There’s nothing new about dribbling on liquid fertilizer and incorporating it with a tine harrow.
However, doing it big and doing it fast gives the method a new twist.
Growers are placing less emphasis on one-pass farming. The utopian ideal of doing all seed placement, fertilizer placement and trash management in a single swipe compromises the quality of all three functions.
Instead, growers are placing more emphasis on the best possible placement of seed and fertilizer, even though it means two or three extra passes.
Read Also
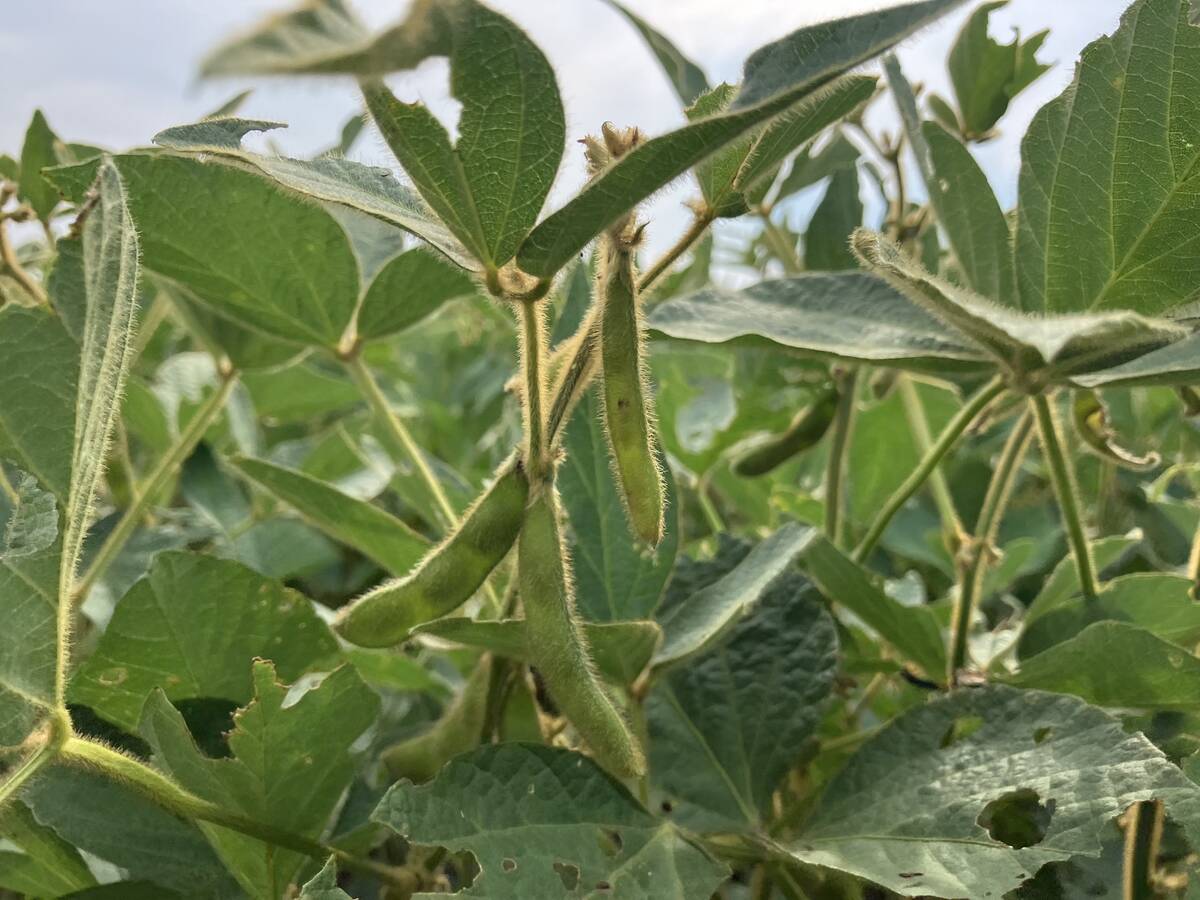
U.S. loses out on sales of soybean to China
U.S. soybean exporters risk missing out on billions of dollars worth of sales to China this year as trade talks drag on and buyers in the top oilseed importer lock in cargoes from Brazil.
The other evolving issue is the debate pitting conventional Canadian style equipment that’s big and slow against European style equipment that’s small and fast.
However, Elmer Friesen doesn’t look at it that way. He thinks he can do big and fast at the same time — and it looks like he’s right.
Friesen, owner of Elmer’s Manufacturing in Altona, Man., has been designing and building tillage and seeding equipment for nearly 40 years. Three of his most popular products are the 80-foot Super 7 Harrow, the NutriMaster fertilizer caddy, which can go as high as 6,500 US gallons, and driven and non-driven rubber tracks for field implements.
Last spring, Friesen was looking at his 3,000-acre family farm and thinking about making the seeding operation happen faster without sacrificing the quality of seed placement.
He figured that combining seed bed preparation with fertilizer application held the potential to save a lot of time.
Working with his engineering staff, Friesen married an 80-foot Super 7 to a 4,200 US gallon NutriMaster mounted on rubber tracks. He reasoned that the unique rig was big and it would be fast. As well, it would leave a good seed bed for optimal seed placement.
The shop ran one-inch flexible hoses from the NutriMaster to the Super 7 frame, mating them to PVC piping secured to the frame. Adapters were installed at each tine location with 1/4 inch flexible hoses running down to the tine. The small hoses connect to custom welded tubes on the front row of tines.
Harrowing immediately after the liquid was applied would ensure 100 percent incorporation into the soil. The rig was now ready to apply and incorporate virtually any type of liquid product.
The company conducted tests on Friesen’s farm by running the 80-foot rig with 28-0-0 at a rate up to 60 gallons per acre at eight m.p.h. on a 320-acre field. It fertilized and harrowed the field fertilized in 4.1 hours with an estimated time saving of 40 percent.
In the first scenario there’s a tractor, a harrow and caddy running simultaneously.
The 80-foot Super 7 with NutriMaster covers 77.5 acres per hour. The 320-acre field is fertilized and sprayed. Total time is 4.1 hours.
In the second scenario, there’s a 100-foot sprayer pass and then a tractor and a harrow pass.
The 100-foot Sprayer covers 181 acres per hour. The 320 acres are sprayed in 1.76 hours. Then the 80-foot Super 7 Harrow does a pass at eight m.p.h. taking 4.4 hours. For application and incorporation, the total time is 5.76 hours.
Nearly two hours of machine time can be saved purely on fieldwork, not including transport, preparation and maintenance.
Running the fertilizer caddy ahead of the harrow lets you fertilize and prepare the seedbed at the most opportune time and saves the cost of the sprayer and operator.
The large capacities of fertilizer caddies reduce the number of fill stops compared to the number of fill stops for a sprayer. Total weight of the full cart on tracks is 53,800 pounds. The non-driven tracks sell for $60,000.
When calculating any fuel savings, the results were deemed negligible because the increased weight the tractor must pull cancelled out the fuel consumption of the sprayer.