Used poly grain bags are heavy and awkward. It’s a hassle hauling them to designated dump sites and more municipalities pass laws each year to ban bag burning.
American farmers have numerous recycling options, turning used grain bags into irrigation pipe and other industrial or consumer items.
The recycling programs are backed by environmental rules regarding the disposal of grain bags.
Until this summer, there have been no options for the 15,000 grain bags emptied each year on the Canadian Prairies.
Read Also
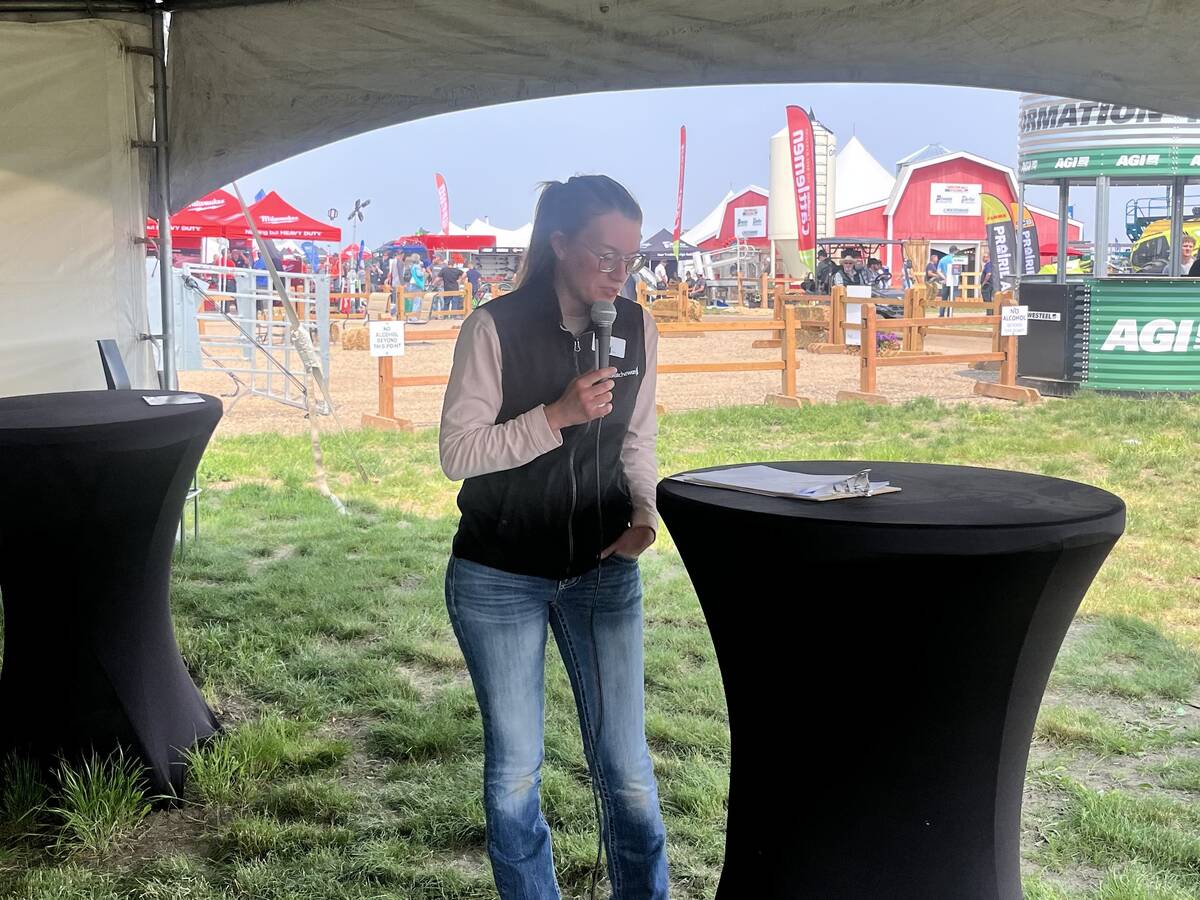
Ag in Motion speaker highlights need for biosecurity on cattle operations
Ag in Motion highlights need for biosecurity on cattle farms. Government of Saskatchewan provides checklist on what you can do to make your cattle operation more biosecure.
