Under current regulations, there is no requirement for brakes on farm trailers, carts or wagons. Most manufacturers offer brakes as an option, but very few farmers spend the extra money.
“The number of farmers ordering optional brakes would be less than five percent, way less than five percent,” says Mike Friesen, president of Elmer’s Manufacturing.
Friesen is an engineer. He knows machinery from the moment it’s a mere whim right through to the time it’s working on his own family farm at Altona, Man., or on farms across North America and Europe. His father, Elmer Friesen, launched Elmer’s Manufacturing in 1978. Designing farm equipment seems to run in the family.
Read Also
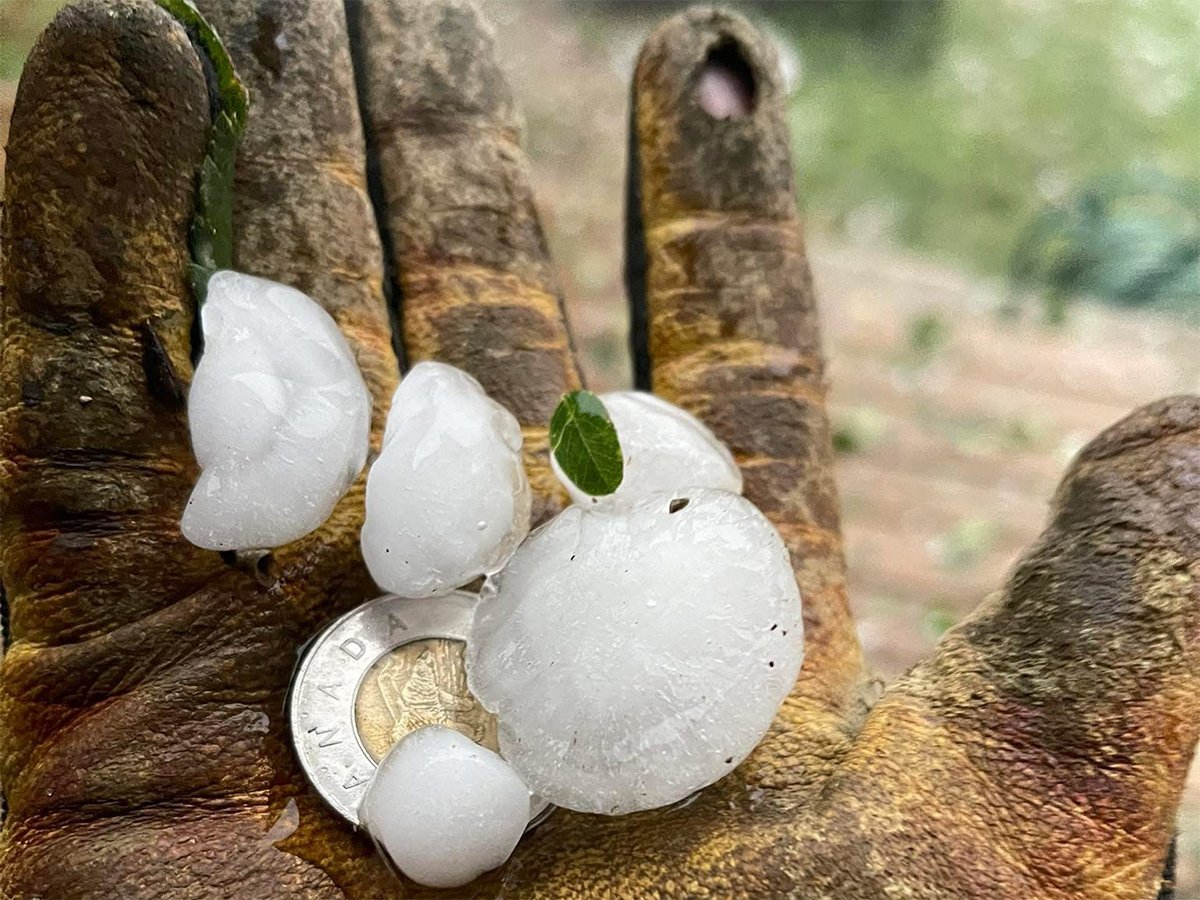
Half million acres of Alberta crops affected by massive hail storm
Late August hail storm catches farmers in prime harvest mode, damaging half million acres of crops in Alberta.
