Better machinery | Producers are investing in sophisticated equipment to save time and speed drying
High grain prices are prompting farmers across North America to convert their hayland into cropland, which is good news for serious forage producers.
There are internet reports of hay delivered in Texas for $380 US per ton, while prices in the northern border states exceed $200 per ton. A hay dealer in Langley, B.C., is listing timothy, orchard grass and alfalfa at $290 to $400 a ton.
Canadian prairie forage producers are not yet seeing those kinds of prices, but the trend toward fewer forage acres across the continent will eventually push prices higher. It’s likely that a significant amount of transportation will be required to realize those prices.
Read Also
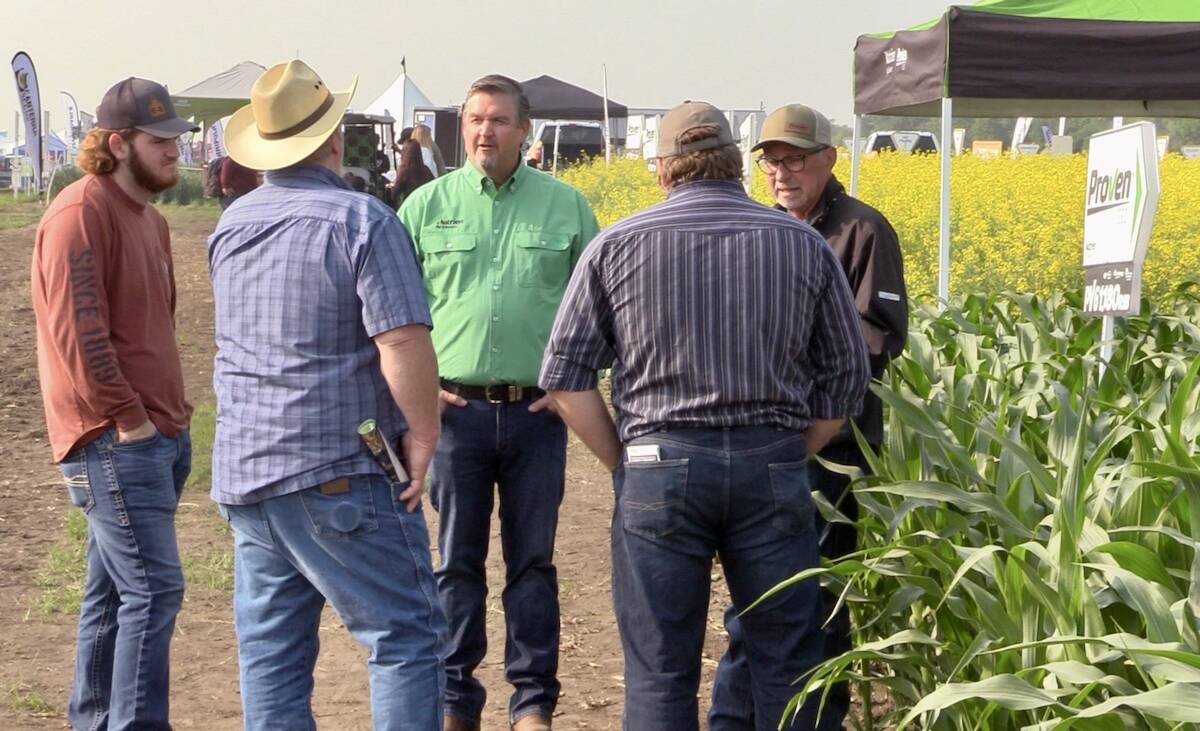
Interest in biological crop inputs continues to grow
It was only a few years ago that interest in alternative methods such as biologicals to boost a crop’s nutrient…
Hay and forage producers will have to do everything possible to get all they can out of every acre to take full advantage of this situation, says Kevin Shinners, an agricultural engineer at the University of Wisconsin in Madison.
“That means drying the crop as quickly as possible by conditioning, getting it into storage and keeping it protected so we maintain its value,” Shinners said.
“Especially when hay prices are $200 to $300 per ton, baling when the moisture content is too high or storing hay poorly has real negative economic impacts.”
