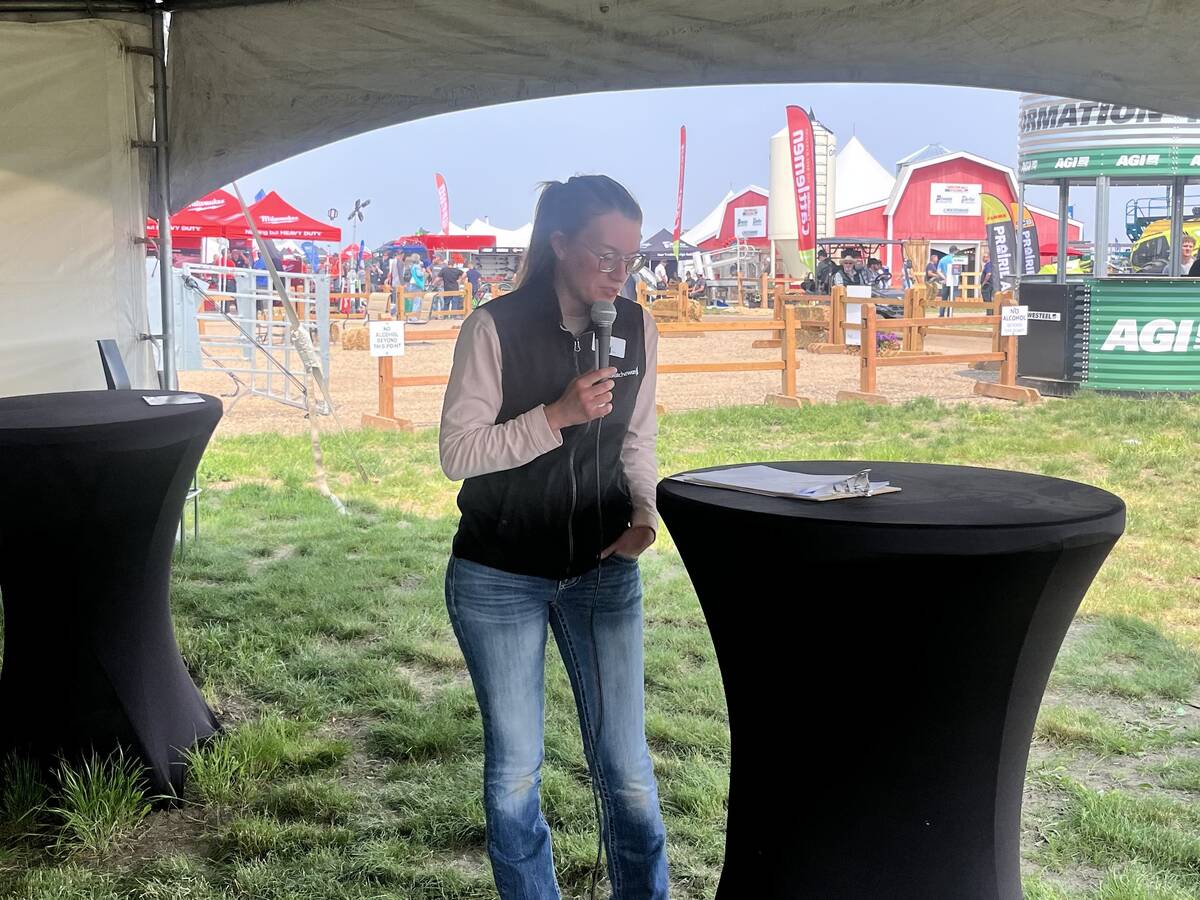
Ag in Motion speaker highlights need for biosecurity on cattle operations
Ag in Motion highlights need for biosecurity on cattle farms. Government of Saskatchewan provides checklist on what you can do to make your cattle operation more biosecure.
“We bought them when it was muddy, with the idea of just putting them on the combine,” said Devin.
“They were awesome. We couldn’t have gotten the crop off without them so they paid for themselves the first year.”
A wet spring seeding season is the likely scenario following a wet harvest. Rather than drag their Morris cart through the mud, they bolted on the Griptracs.
The universal 10 bolt pattern along with four-inch spacers to move the tracks away from the cart made it relatively easy to put on the tracks. They used the original Morris hubs and bearings, which turned out to be a mistake, according to Devin.
“The tracks themselves worked very well in the wet. But one fell off because the original air cart bearings seized,” he said.
“When you make your turns in the headlands, tracks have way more surface and way more side force than tires. It really loads up the hubs and bearings.
“The other thing is tracks have a bigger circumference, so those bearings are now turning at a higher r.p.m. than they were designed for.”
Into their third year with the Griptracs, the Peace region flip-flopped from the typically wet environment to bone dry conditions.
However, Carl and Devin decided the tracks were doing a good job of reducing compaction, so they reworked the bearings and ran the tracks one more year under the Morris. This time there were no problems.
When it came time to trade the Morris up to an 800-bushel Seed Hawk, they removed the Griptracs and parked them in the yard.
They immediately switched the new Seed Hawk from the original bias ply tires to radials. Devin said he and Carl tried to order tracks, or at least dual radials, but they weren’t available.
“Seed Hawk said they wouldn’t sell us radials. Their cart wasn’t designed for radials or tracks.
“And their bias ply tires were supposed to run at something like 50 pounds, so of course they’d cause compaction. That’s way too hard for any soil.
“So we installed those big Michelin radials and we ran them down at 12 pounds. They didn’t pose any problem.”
He said the radials were not only softer but also wider by two inches per tire. Compaction was probably less severe than with bias ply tires, but it still wasn’t good enough for the Lindens.
