Modern sprayers rely on rate controllers to keep the right amount of chemical flowing, no matter how fast or slow the machine is moving.
They are expected to handle five m.p.h. turns on headlands, eight m.p.h. swerves around sloughs and 20 m.p.h. runs on open ground, all the while applying the right amount of product.
Maintaining the rate is one thing, but getting it onto the field in a useful pattern is another.
Rate controllers drop the rate to meter out the right measure as speeds slow, but when they do, pressures fall. When that happens, spray patterns can turn from ideal to too coarse and inconsistent.
Read Also
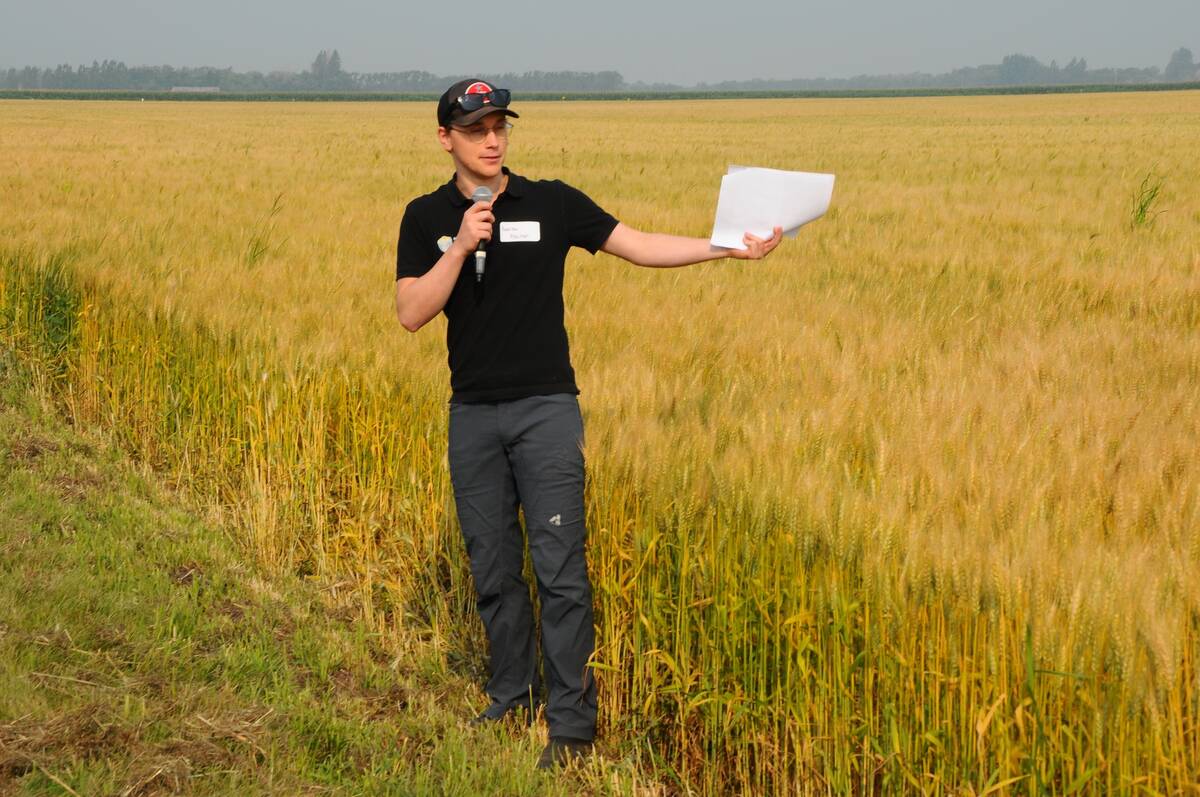
On-farm research translates science into ‘farmer speak’
Manitoba’s three major agriculture grower groups support farm-level research to test crop science under the shifting conditions of real farmer fields.
Modern self-propelled sprayers are also capable of out-running their own pumps or sending boom-line swelling pressures to the tips.
In both cases, the expectation is that the spray pattern will remain constant.
That’s why it’s important to use the right spray nozzle. Money spent on new nozzle systems might be wasted if the pattern, volume and droplet size don’t fit product requirements, the sprayer or the ground speed.
Agriculture Canada researcher Tom Wolf says producers have many choices when it comes to nozzles.
Using high-speed imagery, Wolf has shown the differences in spray pattern and droplet size with different nozzles at varying pressures.
Juggling drift to find adequate coverage and good canopy penetration requires minor compromises from a single nozzle if wide ranges in boom pressure are encountered.