But an Alberta company called the Plastic Place wants those bags to flow into their poly recycling plant in Bassano, about 150 kilometres east of Calgary.
The Plastic Place began using recycled post-industrial plastics five years ago and is now installing German and Italian equipment engineered to recycle grain bags, said company president Bevan May.
“Grain bags are a new initiative for us. By this fall, we’ll be capable of taking every pound of plastic grain bag used on the Prairies,” said May.
“The challenge is to work out an economically feasible way to collect used bags from all corners of the three provinces and transport them to the new facility. That’s what we’re concentrating on right now.”
The Plastic Place is the first company in Canada to set up a large scale, commercial facility for recycling grain bags.
The key is finding the right equipment to wash flexible plastic, also known as film.
“The equipment is being installed as we speak and it will be fully operational this summer. We are the only facility in Western Canada with the capability to wash film and the largest such facility in all of Canada.
“Everyone involved is quite enthused about getting this problem solved, including the farmers we’ve talked to. Everything is coming together very rapidly.”
May said many Alberta municipalities have designated collection and transfer stations for grain bags. Regular municipal dumps and dump sites established for chemical containers may not be large enough to handle the bulky piles of bags and the equipment required to densify and load them.
Business opportunity
May said the collection, densification and transport of used grain bags presents an excellent business opportunity for entrepreneurs looking for a secure business venture.
He said his company wants to focus on processing and manufacturing plastic goods. They do not want to be in the business of collecting the raw materials.
“It’s definitely not our intent to remain in the collection side of things. Our interest is to get the used grain bags into our processing plant. So I think there’s a good business opportunity here for someone.”
The money to collect, densify and transport used grain bags potentially comes from three sources. Some municipalities in Alberta and Saskatchewan have already put money in their budgets for grain bag disposal. However, that’s only a short term-solution, said May.
“Taxpayers can’t be expected to bear the cost of bag removal. Our objective is to help work out a user pay mechanism along the lines of the tire program.
“When a producer buys a grain bag, there’s a recycling fee that will later be applied to the removal and recycling of that bag.”
May said until a user pay system is in place, the third source of revenue for collectors comes from the farmer himself.
“The producers we’ve been dealing with say they are willing to pay someone to come onto their farm and remove used grain bags.
He said the Plastics Place operates its own trucking company and may have to look after shipping from regional collectors to the Bassano plant.
May said his company realizes it’s nearly impossible to organize back haul flatbed trips into Alberta. Typically, any flatbed coming from Manitoba or Saskatchewan will be hauling hay to Alberta.
Polylog
The densified bags resemble logs, and are loaded on a flatbed the same way eight foot logs would be loaded in the forestry industry. As the load builds to 40,000 pounds, the bottom layers compress, making the load more stable.
The prototype bag densifier developed by the Plastics Place winds a 250 foot grain bag into a tight eight-foot-long polylog weighing about 500 lb. and measuring two feet in diameter.
It takes two minutes to wind up each log. Smaller bags weigh as little as 300 lb. and the largest bags weigh 700 lb.
“Our equipment grabs an individual bag out of the pile. It doesn’t matter how they’re piled on the ground. Two minutes later, it’s a log. That makes it perfect for moving from farm to farm.”
The hydraulically driven bag winder attaches to the front of a skid steer loader. The prototype is in the final stages of field testing on Alberta farms.
Big round poly bale
The other method of densifying bags is to feed them into a big round baler.
“Some of the Alberta farmers we’ve been working with have fed from four to six bags into a single bale. That makes a good tight bale that weighs between 2,000 and 3,000 lb.
“From what we’ve learned, they’ve been able to do this without any sort of modification to the baling machine. So if you’re set up to handle big round bales, this looks like a logical way to handle used grain bags.”
