FARGO, N.D. — There’s good news for farmers who missed out on buying the last of the Wishek Big Mac rock pickers.
The renowned rock picker is back under the name Big Mac III, complete with upgrades.
The Big Mac was originally engineered and manufactured by Glen Mack three decades ago.
When Wishek announced four years ago that it would stop building Mac, most people thought it was gone for good. However, knowing that the jigs were sitting idle, a Minnesota short-line manufacturer struck a deal with Wishek, and John Murphy ended up owning the jigs and the right to build and sell the machine.
Read Also
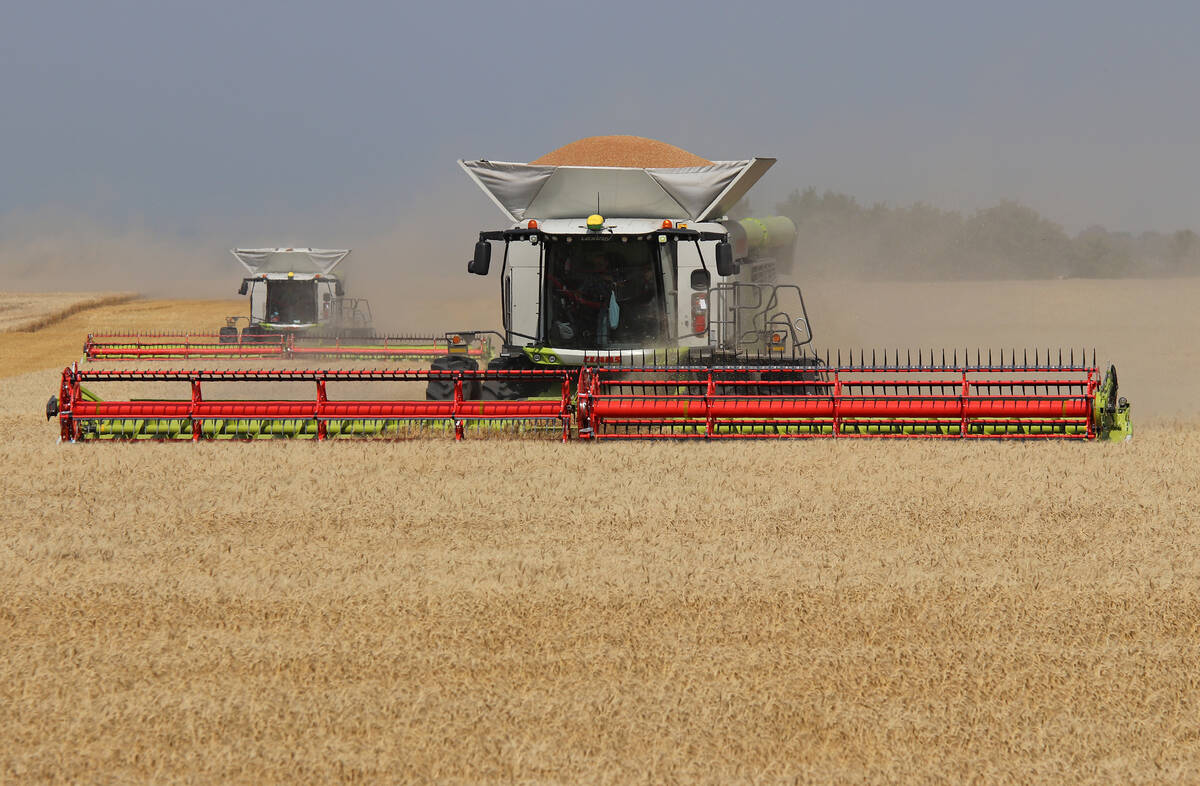
China’s grain imports have slumped big-time
China purchased just over 20 million tonnes of wheat, corn, barley and sorghum last year, that is well below the 60 million tonnes purchased in 2021-22.
At that point, steel prices were at an all-time high, so Murphy decided to sit on the project for a year, giving him time to make improvements on the latest generation of the picker.
“I already knew the weak points on the Wishek-built machine, so I fixed all those problems first before I started building my machines,” he said.
“Then two years ago, steel prices started coming down so I built 25 rock pickers. They all sold pretty quick, so now I’ve got 26 in the mill, and eight of those are already sold. There seems to be a strong demand, I think because so many people remember how good the original and the Wishek Big Macs were.”
Murphy said a key element is listening to what farmers have to say. If a farmer recommends a change, there’s usually a good reason for it, he added.
“Farmers told me that their latest generation of high horsepower tractors are built with an inherent rear visibility problem. The operator can’t see the front of the implement,” Murphy said.
“That’s especially important pulling a rock picker because the operator has to see the fork. So we came up with a three foot extension that bolts into the tongue, at the very front of the picker frame. That moves the picker back three feet. If we find that’s not enough, then we’ll provide a longer extension.”
One of the first things to be re-inforced was the fork that scoops rocks into the box. Murphy brought the fork from one of his own original Big Mac pickers to the manufacturing plant in South Dakota.
“I told them to look at every spot that’s broken or bent or that’s been repaired, then build the new fork so none of those spots will ever break again. And that’s what they did,” he said.
“The two arms that support the bucket used to be a problem. We have stronger arms now. If anything ever breaks on this rock picker, I know it won’t be the arms.
“That’s the process we used as we went through the whole machine. I can’t think of any spot on this picker that can break now. Our first Big Mac III pickers were delivered 2 1/2 years ago. We haven’t heard a single complaint about frame cracking.”
Murphy said the Wishek picker used to have axle problems. He uses a larger axle with eight-bolt hubs. The spindle is 2.75 inches in diameter. Tires are used super singles from semis.
The shaft on which the fork rotates had previously been a weak point. Murphy made a number of upgrades to the shaft, but concedes this component will always be the weakest link on any rock picker.
While the original shaft used to run in two half pieces of a pipe as a bushing, Murphy now machines the bushing out of a block of high grade steel. The block material above the shaft is 3/4 of an inch, leaving plenty of steel in case it ever needs to be re-machined.
“The shaft and the block are both high grade steel, so you still have steel on steel,” he said.
“That means you’ve got to keep it well greased. I don’t trust any of the bushings or bearings on the market. For the work these machines do, bushings and bearings won’t take the abuse.”
The hydraulic system is also new for Big Mac III. The double action cylinders are custom made by another Minnesota firm. With 25 units in the field, there have been no hydraulic breakdowns yet.
“If you can get a rock on the fork, I guarantee you can pick it up and drop it into the box.”
The box has a three cubic yard capacity, with a grated bottom and back so soil remains in the field. The slats are high carbon rolled steel.
The frame is five by seven inch high tensile steel.
Murphy said he tries to keep the price as low as possible by buying large orders of steel whenever prices are low. He sells the rock picker factory direct to the customer to eliminate the cost of going through dealers.
The list price for the Big Mac III is $17,000.
For more information, contact Murphy at 320-748-7183 or visit www.murphysalesllc.com.