“We still had a hell of a time with compacted tire tracks. And that was a dry, dry spring,” said Devin.
“We had these hard dual strips all over the fields wherever we pulled the cart. Canola plants absolutely could not break through.
“We tried filling the cart only halfway to reduce the weight. But what’s the point of investing in an 800-bushel air cart if you can only carry 400 bushels?”
He said it’s frustrating to put down the full load of seed and fertilizer on whole fields, only to have acres lie barren due to compaction.
Carl calculated the cost of lost canola due to air cart tire strips to be about $45,000 per year. The lost annual revenue was almost equal to the price of the Griptrack pair they had sitting in the yard.
“The economics of installing rubber tracks should be simple for the manufacturers to understand, but you can’t tell these people anything,” said Carl.
“The big Michelins are roughly 700 square inches per tire. There’s four tires, so there 2,800 sq. inches in total. The number is smaller for bias ply tires.
“On the Griptracs, we have 3,400 sq. inches on each track, so there’s a total of 6,800 sq. inches.”
But Seed Hawk and other drill manufacturers showed no interest in rubber tracks, so Carl and Devin turned to the Griptracs sitting in the yard. After two seasons of running the cart on radials, they traded for a new 800-bushel Seed Hawk, and ordered it without tires so they could install their Griptracs right off the bat.
The Seed Hawk is about twice the weight of the Morris, so they knew that using the original bearings and hubs was out of the question.
The Griptrac people reported good luck using the final drive units from big combines to interface between a heavy cart and the track systems. The combine drives were strong enough and they might serve to space the tracks enough from the cart.
But there would be problems with the speed differential caused by the tracks, powering the ground drive metering system, the exact offset of the tracks and other unforeseen glitches.
The question was “how do we do it?”
That’s where Craig Swanson at Gateway Farm Equipment entered the picture. Swanson, service manager at the Case dealership, was up for a challenge.
“There was a lot of math and calculations, plus a lot of welding and machining involved,” said Swanson, adding that the combine drives had the necessary bolt pattern to match up with the Griptrac drive wheels.
The Griptrac drive wheel lacks enough recess to allow for a bearing cap. Seed Hawk has a seven or eight inch distance between the wheel-mounting surface to the end of the bearing cap.
“You’d need a seven or eight inch spacer, and that’s way too much distance for a spacer,” said Devin.
“On the Morris setup, they had four inch spacers. I think even four inches is too much distance with tracks. There’s too much leverage.
“Using a combine final drive eliminates the spacers completely and solves the leverage issue.”
New air carts can be ordered with hydraulic meter drives. Swanson said that eliminates many of the intricacies of putting aftermarket tracks on an air cart.
But Linden’s new Seed Hawk cart had the ground drive.
Swanson said aftermarket rubber tracks create rotational problems when installed on air carts.
The factory setup with chains, sprockets and turning tires was designed to work in one rotational direction. Sticking a combine final drive in the mix makes everything run backward.
The other issue is shaft speeds. The effective rolling circumference of the track and drive system is less than that of the original tire and sprocket combination. As a result, shaft revolution speed is twice that of the original factory setup.
There are no planetaries or other mechanical gear reduction systems in the Griptrac setup. The drive wheel that powers the track is so much smaller in diameter than the old drive tire that it creates an automatic increase in speed. Griptracs on a ground drive metering system create a high-speed shaft driving the metering rollers.
“So we installed that small gearbox…. It reverses the direction of rotation. And it has a two to one gear reduction that puts us within seven percent of the original Seed Hawk numbers.
“After we had it all together, we did a ground speed calibration run and the number on the monitor changed by only one digit. It’s so close that the monitor can handle the variance.”
Devin said the tracks worked beautifully in 2010 with no compaction issues.
While they are satisfied the Seed Hawk on Griptracs is the way to go, Devin said the downside is having to deal with the extra wheels, tires and hubs if you don’t plan and order exactly what you need.
An added benefit is that the Griptracs are not tied to one implement. The Lindens can install them where they’re needed most.
“When we get back into wet harvests again, it’s a simple matter of 10 bolts to put each track back onto the combine. They mount to the combine the same way they mount to the air cart.”
Griptrac said that although the
Seed Hawk boss Pat Beaujot says rubber tracks are on the agenda at his company, but they need more work to meet farmer demands.
“We know a cart will float better on tracks and it’s less likely to get stuck, but there are issues we need to address before we offer tracks,” he said.
“We have a tentative plan for a track setup. One of our customers has put tracks on two of our 800 carts.”
He said Kent Hamner of Govan, Sask., bolts Soucy tracks directly to Seed Hawk hubs.
Beaujot said Hamner imported the tracks this winter. Seed Hawk considered offering the Soucy tracks as a factory option, but said there’s an inherent problem with tracks on any big air cart.
“The fill auger cannot manoeuvre around the tracks for full access. It just will not happen.
“There’s no way you can get an auger to do everything it’s capable of with tracks in the way, on any cart, any manufacturer.
“Fill augers are a big deal with farmers. It seems we spend more time improving our augers each year than we spend on the drill. Farmers are very touchy about messing with their fill augers.”
Beaujot said if a customer wants to buy a complete drill minus the cart tires, that’s fine with him. The customer can then to buy the tracks.
“But if we sell it with tracks of any brand and the customer doesn’t like the fill auger obstruction, then he’s mad at us.
“So for now, this is the way we’re doing it until we re-think the whole engineering aspect.”
Beaujot said hydraulic metering has eliminated the ground drive problem associated with tracks and more producers are opting for this option.
For more information, contact Pat Beaujot at 306-538-2221 or www.seedhawk.com and for Griptrac, www.griptrac.com, 231-853-2284