BRANDON – The sloping front edge of the ATI High Idler rubber track configuration has attracted attention at prairie farm shows this winter.
“Wherever we set up the display, we get a crowd,” said Dale Shepherd, vice-president of Mazur Group, which is a dealer for ATI . “The shape seems to intrigue farmers.”
Shepherd said ATI is the only track manufacturer with an upward curved tip on the leading edge, which offers three main advantages over triangular or parallel configurations:
Read Also
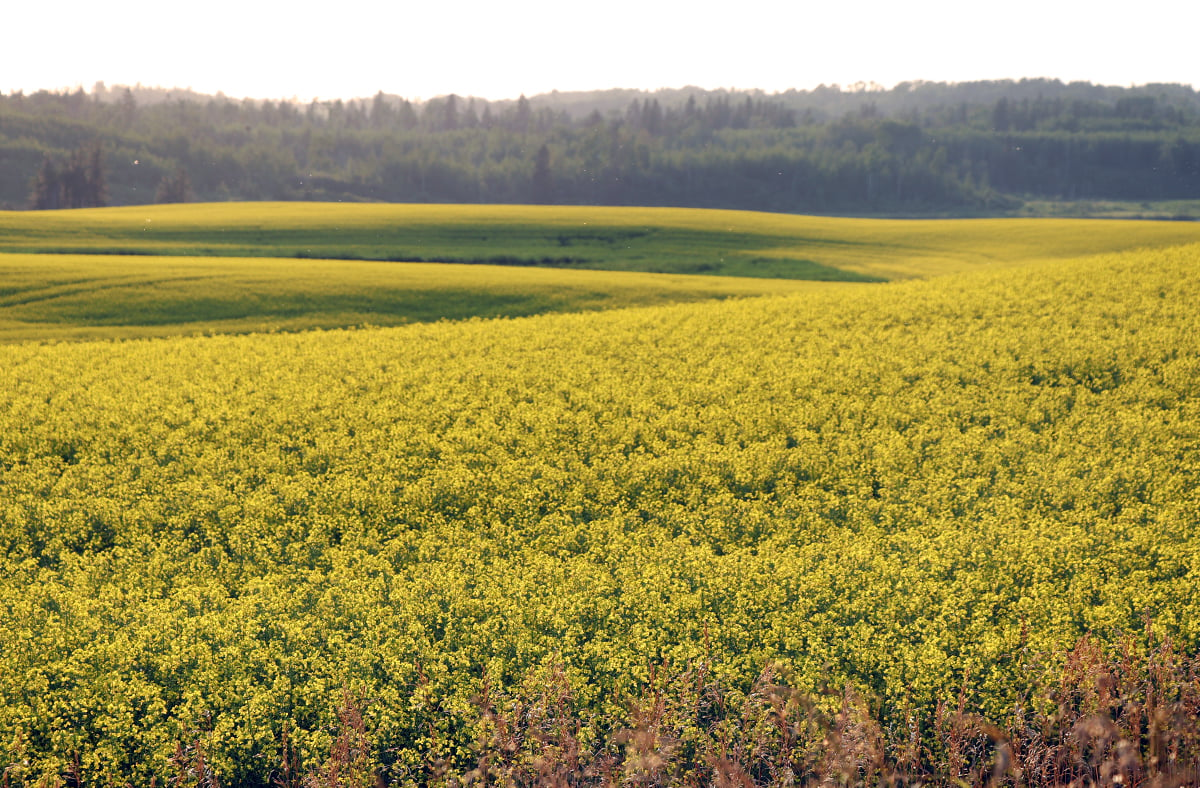
Agriculture ministers agree to AgriStability changes
federal government proposed several months ago to increase the compensation rate from 80 to 90 per cent and double the maximum payment from $3 million to $6 million
• the sled shaped leading edge drags residue and the best topsoil under the footprint to give better traction and flotation;
• it’s easier to drive in and out of ditches and over undulating terrain without excessive punishment to machine or operator;
• belt longevity is better because it has four corners to run around instead of just two or three corners.
“In normal conditions, which of course includes working in mud, High Idler belts last 6,000 to 7,000 hours,” said Shepherd.
“It’s one of the heaviest belts made by Camoplast, so it’s designed to take a lot of abuse.”
Indiana based ATI started building rubber tracks in 1994, with 75 percent of the systems going to the construction and seismic exploration industries.
“That’s all hard use equipment, so they’re no stranger to heavy, high horsepower requirements,” Shepherd said.