May said his company is focused on only grain bags and not forage bags. As they are used, forage bags are cut into small pieces that don’t work well in the recycling process. However, if a forage bag is still in one piece, they will accept it.
For more information, contact Bevan May at 866-240-2122 or visit www.tppinc.ca.
– LYSENG
The Unloader requires 50 h.p. and a hydraulic capacity of six gallons per minute. Power take-off speed is 540 r.p.m. All hydraulic controls are at ground level in one location.
Nelson said there are three components in the overall Loftness system. The GBL Grain Bag Loader sells for $26,800. The GBU Grain Bag Unloader sells for $34,000. The truck auger for transferring grain from a semi into the loader hopper sells for $13,5000. Those prices come from Young’s Equipment in Regina.
Although the system was intended for the corn growing states, Nelson said small-grain producers in Canada have caught on to the advantages. The first Loftness bagging systems were built in 2008 and there are 60 baggers and 100 unloaders at work in the three prairie provinces.
The Grain Bag Loader fills at a rate of 26,000 bu. per hour, loading 10 foot diameter bags up to 300 feet long with a capacity over 12,000 bu. Nelson said most other loaders handle only 200 or 250 foot bags.
The 17 inch main auger on the GBL has a two-inch shaft and the hopper is eight feet by eight feet. It requires at least 50 h.p. The p.t.o. is 540 r.p.m. There’s an electric winch for bag loading, a hand winch for bag tray adjustment and a hand wheel to apply the automotive style disc brakes.
The truck auger has a hydraulic requirement of 21 gpm at 2,900 psi to power the pair of seven inch hopper augers and the 12 inch main auger.
Some producers use their 60 foot augers to transfer grain from the semi to the GBL bagger, running it through a 20 foot flexible drop spout into the eight-foot hopper on the bagger. Others prefer to spend $13,500 for the special Loftness truck auger because it attaches directly to the bagging machine.
Adair said that large prairie farms typically buy the complete system. Smaller farms buy a bagger and often share the cost of an unloader and truck auger with a neighbour.
“Everyone needs their own bagger because of the time issue. We’re all combining at the same time, so it’s hard to share the bagger. The timing for unloading isn’t as critical.”
Speed a plus
Nelson said the speed of a bagging system has made it the preferred method for handling corn in the U.S.
“Bagging in the field saves a lot of time during harvest. You don’t wait for trucks or the dryer or the elevator line. Guys just fill the bags in the field and keep the combines moving.
“Of course the biggest consideration is the fact that you can store your grain in bags for five to seven cents (US) per bushel for a year or longer if necessary. You can’t begin to approach that cost with conventional bins.”
The construction and chemical composition of a polyethylene grain bag is important in preventing grain grade deterioration. A ripped bag allows insects and air to get inside and allows fungi to develop. The bags must stand up to the elements.
There are numerous companies manufacturing bags for grain storage and their specifications are nearly identical. All firms say grain can be safely stored up to a year and a half when everything goes according to plan. A hole in the bag is not part of that plan.
The grain is safe from insects and fungi because the grain consumes oxygen in the sealed bag. In doing so, it expels CO2 that kills everything locked in the bag, thus eliminating the need for chemicals. Grain becomes dormant once oxygen has been consumed.
Although a grain bag looks about the same as a forage bag, Nelson cautions that there are differences. Grain, even at a low moisture content, is heavier than forage. A forage bag filled with grain might trigger a bag failure.
Grain bags have more ultraviolet inhibitors than forage bags and they are thicker, constructed with three layers of poly. Most have the UV filters in the outer two layers, with the inner layer made of black poly to keep out sunlight.
Grain bags are 9.3 mil thick, thus adding more sidewall strength to reduce the pillowing effect caused by the weight of the grain.
For more information, contact George Adair at 306-774-8559, Dave Nelson at 800-828-7624 and Kevin Fuchs at 800-803-8346 and visit www.loftness.com.