Changing concaves to match every crop and field condition might improve axial flow combine performance, but it’s a grueling time-consuming task.
John Deere STS owners understand the benefits of an aggressive concave for tough conditions and a smooth concave that’s gentle on canola, but it’s hard to justify taking time to change concaves in the rush of harvest, said Gerald Foster of Sunnybrook Welding, one of the leaders in cylinder and concave engineering in the past two decades.
In 2008, Foster investigated complaints he heard from producers who ran axial flow combines. The main complaint was capacity in canola, followed by unthreshed heads in cereal crops.
Read Also
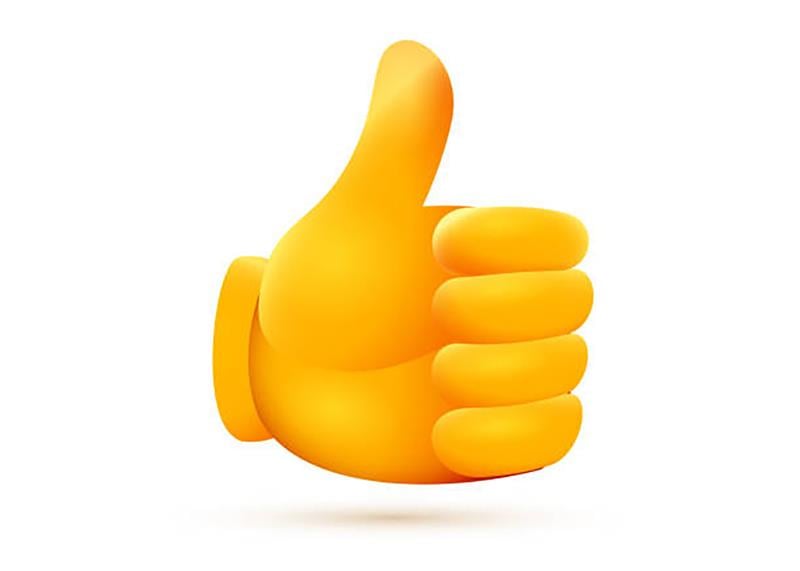
Supreme Court gives thumbs-up emoji case the thumbs down
Saskatchewan farmer wanted to appeal the court decision that a thumbs-up emoji served as a signature to a grain delivery contract.
Two seasons of research and development, field trials and talking to farmers pointed Sunnybrook in the right direction for a remedy.
“Axial flow engineers took the conventional concave, turned it sideways and then dusted their hands of the whole deal,” said Foster.
“The problem is that material flows tangentially, at an angle as it moves through a processor. It’s not in full contact with the curved surfaces,” he said.
“Building multiple radii into the design helps, but that wasn’t the complete answer. It still left a lot of opportunity for improvement.”
Foster reasoned that a concave frame with seven interchangeable bolt-in boxes of various designs would
allow combine operators to fine tune the threshing mechanism to specific harvest conditions without having to wrestle a 40 kilogram chunk of steel in and out of the pocket.
Each Sunnybrook frame is half the width of one factory John Deere frame. Up to six Sunnybrook frames can be used instead of three Deere frames. Two Sunnybrook frame sections bolt together to form a single concave section that drops into the regular pocket, so there’s no modification to the combine.
Because they are half-width, the STS owner will need to buy Sunnybrook frames in pairs, said Sunnybrook vice-president Dale Mackenzie.
He thinks many owners will start with two or four frames, using them in conjunction with the factory frames, and then add more pairs as they realize the benefits.
Each box weighs about 1.3 kilograms. A half-width Sunnybrook frame weighs about 25 kg when all seven boxes are bolted into place.
“Some of the guys who tested the concaves this year said they could change out a frame in less than five minutes,” said Mackenzie.
“On the full width John Deere frames, you have to roll the rotor a couple times to get things positioned to pull one frame. It took some time. With the half-width frames, there’s no need to roll the rotor. It just pulls right out. It’s much quicker. And that means guys will be more willing to stop and make those adjustments.”
Mackenzie said some farmers who tested the system this year installed only two or four frames and still noticed significant improvements.
“At first we figured owners would buy just the frames they needed and a variety of boxes, so they would change just the boxes,” he said.
