They look like great big floppy overshoes for your implement, but they’re custom tailored to fit all sizes
The tires versus rubber tracks debate sparked by CAT Challenger 31 years ago eventually subsided.
Tracks are now available for every agricultural implement that might ever need to work in mud.
The atypical wet weather we’ve experienced in the past couple decades fostered enormous growth in the rubber track industry, as did the awareness of yield benefits and reduced soil compaction.
Unmanned aerial vehicle photos now give farmers visual evidence that fields worked with tracks are in better shape than those worked with tires.
Read Also
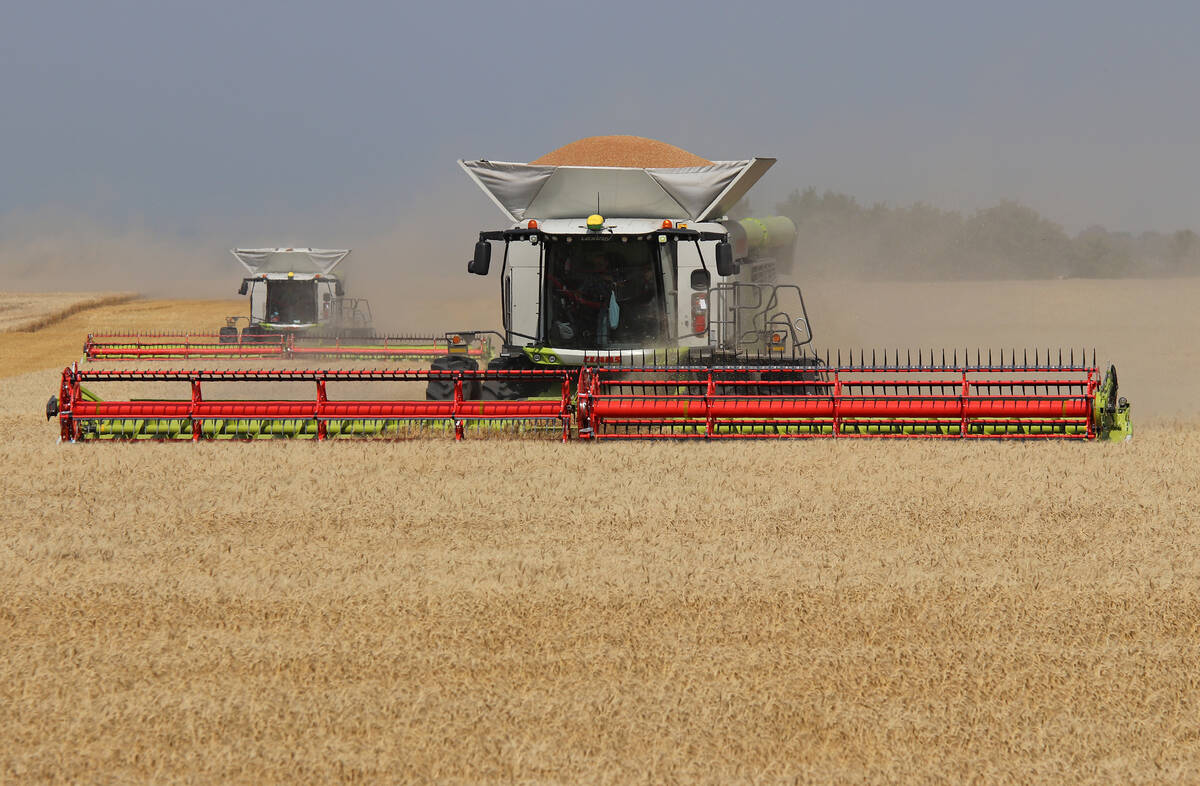
China’s grain imports have slumped big-time
China purchased just over 20 million tonnes of wheat, corn, barley and sorghum last year, that is well below the 60 million tonnes purchased in 2021-22.
Together, these factors inspired a new generation of fresh thinking and new track technology. A case in point is Right Track in Edmonton, owned by Tom Zaleski and Tom Zaleski Jr.
The company custom builds rubber tracks in any length and almost any width that a person might conceivably need up to six feet. That’s wide enough to make their unique belt go over duals on a New Holland TV145.
The belt itself is a 1,200-pound four-ply conveyor material that had its origin in the mining industry, where it’s been engineered to haul massive rock loads. A heavy-duty steel hinge allows the two ends to be spliced together to create a belt that is assembled to be the exact correct length required by the customer.
