FARGO, N.D. — From the side, there’s a visual similarity between the preying mantis and the Rock Mantis, the big difference being that the Rock Mantis eats stones instead of bugs.
Measuring 52 feet long, the Rock Mantis RP1000 is one serious stone-picking machine.
It harvests rocks up to one foot in diameter while cruising across your fields at three m.p.h. At that speed, it can remove 23 cubic yards of rock per hour, working at a depth of two inches.
The machine takes in a 20-foot wide swath with the windrow arms fully extended. It lifts to a height of 12 feet when the hopper is full and dumps its load into a waiting tandem or trailer in less than 60 seconds.
Read Also
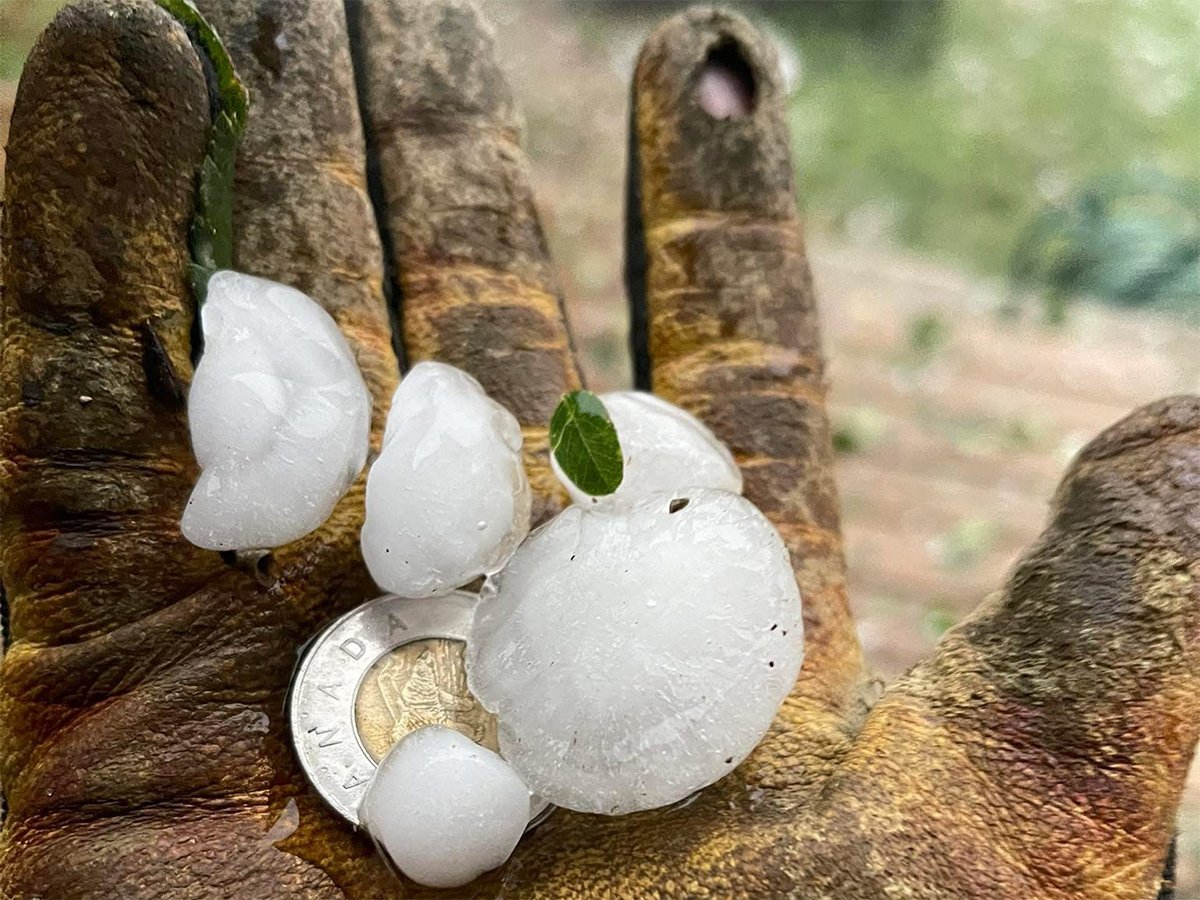
Half million acres of Alberta crops affected by massive hail storm
Late August hail storm catches farmers in prime harvest mode, damaging half million acres of crops in Alberta.
