Big bale value | It can be lost in picking, handling and transport, but with the right equipment and a plan it can be saved
BRANDON — Livestock producers and commercial forage growers are well aware of the financial benefits of closely managing cutting, conditioning and baling their hay.
However, those best management practices disappear when it comes time to moving bales off the field, says Greg Haukaas.
Haukaas, who farms at Mortlach. Sask., and runs Haukaas Manufacturing, said producers spend a lot of money growing and harvesting a top quality hay crop, so it’s a shame to see them leave some of that nutrient in the field.
He and his father decided 13 years ago that there must be a better way to gently move big round bales off the field.
Read Also
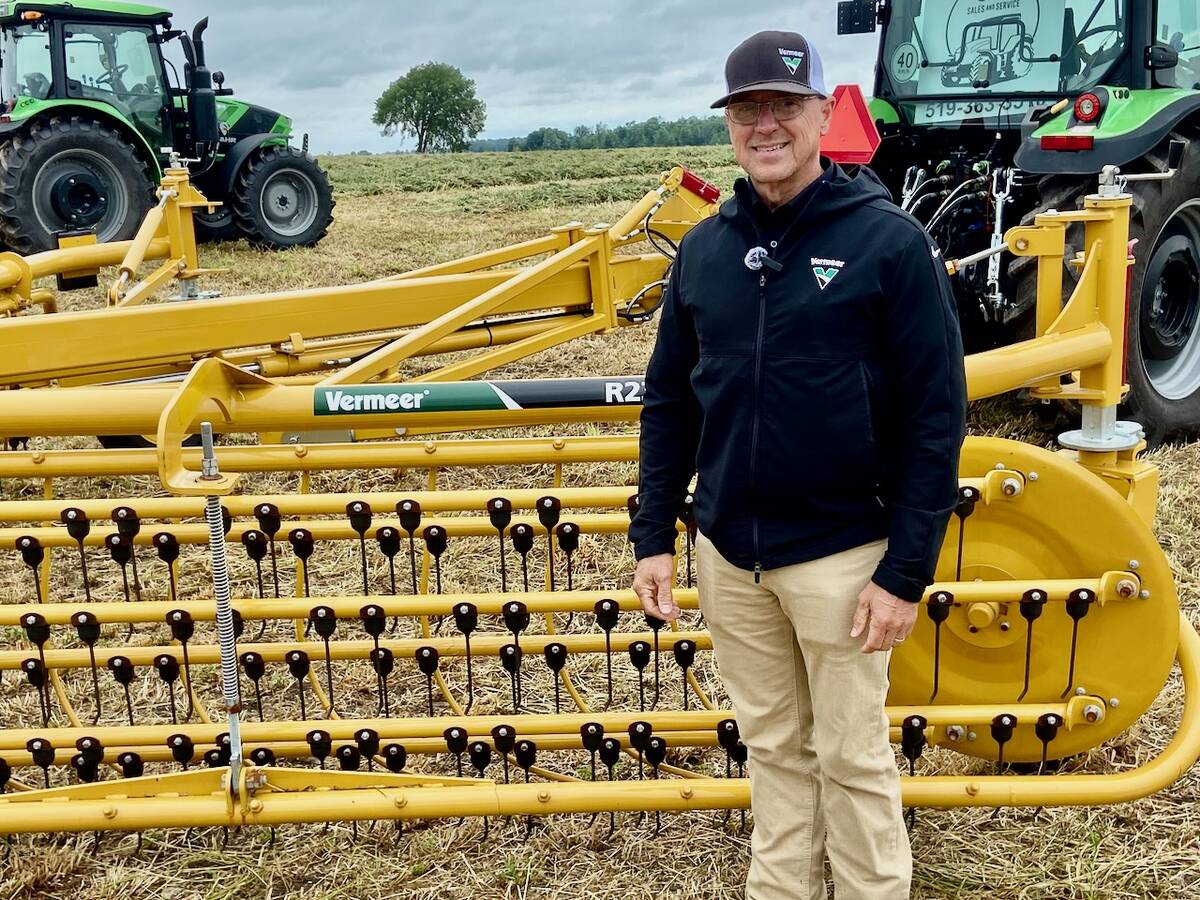
Basket rakes pitched for top-quality windrows
Boxy, clean windrows help make better hay bales for livestock farms and forage growers, and a basket rake excels in those areas, says Bart Elder of Vermeer.
“A hay bale is valuable. We should handle it like it’s a marshmallow,” Haukaas said.
“Our farm is nine miles (14 kilometres) north and a little west of the government hayfields here at Mortlach. We’d often drive past as guys were picking bales with a front-end loader and hauling them to the road. Each bale was handled many times so there was a lot of bale damage, bales coming apart. We said to each other there just has to be a better way.”
They looked at the chain and sprocket travelling-floor trailers and decided to build something better.