The tracks are characterized by extreme aggressive polyurethane grousers that can be changed from wild to mild for different conditions. Grade eight bolts attach the grousers to the belt. Using an impact gun, grousers can be changed or damaged ones replaced without removing the belt, said Zaleski Jr.
“We make everything to be re-buildable, starting with our first tracks 20 years ago. That’s when we developed tracks for pneumatic tires on skid steer loaders,” Zaleski said.
“With every other skid steer track on the market, it went to the trash when the outside tread wore out. When the outside tread of our track is worn down, you simply install new treads. You can do that over and over.
“We have other unique features. We have replaceable wear bars on the inside of the track so the tires grip the belt better and eliminate slip. The wear bars make the belt ride one-inch away from the tire, and that helps keep the inside free of mud.”
Zaleski said the company diversified from skid steer tracks to ag implement tracks eight years ago. For implements, it uses the same design concept but with stronger components. The list of possible machines includes irrigation pivots, manure spreaders, sprayers, trucks, trailers, grain carts, air seeders and tractors.
“Due to the custom nature of our product, we can design a track for any level of horsepower. We just adjust the belting, grousers and guide material accordingly. We haven’t found the upper limit yet,” he said.
“We’re building some tracks right now for log forwarder machines. They’ll be carrying 100,000 pounds and probably travelling up to 25 m.p.h. off-road. So we’re re-enforcing the components to take the weight. We still have not had a job where we couldn’t meet the requirements.
“We can build tracks for those new 500 and 600 horsepower four-wheel-drive tractors. We haven’t been asked to yet, but it’s 100 percent within the parameters of our capabilities.”
With belts up to six feet wide, Zaleski said the company can build tracks for any piece of equipment with a pneumatic tire. The belt has internal fibre nylon cords, but is smooth on both surfaces when it arrives at the factory.
He said the splice is like a giant piano hinge made of 3/16 inch QT100 steel with a mild steel rod for the pivot pin.
“The replaceable grousers are polyurethane,” he said.
“We have a variety of different configurations, from a low profile one-inch grouser all the way up to a 2.5 inch heavy duty grouser that can carry up to 120,000 lb.”
The replaceable wear bars are UHMW l poly. The saddles are made out of mild steel using a combination of 3/16 steel flat bar and 3/8 steel flat bar and are used to guide the tracks over the wheels so the track doesn’t slip off sideways. Saddles for dual tires have a prominent ridge in the middle to keep the belt centred.
Grade eight bolts from the outside pass through the grousers, the belting, the saddles and the wear bars.
The head of the bolt on the outside is countersunk into the grouser bar. It’s secured by a stover lock nut on the inside and the bolt is then cut flush to the wear bar so it doesn’t damage the tire. The inside is also countersunk.
Although wear bars are replaceable, Zaleski said it’s seldom necessary because they prevent the tire from spinning inside the track and therefore prevent wear. Components typically last up to three years before a re-build is needed. He said in 99 percent of cases it’s only the grouser treads that need replacing at that point, along with the bolts.
The same tracks are used for driven and non-driven tires. They can be built specifically for flotation on non-driven single tires, such as the front tires on a semi used for hauling grain out of muddy fields.
“We sell a complete track assembly that goes on the front axles of a semi. We take off the customers’ existing tires and replace them with two 9-R 22.5 tires with tracks fixed,” he said.
“One pair of tracks can be built to fit two different machines with different tire sizes or different axle spacings. First we build the belts for the shortest requirement. Then we build a spacer piece to splice in so the belts are longer for the bigger machine. Now the belt has two hinges.”
All rubber track systems have the same drawback: they’re made for off-road use.
Operators have to be careful on paved roads and gravel roads, whether the machine is a small displacement all-terrain vehicle or a 600-hp four-wheel-drive tractor, aftermarket or original equipment manufacturer.
“We suggest people keep road speed down below 30 m.p.h.,” he said.
“Our tracks are designed for off-road use, so they have very aggressive treads, and they’re not DOT approved.
“Installation requires less than an hour on a unit such as a manure spreader with a tandem or triple axle. Guys use a come-along with two pieces of chain. Drop the air pressure down to about 10 lb., then pull the two ends together until the hinges line up. Slide in the pin and bring the air pressure back up on the tires, and you’re done.”
Prices vary because the tracks are custom made for each machine. As an example, Zaleski said a pair of tracks for a single tire manure spreader run about $16,500, a dual tire setup with 11-R 22.5 tires cost about $19,500 and a triple axle is about $26,500.