The Rock Mantis heritage dates back to the early 1950s, according to Niel Somero of Davis Village Solutions in Michigan, which now builds the machine.
“In North America, the real guru of rock picking equipment is Harley Fahrenholz from northwest Minnesota,” said Somero.
“He built rock pickers way back in the 1950s through the ’70s. Many of the rock picking designs and styles we see today evolved from Harley’s original inventions.
“He’s the guy who decided to use a mesh reel or a mesh tube to process rocks and get the dirt off. I don’t think he ever made any two machines the same. He was always making upgrades, coming up with improvements. He originated the Harley Rake attachment for skid steer loaders.”
Somero said rock picking is a time-consuming process regardless of what machine is used. Rocks have to be windrowed and then picked up and hauled away.
Fahrenholz’s neighbour, Mel Aho, eventually put all of the patented inventions into a single machine with a dump wagon at the back.
Starting with a working combine, Aho assembled the twin windrowing rollers, conveyor belts, mesh reel and dump cart into one long rattling machine.
Somero said Aho’s machine did what it was intended to do when his company got involved, but keeping it working was a challenge.
DVS couldn’t depend on junkyard parts if it was going to commercialize a bigger picker. Every component had to be new and reproducible on a production line. DVS engineers used the Aho combine as a pattern to design an all new Rock Mantis RP1000 from scratch.
“We’d known Mel for years, so we got together with him and worked out something with his patents because he had things to do other than go into manufacturing,” Somero said.
“We went right back to ground zero and started over.”
He said the new RP1000 has a John Deere combine cab, which DVS modified for its control system.
The 250 horsepower John Deere diesel spins three Bosch Rexroth hydraulic pumps, which power all functions on the picker.
The end result goes on a heavy-duty chassis designed by DVS with centre-articulated steering.
A rock picker lives a brutally violent life, regardless of the design or who builds it. Components are worked to the limit.
As a result, Somero said the first generation went through a number of changes.
“Initially, there were a few things that jumped out and bit us right away, and we re-designed those elements,” he said. “Once we worked through those, it’s actually been a pretty robust machine.
“Of course there are wear parts. Anything coming into direct contact with the rocks is designed to be replaceable, some of it in the field. The tubes that bang the rocks into a windrow take the worst beating. The wear bars on the tubes have to be replaced periodically. They’re welded to the tubes.”
The full working width is 20 feet, but Somero said the operator always allows for overlap, which means the practical width is about 16 feet.
“Where the rocks end up windrowed in the centre of the machine, we modified the original Harley design,” he said.
“We have a rubber conveyor belt that runs right down into the dirt. As the machine moves forward, the rocks are forced up onto the belt.
“The belt runs them up into the trommel screener. The trommel shakes off all the dirt, and the clean rocks go up the next conveyor into the cart. The screens are changeable in the field, so the operator can adjust the stone size to meet the landowner’s requests.
“If the farmer wants to remove everything over one inch, we can install aggregate screens to accommodate that,” Somero said.
“But of course, that means the machine has to work more slowly, so the cost goes up.”
The operator controls the hydraulic down pressure on the two windrow tubes, which determines the working depth of the bars.
Somero recommended running the cylinders about two inches into the soil at about 60 r.p.m. He said the field should first be worked with a chisel plow or shovels to loosen the rocks.
“The more effort the farmer puts into field prep, the more rocks we can remove,” he said.
“We can clear more acres per day, and the cost to the farmer goes down. We like to see nice loose soil with lots of rocks brought up to the surface.
“We have potential buyers who are clearing bush and turning it into tillable land. They’re starting from scratch, and they want to pick up roots and rocks and debris so they can farm new fields. We’ve tried that, and it does work for that.
“In some areas, aggregate for roads and construction and concrete is very expensive, so we have people who simply want to harvest aggregate. Of course, we know it works for that.”
Somero said the Rock Mantis RP1000 sells for US$450,000.
For more information, contact Somero at 906-353-5151.