Learning where your losses are occurring at the back of the combine is critical to putting money in your pocket
HUMBOLDT, Sask. — Harvest time is another opportunity to increase yield by reducing what stays in the field.
Combine losses are typically acceptable at a bushel per acre, depending on the crop. The number is more if it is a heavy feed barley crop and less if it is canola or flax.
For every bushel lost in Western Canada, the cost to the primary producer is about $500 million annually.
Like any application of resources in the field, there is an economic threshold that needs to be observed.
Read Also
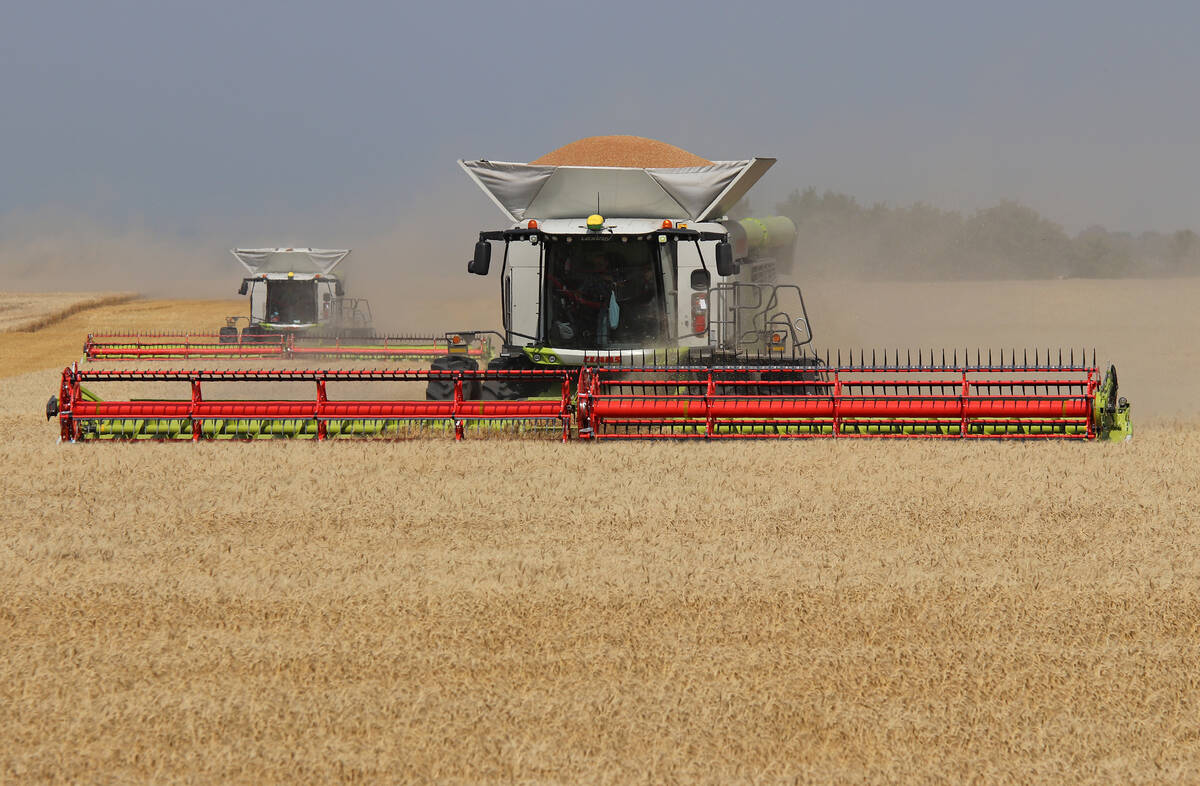
China’s grain imports have slumped big-time
China purchased just over 20 million tonnes of wheat, corn, barley and sorghum last year, that is well below the 60 million tonnes purchased in 2021-22.
Farmers can make choices to invest more time harvesting a crop or choose more acres per hour, depending on the price of the crop or the risks related to grade loss, time of year and delivery opportunities.
However, producers can typically make improvements to combine settings that don’t entirely rest on slowing down to what feels like a crawl when sitting in the cab.
Joel MacDonald, who manages agricultural development services at the Prairie Agricultural Machinery Institute, said farmers need to first find out exactly what they are leaving behind and put a price on it before they start making changes to their machines.
“What would you spend for another three bushels of canola per acre? Apply some fungicide? Add 10 pounds of fertilizer? Look at new drill? You would likely invest in that crop. Combining is not that different,” he said.
He recommended dropping the straw and chaff into a windrow at the start of harvest and measure what is going on the ground.
“Whether you use sophisticated drop pans or Tupperware containers, so long as you can measure that and compare it to your harvested (area), you can evaluate your losses and make decisions from there,” said MacDonald.
Using a pan is critical because some losses on the ground can be related to shattering at the header or leaks in the processor or feeder and need to be accounted for separately.
Machines typically also have left and right side loss differences related to the way the deflectors are set, and producers can often get some clues from the side of the machine where the losses appear.
There are myths about combine losses that PAMI hopes to put to rest, including that machines running relatively lower amounts of material don’t harvest as efficiently.
“It is possible, with a very small seeded crop, like canola, to run too slowly and have seed losses off the grain pan, but that is going to be, like say half a mile an hour,” he said.
“We have a lot of testing results, and 99 percent of the time losses increase along with feed rates,” he said.
“Slowing down usually results in lower losses, but you have to measure to find out.”
A second compromise will also have to be made: either over-process the crop at the rotor or cylinder level, resulting in overloading the grain pan with material other than grain, or under-process it and send crop out the back of the machine.
Discovering where losses are occurring is critical to getting the most capacity out of the machine.
MacDonald uses a one foot square Tupperware container attached to a broom handle to reach into the bottom side of the crop flow, while dropping the straw, and later the topside.
“Then you can find out where your seed is going when not into the tank,” he said.
Speeding up rotors or the cylinder and tightening the gap will cause more material on the grain pan and reduce losses at the top of the system.
Managing fan speed and sieves will handle the shoe losses.
“You should be seeing similar losses off top and bottom, and for most machines it means you will be set about right,” he said.
A loaded stall test can show how well the shoe is loading and whether it needs to be adjusted or recalibrated or if those sensors are not delivering the right messages.
Manufacturers point out that a quick engine restart with the processor off is required to keep oil flow to the turbocharger and let the non-threshing components cool down properly before being shut down to examine the load on the shoe.
And that is when producers can refine the threshing job, reducing chaff in the grain and consider cracking and other issues.
Finally, the loss sensors should be calibrated so that the operator knows when to slow down and what is acceptable.
“Unfortunately losses change at different times of the day,” he said.
“Three in the afternoon is different than 10 at night when things are getting tough and you can start to speed up those rotors to keep knocking it out without as much risk of cracking the sample.”
- Savings by increasing speed to 4 m.p.h.: 2.8 hours (D) x $325/hr combine operational fees = savings of $910
- The gross cost of crop losses would be $3,330 to go one m.p.h. faster (E). However, after subtracting the additional combine operation hours, the loss on that quarter section falls to $2,420, or $15/acre.