The AgriWave remote machinery management system, which is integrated into a machine’s on-board control system, can give farm managers better insight into their drivers, help with personnel training and boost efficiency.
Introduced last year by GVM Ag- Junction, the system is standard equipment on all Predator E350 applicators and will soon be available as a retro fit for other brands, according to AgJunction’s Aaron Hunt.
“Our electronic work order system is integrated with the on-board controller. So we can push prescription files back and forth quickly and without any problems,” said Hunt.
Read Also
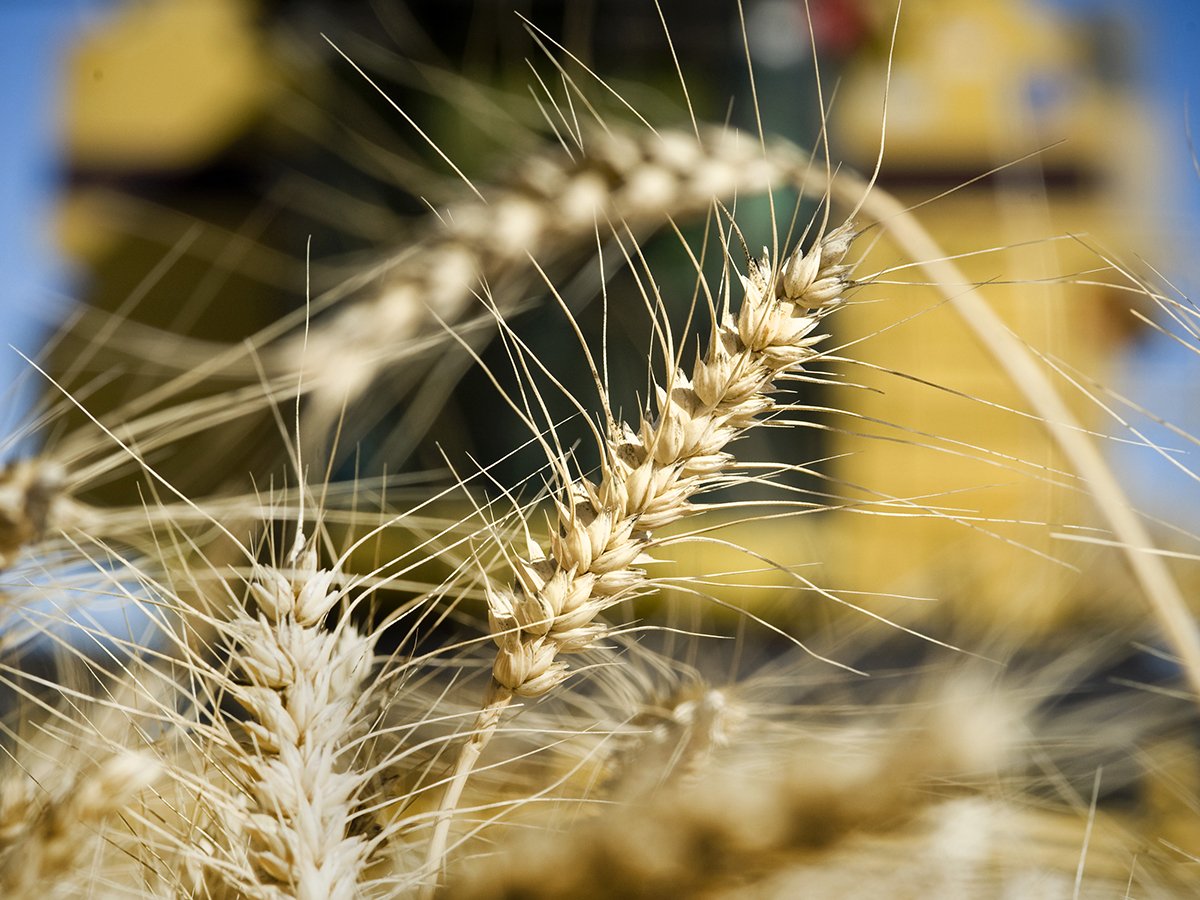
European wheat production makes big recovery
EU crop prospects are vastly improved, which could mean fewer canola and durum imports from Canada.
“The GPS reports live once every minute. It’s not like the batch systems that store data and then send a batch of data all at once.
“This isn’t what you’d call near-real time. It’s live. The monitoring system for Tier III feeds data to the server twice a second.”
Hunt said that a farm manager can monitor the tach, fluid temperature and pressure or virtually anything else that connects to a wire.
“If you’re in your office or pickup, you can go on-line to watch the exact same dashboard screen the operator sees.”
Hunt said following the action in the cab can be a big help in training and upgrading machine operators.
“You’re not just monitoring a machine. You’re monitoring the operators. You can see what your best veteran drivers are doing right and what your rookies are doing wrong.”
That’s not to cull low-performing drivers. With farm help hard to find, better training for new drivers is the best solution.
“Paying attention to what the machine is doing helps you upgrade the driver’s skill.
“Are they running the r.p.m. too high? Turning too fast in the headlands? Do they let the machine sit and idle for 15 minutes at the end of the day so it cools down?
“There are dozens of things you can learn about your driver’s habits by monitoring the machine.”
Hunt said telematic troubleshooting can reduce downtime. If a fault code comes up, the farm manager is notified at the same time the operator sees it. If the dealer or maintenance crew is tied into the network, they can start work on the problem immediately.
“And here’s the main thing. The farm manager or the dealer service department can actually interact with the machine through this system,” said Hunt. “So if it’s something that can be solved remotely, you can conceivably get the machine up and running almost immediately.”
Hunt said the basic AgJunction system can expand and has immense capacity.
“You might have a dispatcher monitoring 50 machines over a three state area. We can handle that. If you’ve got 12 volts available on a machine, we can monitor it.”
For more information, contact Aaron Hunt at aaron. hunt@agjunction.com.