“Not only better, but it had to be fast. If the field isn’t too rough, we can pick and move 120 bales per hour, or about 1,000 bales per day,” Haukaas said.
The Quick Pick Bale Cart they designed picks up a bale by letting it slide into the chamber as the cart drives up to it. There are no arms or sharp projectiles to grab the bale and snag strings and wrap.
Each chamber holds five big round bales, which can vary in diameter from 48 to 72 inches.
The machine moves forward while bales accumulate in the chamber. Normally, the operator alternates between left and right chambers to keep the load balanced.
Pick-up speed for the first bale is four m.p.h. The next four can be picked up at six m.p.h. once the first bale is in the chamber.
To keep the ride smooth at those speeds, the chambers are suspended by flotation springs, which prevent the machine from gouging into the field’s surface. The chambers react to rough terrain as if they’re weightless.
The chambers ride at 14 inches above the surface in the field position with each chamber holding five bales of up to 1,500 pounds each. Once full, the two chambers fold to the centre of the trailer for road transit.
Each chamber has its own dedicated hydraulic circuit. The optional hydraulic rear gate requires a third circuit.
There are two ways to unload the bales.
The first method is to have the operator back the tractor out from between the dual rows while the chambers are down. Friction between the bales and field automatically deposits the bales in two parallel rows. This is the preferred method for loading to a semi.
The second method is easier. The operator uses the optional hydraulics to open the rear gate and then drives forward with the chambers lowered to the ground.
Each bale is always set down on the same side it sat on in the field. It never rotates off that original flat spot, whether it’s in the chamber of the cart, deposited on the ground at the gathering point or when loaded on a semi for transport.
“Every time you flip a bale, you end up with two spoiled spots. You damage the integrity of the bale and its ability to shed water,” Haukaas said.
“When you load them on the semi trailer, the flat always faces down on the deck so we don’t get roll-offs. It’s quicker to load and a lot safer.”
Haukaas said he doesn’t put up 10,000 bales a year like some farmers, which means he must learn a lot from his customers. Flaman Rentals has played a big role in the success of the bale cart, he added.
“They have a big rental fleet and they only buy our bale carts now,” he said.
“Flaman likes them because there’s no maintenance. I like the deal because guys will rent one of our accumulators from Flaman and then next year they come to us to buy one.”
The Quick Pick bale cart alone doesn’t guarantee an efficient hay harvest. It’s more about the overall system and how the cart is used.
Haukaas said the goal is to get the hay off the field in the least amount of time and with the least amount of damage to the bales.
“After we already had the bale carts on the market, we found out from our customers that the system to retrieve and move those bales is more important than the machine itself,” he said.
“The most efficient way to get that hay off the field and into the yard is to gather your bales and set them up in planned groups around the field.”
Haukaas said it’s important to arrange the rows of bales as they’re being accumulated. With the Quick Pick cart, the spacing between the two rows is ideal for a semi to drive between for quick loading from both sides.
For efficiency, Haukaas recommended breaking 160 acre fields into 10, 16 acre sections, or however many it takes to gather three loads of hay from equal shares of a field.
The bales should be loaded in each section in smooth, long passes with as little field tracking as possible and then deposited in a long row through the middle of the field.
Some operators can load a 53 foot semi trailer with 30 bales in just eight minutes, while others take 12 minutes or longer.
Bales are placed in two rows of 15 but can also be placed in two rows of 10 with two rows of five set perpendicular to the ends of the 10 rows. Either way, a truck is rapidly loaded.
In his literature and on his website, Haukaas has plotted out six bale accumulation patterns that a producer might typically employ. His model uses a square quarter section holding 320 bales that average 1,500 pounds each.
The six scenarios cover a wide range in terms of manpower efficiency. The least efficient is a tractor and loader carrying bales to a single point in on corner of a field, with 38.8 bales accumulated per man hour, pencilling out to nearly nine hours to empty the field. The best system removes 53 bales accumulated per man hour, working out to six hours to empty the field.
“There is no system for loading bales more efficiently than our dual row system,” Haukaas said, adding that the system has far-reaching implications for the future of beef production in the prairie provinces.
The days are gone when five guys looked after 1,000 cows. A typical operation today is a father and son running 700 to 1,000 head of cattle themselves with no hired help.
He said systems that function as one-man operations are the way of the future, and his bale cart and dual row accumulation scheme are the kinds of tool that make minimum manpower farming possible.
“Our bale cart is designed so one person handles large volumes of hay by themselves,” he said.
Haukaas paused before answering when asked how he developed the high-efficiency system.
“I’d really like to tell you that when we developed the bale cart, we had our whole system all worked out and we designed it to leave enough space between the bale rows to drive a semi in there. But to be honest with you, that’s just something that worked out later. People using our bale cart told us, ‘do you know I can load 30 bales in eight minutes.’ ”
For more information, contact Greg Haukaas at 306-355-2718 or visit www.haukaas.com.