“That’s why the High Idler is so much heavier than other agricultural track systems on the market. And that’s also why it carries a three year or 2,500 hour warranty.
“The unit we have here, a single corner weighs 7,500 pounds and has a load capacity of 37,500 lb. The nearest competitor in ag tracks weighs just 5,000 lb. per single corner.”
He said the working mechanisms, including bearings and seals, are designed to go 7,000 hours before maintenance is required. There are no grease nipples or service intervals before 7,000 hours.
The High Idler is compatible with any brand of combine or four-wheel drive tractor. Shepherd said it bolts directly to the hub without adapters.
“This gives farmers the opportunity to make one investment in a high quality system, either a pair or two pairs, and keep them virtually forever.
“Switching back and forth is as easy as changing tires. A lot of guys are telling us they will keep their tires for dry seeding and dry harvest conditions. They’ll only bolt on the tracks when the mud merits it.”
Farmers might worry about equipping a tractor with two pair of tracks for wet seeding and then switching one pair to the combine for a wet harvest. However, this means the other pair sits idle.
“We had a customer in that exact situation in 2010,” Shepherd said.
“He bought two pair for his tractor. For harvest, he had no choice but to put one pair on the combine. But the other pair sat there bolted to one end of his tractor. He didn’t like that. Of course his neighbours were also fighting a muddy harvest.
“So he rented the other pair to a neighbour for seven bucks an acre. The neighbour harvested 3,000 acres. That’s $21,000 in rental for the extra pair of tracks.”
List price is $95,000 for two tracks.
Mazur decided to pick up the ATI line partly because his company is a New Holland dealership. Under the agreement between Case and New Holland, Case with its Quadtrac will remain the exclusive original equipment manufacturer supplier of rubber track tractors.
If a New Holland dealer wants to sell big 4×4 tractors with rubber tracks, it must be an aftermarket deal. In Minnesota, a New Holland dealer bought a Case QuadTrac and painted it blue for a customer who wanted a tracked NH tractor.
Faced with this challenge and the demand for rubber track equipment, Mazur decided to go with ATI.
Shepherd said a farmer buying a new tractor can order without wheels or tires.
“Wheels and tires alone can save you up to $60,000,” he said.
“There’s another $20,000 in frame and wheel weights you don’t need to buy.
“A lot of dealers are telling us they don’t mind selling a unit without tires. It’s a plus for them because tire brand and size is often an obstacle when trying to sell a used tractor or combine.
“When they take the trade back in a few years, it has no tires. That allows them to install the exact tire or track combination they need to close the sale for the next buyer.”
Shepherd said there are three reasons why farmers should consider rubber tracks on their combines:
1. Legal liability
“Class 8, 9 and 10 combines today weigh over 60,000 pounds with a big header, full fuel load and 350 bushels of wheat,” Shepherd said.
“There are no manufacturers today offering a tire package that’s rated for that much weight. It’s a safety issue and a very serious legal liability issue. Tracks provide the logical solution.”
2. Equipment failure
Combines can blow rims and beads when full in the field.
“It really ruins your day. If it’s muddy, it might ruin two or three or maybe four days. Those are days you should be combining.
“Dealers don’t warranty rubber. And rubber manufacturers will say that you’ve overloaded the tire, which is probably true. So it all falls back on the farmer.
“Plus, if it’s the left tire when the combine goes down, now the end of the auger is about four feet off the ground and the ladder is twisted. It’s an expensive mess.”
3. Time management
“Because most modern combines harvest 2,500 to 3,500 acres each year, it’s an expensive piece of machinery that works for a relatively short period of time.
“When a combine is sitting still because the field is too muddy or it’s stuck or it blew a tire, it represents a lot of dollars not going into the bin or into the bank.
“Why have you spent all that money on inputs just to leave your crop standing in the mud? Simple economics tell us that an investment in a quality track system can protect your crops for many years into the future.”
The High Idler is 67 inches high with a 36 inch belt width and 100 linear inches on the ground. Total surface contact per unit is 3,095 sq. inches. Belt length is 252 inches.
The drive is a self-tensioning positive system with seven or eight cogs engaged at any point in time. The undercarriage has a centre pivot with oscillation of 12 degrees up and down.
Shepherd said ATI also builds a more conventionally shaped triangular track system, but it has a large drive wheel at the top that reduces belt wear.
For more information, contact Shepherd at 204-728-2244 or visit www.ati.tracks.com .