FARGO, N.D. – Building a bigger cart is not merely a matter of super-sizing the previous 1,550 bushel unit.
It requires a fresh screen on the computer assisted design software.
Balzer engineers knew from the start their mammoth new Field Floater III grain cart would require fresh thinking if they wanted to avoid soil compaction and bogging down in the mud.
Weighing in at 32,750 pounds empty and able to carry 2,000 bu., the Balzer 2000 introduces technology other cart builders will no doubt study closely:
Read Also
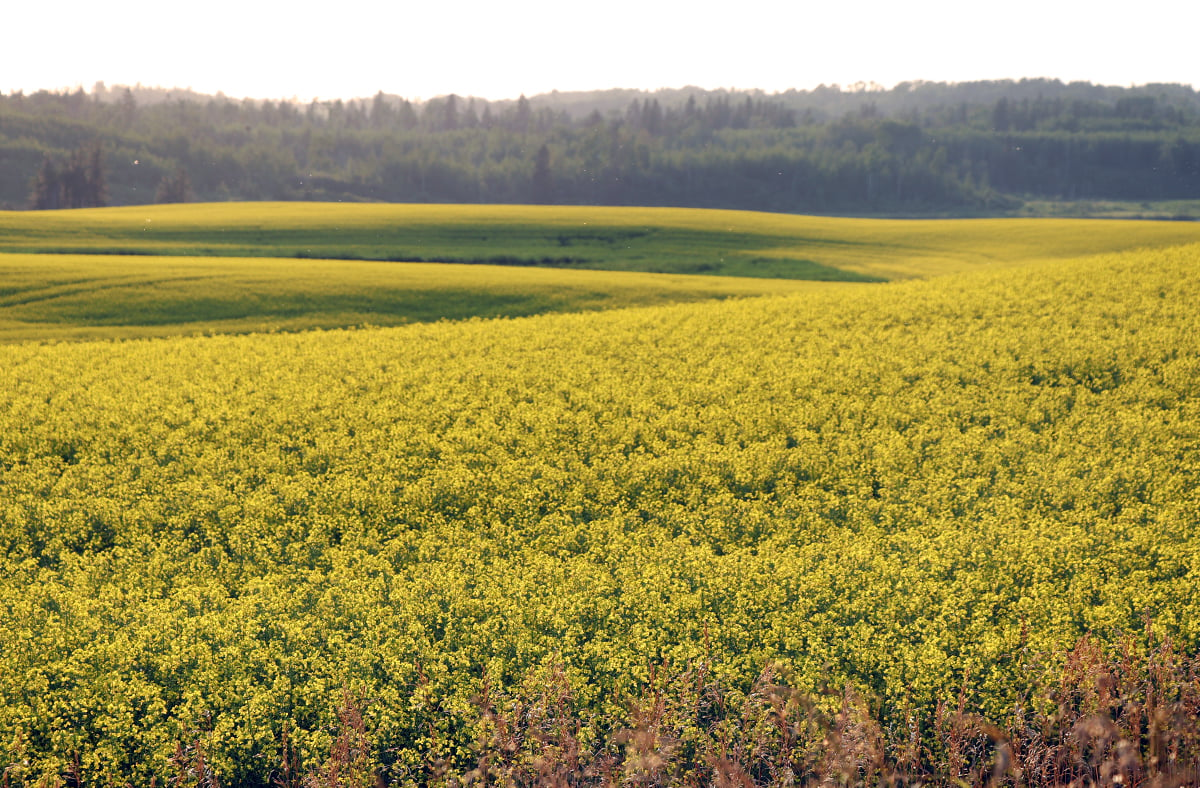
Agriculture ministers agree to AgriStability changes
federal government proposed several months ago to increase the compensation rate from 80 to 90 per cent and double the maximum payment from $3 million to $6 million
• six-wheel fully independent suspension;
• steering on front and rear axles;
• disc brakes that interface with the tractor brake pedal;
• separate controls for 20 inch horizontal flow auger and 24 inch vertical unload auger.