“But my guess now is that they’re more interested in getting a certain number of frames permanently set up with boxes for different conditions, so they just swap frames.”
The different styles of boxes areverything is manufactured to fit into the original STS pocket without modifying the combine. One of the side benefits of the system is that rock damage will be limited to a small number of parts. Because the whole concave is segmented into smaller components with replaceable boxes, shipping costs and time is reduced. |SUNNYBROOK WELDING PHOTO
interchangeable. Each style is designed to match the tangential flow of a specific crop through the processor.
Minimum thresh smooth box
The smooth box is most effective in canola. By installing one or two frames with smooth boxes, material is accelerated to rotor speed without pulverizing the material other than grain.
The threshing bars are still exposed when traditional filler plates are installed underneath the concave. Too much material ends up on the shoe, so overall combine capacity is limited by the cleaning system.
“The smooth surface moves material back through the system without overloading the cleaning area immediately beneath the front of the rotor,” said Mackenzie.
“In canola and crops that thresh quickly and easily, boom, you’ve got all the stuff going through immediately. Now the operator has to slow down because it’s overloading at the front. We’ve found that the smooth boxes disperse the crop better. It allows you to utilize more of the cleaning area.”
The smooth box and easy transition from feed beater to rotor are also beneficial in other crops and conditions.
Maximum thresh angled box
Perpendicular layout of threshing bars to the flow of material in a rotary combine is key to eliminating unthreshed heads. To achieve that geometry, bars are welded to the box at a 45 degree angle, which puts the square bar stock perpendicular to the direction the crop moves.
The most common observation by test combine operators was that this box allowed them a marginal increase in concave to rotor clearance. As a result, sample and capacity were improved.
The angled threshing bars will wear as they work material, but the box concept allows for reversal and doubling of service life.
Round bar box
The round bar box works well for large seeds or where gentle action is needed. It threshes and separates without overloading the shoe, which can be a problem with traditional round bar designs.
Mackenzie said it’s important to avoid skin damage on delicate crops such as beans and lentils, which is why the round bar is better.
“Now you have a threshing pad instead of wires. The rod performs the threshing.”
The most common comment from operators who tried the round bar was that they got a cleaner sample.
Standard box
This box has 21 holes and functions much like a traditional wire concave but with more square inches of metal surface in the concave to provide more threshing area.
Mackenzie said it’s the same concept as the angled box but not as aggressive.
“On a conventional concave, you put blanks at the front when there’s a threshing problem. This gives you a threshing pad. The performance advantage of the standard box is not tremendous, but it does have an increased service life because it’s reversible.
“Really, what all these boxes do is give you more options and configurations so you can get the most out of your combine. And you don’t need to spend a lot of time making the adjustments.”
Foster said there’s no doubt box design will be an ongoing process.
New threshing concepts will be relatively easy and economical to try because Sunnybrook needs to design and build only a small number of test boxes to fit existing frames.
He said that’s quicker, easier and cheaper than building a new prototype concave each time the company has a new idea.
This will allow it to push new processor concepts further and faster than what was previously possible.
Sunnybrook is already known for pioneer work in boronizing combine wear parts to increase longevity and reduce friction within the processor. Foster said the boron treatment will be an option on all new boxes.
He said better combine performance puts more seeds in the bin and money in the bank, but there’s another economic factor in the box style concave concept.
“A big cost in concave replacement is freight. It cost us $300 to $500 to ship a few hundred pounds inter-province. After the initial investment, the replaceable boxes are a fraction of the price of a complete concave. If a rock bends two or three boxes, that’s all we need to send you.
“They can be couriered or mailed for about a tenth the freight cost of a whole concave.”
Prices depend on the complexity of building each type of box. At the low end, a single frame with seven smooth boxes sells for $425. Two are needed, so the price is $850. That replaces one Deere factory concave frame. The 21-hole standard is the most labour intensive. A single frame with seven boxes sells for $600.
Mackenzie urges producers to closely assess their threshing problems before deciding which boxes to buy. Because there are dozens of combinations, there may not be a single magic bullet solution for each condition.
Sunnybrook plans to debut the box style concaves at the Crop Production Show in Saskatoon Jan. 9-12.
For more information, contact Gerald Foster at 780-789-3855 or visit www.sunnybrookwelding.com.