Shinners sees a trend toward more sophisticated, efficient equipment such as self-propelled harvesters and custom harvesters that handle more acreage. For larger producers and custom harvesters, it’s all about productivity, rapid road transport and efficiency.
Case IH forage manager Brett DeVries say said producers need reliable equipment to put up the most hay in the shortest time.
“Hay tools have been evolving to do exactly that,” he said.
“Machines are bigger, with wider cutting widths so you can get more done in one pass.”
DeVries said Case IH recently introduced a new disc header for self propelled windrowers.
At 19 feet wide, the RD 193 is the largest disc header in the industry and requires less horsepower to operate than previous models.
Saving time is also important, which is where large square bales and round bales that don’t require tying can help.
“On a Case IH round baler, you can choose twine or net wrap with the push of a button,” he said.
“On the large square baler there’s an auto loop system, so you don’t have to grease the baler every day. It greases automatically, saving time and money.”
Shinners said telematics will soon change the way hay is produced and harvested. It will let a farmer re-motely capture data from harvesters and tractors.
“A farmer can sit at a computer and see if the harvester is moving in the field and can tell when another truck or crew is needed,” he said.
“If we can track things like fuel use and tonnage in each field, we can really start to get a handle on costs, figure out where there are inefficiencies and determine how to overcome those problems. The productivity benefits of this type of system are obvious.”
Added DeVries: “A bale weight system lets you monitor and control bale density, shape, weight and length, all from the cab. You can monitor the moisture content in each bale, so you know exactly what you’re putting up.
“With telematics, we’ll also be able to direct all that information to a computer, along with real-time information about how the equipment is operating.
“Starting this spring, dealers will retrofit AFS Connect Manager and AFS Connect Executive packages on fleets of both Case IH and competitive equipment as part of its commercial introduction of Case IH telematics technology.”
A radio frequency identification tag on a bale can store information about the quality of the bale, including which field it’s from, where in the field it was made and its moisture content.
Producers can then feed the highest-moisture bales sooner and store the driest-moisture bales longer. They can also decide which bales to sell first and how to price them.
Quality and value depend to a great extent on weather because hay and hayage often require extended drying time in the field.
Shinner said producers can’t change bad weather, but they can take steps to mollify its impact.
“One of the most important things is to utilize the sun’s energy to the maximum extent,” he said.
“At cutting, lay that crop down as wide as possible so that almost every square foot of the field is occupied by drying crop.”
Anything a farmer can do to dry hay quicker so that they can get it out of the field and miss a rainstorm is money well spent. A mower conditioner is a good tool to speed dry down.
“Engineers have done decades of studies that show the advantages of mechanically conditioning the stem and what it does to improve drying rates,” Shinners said.
“A mower conditioner also gives you flexibility to produce either dry hay or haylage.”
He admitted his recommendation to always mechanically condition haylage is controversial because some people suggest that they can slow down the drying rate by not conditioning. Once it reaches the ideal chopping moisture content, they argue, it will stay there for a longer period of time.
“However, without conditioning, the crop will take longer to get to the optimum moisture content, and you put the crop at risk of weather damage,” Shinners said.
“I’m a proponent of conditioning at all times. You shorten the period of time to get to the optimum moisture content, so we can get that crop off the field and protected.”
He cautioned growers to avoid tedding or raking when the leaves are brittle.
Shinners said there are three keys to quality hay and haylage: cut it at the right stage of maturity, dry it as quickly as possible and be gentle with the crop.
“Progressive dairies recognize that the way to maintain forage quality is to have high productivity harvesting equipment,” he said.
“When the weather is right and the crop is mature, you can’t plod along like Grandpa did. You need to get through those acres as quickly as you can, and get into the next growing cycle. In Wisconsin, we’re trying to cut haylage on a 28 to 30 day cutting cycle to have more uniform crop quality and higher quality forage.”
DeVries said it’s a similar story for commercial hay producers in the western States, where the rule of thumb is to cut and bale it in three to four days.
Shinners reminded growers to make sure the conditioning rolls are set up correctly to reduce the mechanical resistance of moisture leaving the plant. The clearance needs to be set so the stem is cracked every three to four inches to open up routes for water to leave the plant.