Jason Liechty of Balzer said a super- B can handle most of the load from the new cart in one trip.
The main advantage of the bigger cart is that it can service more combines and keep them harvesting without having to wait as often for a dump.
Weight distribution is another advantage.
Liechty said the problem of too much weight in the field becomes more significant as implements become bigger.
Compaction and a tendency to get stuck were both issues when Balzer engineers started designing the new cart.
They began with six 30.5 x 32 inch flotation tires on three axles, which spreads the weight more uniformly front to rear.
“Cart steering is important with this much weight,” Leachy said. “So we have hydraulic steering on the front axle and rear axle. The steering axles follow the tractor, so we don’t see that severe rutting and churning up mud in the turning areas.”
Steering is disengaged for highway transit and backing up.
Brakes on the two middle tires are standard, with optional brakes available for the front and rear axles. The system is compatible with the new tractors that automatically activate trailer brakes when the operator hits the brake pedal in the cab.
Liechty said the tridem axle system with six-wheel independent suspension is an industry first.
Agco Fendt has a prototype high-horsepower six-wheel drive tractor with three independently sprung wheels on each side. Balzer’s three-in- line system employs an independent closed-circuit hydraulic suspension for the left side and another for the right.
Each side of the system has three one-way hydraulic cylinders that resemble and serve the same purpose as regular shock absorbers, only bigger. They are connected in series, with one cylinder shock absorber for each wheel.
Each closed system plugs into the tractor hydraulics only for the initial pressure-up procedure. Once it’s set up, there’s no need to attach to the tractor again unless it needs more pressure.
The system is pressurized to carry the weight of the loaded cart with the cylinders riding at the halfway level. This allows each cylinder to travel up halfway or down halfway, absorbing field irregularities.
“If the front left tire rolls over a big rock, it compresses the front cylinder and sends that oil out to the other two left side shocks,” Liechty said.
“Or, if the middle tire drops into a badger hole, it draws oil from the other two shocks and that extends the middle cylinder to absorb the shock.”
The 24-inch vertical auger handles 1,090 bu. per minute, emptying the 2,000 bu. load in less than two minutes.
The horizontal flow auger is 20 inches and is controlled independently of the unload auger.
The unload auger has a bi-directional spout, which the tractor operator can move two feet left or right.
The operator can also move the spout in or out if it’s too close or too far away.
All spout position adjustments are made with a joystick the operator controls from the seat in the cab. The joystick also controls the grain doors in the cart and both augers.
The 24 inch vertical unload auger requires 150 horsepower to start and 75 h.p. once it settles down with a full load of grain. It’s driven directly by the gearbox.
The 20 inch horizontal flow auger is driven by its own individual clutch, controlled directly by the joystick.
It requires 120 h.p. to start and 75 h.p. once it’s running. Both augers are driven by a double number 100 chain.
Liechty said all the gates would be closed in a normal startup. The power take-off would be turned on, but that only starts the vertical auger.
“Once the vertical auger is up to speed, then engage the clutch to start the horizontal flow auger, start opening the gates and watch the grain flow.
“If you’re dumping and it looks like you’re going to spill, you can go ahead and shut it all down full of grain. Remember, you’ve got that clutch on the horizontal auger, so when you start up again, you go with the vertical auger first to clear it out.
“Same thing if you’re topping up a
Independent suspension for all six wheels is necessary for heavy hauling. The in-line design also eliminates many problems associated with duals.
A built-in digital scale above each wheel helps determine the right amount of pressure for the hydraulic suspension system.
load and you want to see how close you are. Shut off the horizontal auger and let the vertical auger clean itself out. Then you can tell for sure how close it is to full.”
Liechty said a farmer needs at least a 300 h.p. tractor to get full performance from the Balzer 2000. It’s possible to squeak by with 250, but efficiency will suffer.
The Balzer 2000 lists for $130,000 US and is available on the Prairies through Viterra.
For more information, contact Liechty at Jason. liechty@balzerinc.com.