Wolf recommends choosing nozzles, speeds and volumes that allow the sprayer to maintain spray with medium to coarse spray qualities.
A volume median diameter of 250 to 450 micrometres (uM) is preferable because it allows for the application of a variety of herbicides and targets.
Drift may become a problem at the finer end of this spectrum. At the coarser end, coverage on grassy weeds or the use of low water volumes will become more of a challenge.
Many advances have been made in tip design, improved rate controllers and variable rate systems.
However, researchers say most farmers still desire single, simple tips that will handle most of their spraying needs.
“A good compromise is the low-pressure air-induced tip,” Wolf said.
“At 40 psi, these tips typically produce very coarse sprays. This is a practical minimum for broadleaf targets but very good for drift control. At 80 psi, they produce coarse to medium sprays, a good choice for grassy targets.”
Wolf doesn’t think speed is the key to covering more acres in a day. He advocates wider sprayers at lower ground speeds for the best results, and said the best results are achieved at 15 m.p.h. or slower.
Operators should be more concerned about the quality of the job and should spray as slowly as the daily workload allows, he added.
“The main reason for this recommendation is that faster travel speeds create a number of problems that relate to weed control,” he said.
“A sprayer travelling at 20 m.p.h. might be operating at, say, 60 psi. At that pressure, the spray quality may be coarse. If the operator slows down for a rough patch, to go around an obstacle, or to initiate a turn, he may need to slow to 10 m.p.h. This will force the rate controller to reduce the operating pressure from 60 to 15 psi.
“At that pressure, the nozzle pattern will collapse, and the spray quality may be extremely coarse. Weed control will suffer under those conditions.”
By digitally capturing spray at 90 psi, Wolf has shown that the Tee Jet AI is capable of maintaining a good pattern while avoiding drift.
However, the same nozzle doesn’t do as well at pressures below 40 psi because the spray quality is too coarse. Sixty psi is a good general pressure for this nozzle.
In another example, the Greenleaf AirMix 11003 low-pressure air-induced tip can produce a wide range of acceptable patterns and droplet sizes.
“These represent the sweet spot in the market and can be considered good general purpose nozzles, not too coarse and not too fine,” Wolf said.
“Slightly higher pressures, about 50 to 70 psi, are needed to get the right spray quality.”
Localizing flow management can help control pressure at the nozzle. The Capstan Sharpshooter, also known as the CNH Aim Command, is a pulsing solenoid that regulates flow by altering pulse width, which is the length of time the valve is open, or duty cycle.
It can produce eight times the range of flow rates of a conventional nozzle system, and the pressure and droplet size change little as these tiny valves vary their duty cycles.
Jeff Grimm of Capstan Ag Systems said the valve attached to the solenoid acts as a pre-orifice controlling the flow while the tip sets the droplet size.
VariTarget is another pre-orifice design. It uses a plunger that controls the size of a valve opening just ahead of the nozzle’s tip, with results similar to the Capstan design.
It is capable of allowing one tip to provide a steady pattern of very coarse, coarse medium or fine patterns at a wide variety of rates and pressures.
However, changes to the droplet size require a tip change.
A major problem with this approach is the high sensitivity of the nozzle flow to spray pressure. A change as small as three psi can result in a 20 to 30 percent change in the flow rate.
As a result, applicators will need to be certain that their sprayer boom produces the same pressures along its entire length to avoid over and under application.
TurboDrop VR is capable of a wider range of travel speeds than a conventional nozzle, but this comes at the expense of pressure capacity.
The nozzle uses a second orifice governed by a spring-loaded check valve. Greater pressure increases flow.
The nozzle begins to operate well at 40 to 50 psi, but the maximum flow benefit requires a high pressure of 140 psi. This may be too high for some sprayers with centrifugal pumps.
Wolf said it’s similar to the VariTarget, but with less pressure sensitivity.
“One overlooked and under-marketed system is the Twin Fluid nozzle, which creates a variable sized orifice by injecting pumped air into the nozzle body,” he said.
“The more air pressure, the smaller the liquid flow rate. Spray quality can be managed by simultaneously changing the air and liquid pressure.
“In essence, applicators can achieve independent control of flow rate and spray quality with this approach,” he said.
“Although the system is available for purchase, it is not being promoted and is rarely used in North America. The concept is very good, though, and should have a future here.”
For more information, contact Tom Wolf at 306-956-7635 or -e-mail tom.wolf@agr.gc.ca.