Friesen said his company does a lot of business in Europe, so it must design every piece of equipment in accordance with strict European standards, including brake systems. It evens make harrows with brakes.
Although the full line of Elmer’s equipment sold in Canada can be ordered with the optional brake package, only one or two customers per year check that option box, usually on the big grain carts with rubber tracks.
At a list price of only $10,000 for brakes on a grain cart, it’s likely not the cost that prevents farmers from buying the brake system. Friesen thinks it’s simply an awareness issue. He said that if operators understood the benefits and safety aspect of brakes on trailers, they would check that option box.
“When equipment was smaller and lighter, you really didn’t need brakes, so a lot of it is just habit. People think they never needed brakes before, so they don’t need them now. The other thing is that manufacturers don’t promote brakes. And they should.”
“We’re seeing more brakes on big air seeders. We’ve all seen those pictures on Google of an air seeder piled up at the bottom of a creek at the bottom of a hill.
“Some of our grain carts can weigh 60 to 70 tonnes when full, so there are some farmers ordering brakes in Alberta and Saskatchewan where they have big hills. The tractor just can’t stop that load. They want the brakes for safety going down the hills. Finally, some companies are putting standard equipment brakes on these massive tanks they’re building. And we’re seeing more tractors built with a hydraulic brake system that’s tied into the foot pedal.”
Friesen said the Elmer’s brake is a drum rather than a disc. It’s a hydraulic system that’s actuated from the tractor brake with electrics, hydraulics or air. The actuator for air/hydraulic is from Mico. The actuator for electric/hydraulic is from Titan.
Paul Degelman’s giant M34 manure spreader offers optional brakes, but he says despite a low $8,000 price tag, only five percent of growers buy it. It relies on four piston calipers squeezing discs on each axle.
Bourgault engineers took a fresh look at the problem of carts driving horses. Operators sometimes can’t react fast enough when a heavy air cart or product wagon starts pushing the tractor. Operators need a foolproof automatic system to activate the cart brakes in those situations, said Bourgault’s Rob Fagnou.
“Beginning last year, we install a standard equipment surge system that triggers the cart brakes on the bigger carts. If the telescoping hitch on the seeder bumps up against the tractor, the module automatically throws on the cart brakes,” said Fagnou, adding that the engineers stopped using the electric activation from the tractor brake lights in favour of the new automatic device.
“It only takes a slight nudge, but there are times when that nudge can turn into a crisis if the brakes aren’t applied immediately. It can disorient the driver enough that he can’t reach down to the brake activation switch in the tractor cab. Things get dicey very quickly.”
During prototype testing in 2014, an operator with a surge equipped 7950 seeded downhill on a grades of 15 degrees, as recorded on his GPS gyroscope. Most operators feel 11 degrees downhill is risky enough.
“Installing brakes on big carts is a matter of common sense, regardless of whether or not there’s legislation. It’s a matter of customer safety. There may be laws coming into effect sometime down the road, but we’re doing this because it’s the right thing to do.”
Fagnou said the system is standard equipment on the 71300 and 7950 carts and available as an option on the 7700. The L7800 uses a pump accumulator brake system. He said the 76 foot Bourgault weighs nearly 50,000 lb. The 950 and 1300 carts are 50,000 lb., as well as the weight of product and possibly liquid or anhydrous ammonia tanks behind that.
“We have disc brakes, but to get enough clamping force, we have two callipers on each rotor. The only problem we’ve had is when someone inadvertently left the brakes on when they went out to the field.”