A system that identifies harvest losses from the combine and header can be used to make on-the-fly adjustments.
Farmwave’s Harvest Vision system has three cameras, a network switch and the Farmbook computer, which are powered by artificial intelligence (AI) models.
The system is designed to detect header and combine harvest loss in real time, and to provide the information to growers with a display in the cab.
This enables operators to immediately see how adjustments they make to combine settings affect losses, which can be especially helpful as harvest conditions change throughout the day.
Read Also
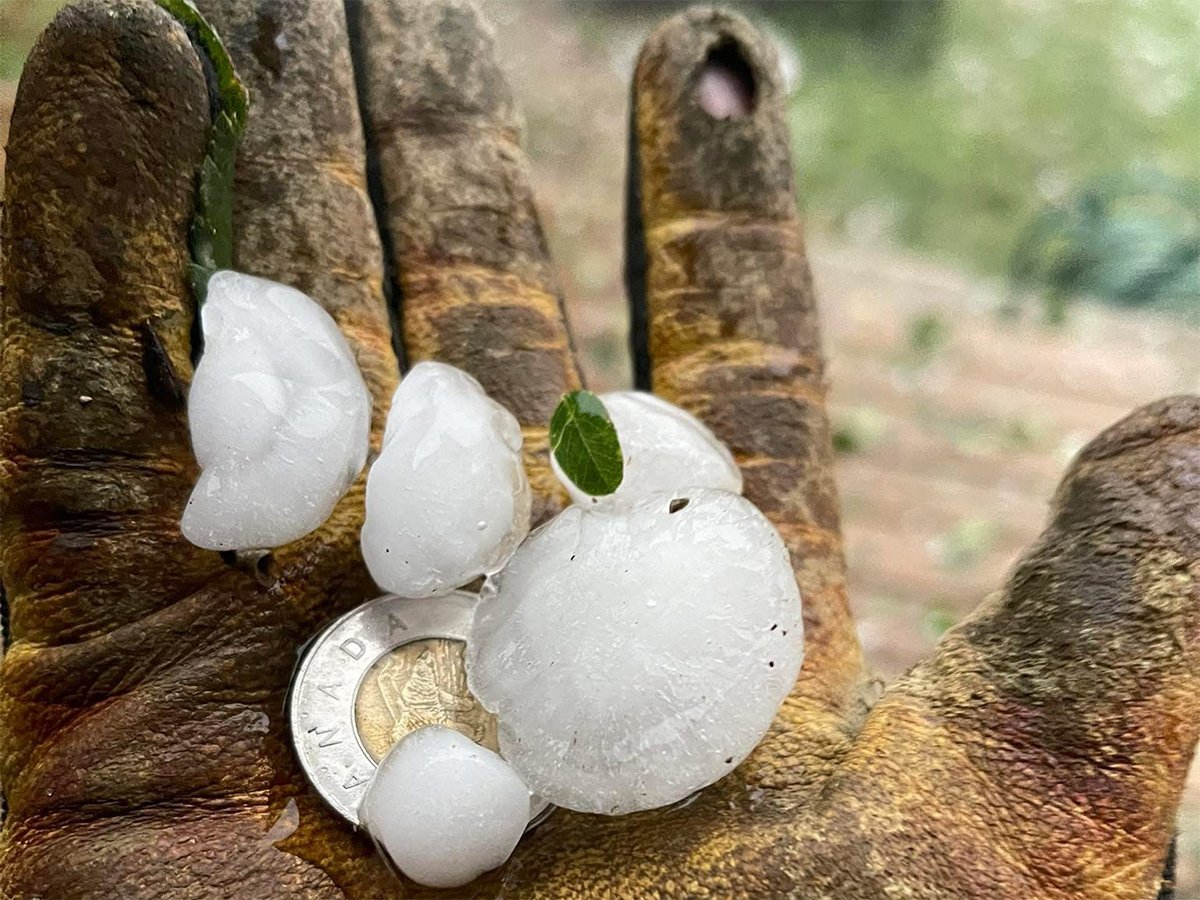
Half million acres of Alberta crops affected by massive hail storm
Late August hail storm catches farmers in prime harvest mode, damaging half million acres of crops in Alberta.
“In addition to not having to stop and get out unless you have to to make a manual mechanical adjustment on something, if you make a change to the reel speed, slow down, change the fan speed, whatever, you’ll know right away in the next three seconds if that helped or not by the counts that Farmwave provides,” said Craig Ganssle, company founder and chief executive officer.
“It’s been saving farmers an average of three to eight bushels per acre. It counts autonomously 140 times an acre without stopping.”
He said the company has algorithms that count harvest loss in corn and beans, with wheat, canola and barley coming later this year.
The system has a camera on the back of each side of the header looking down at the ground, and a third camera is mounted on the rear axle pointed up toward the chaff that’s being discharged out the back.
“We’re actually capturing kernels in mid-flight as they come out the back,” Ganssle said.
“Each of the cameras take a picture every three seconds, and that’s what equals about 144 times an acre.”
He said an operator testing the system found excess losses occurring on one side of the header that would be very difficult to identify without a high-resolution camera and a machine learning-based program capable of performing seed counts on the ground.
The cameras are magnet mounted, so they can be moved around to obtain the best vantage point.
The header cameras cover three by three foot areas on the ground just behind the header.
“It’s taking that picture and literally counting the kernels,” Ganssle said.
“We don’t see underneath the trash, it’s not X-ray, but the sheer volume and how many times we are counting just gives you a trend.”
The touch screen display in the cab connects to a small CPU, and a five-port switch powers the cameras.
“There’s just one cable, so you get a wiring harness for each header. If you have a corn and a beans header, you get a wiring harness for each, and the cameras you can just disconnect, move to the next header, and plug it back in and keep on going.”
He said Farmwave’s Harvest Vision system does not yet connect to task management systems in combines, mainly because it produces more data than original equipment manufacturer systems can handle.
However, he said Farmwave is working on integrating it into harvesters’ systems so that it can autonomously adjust the combine without human intervention.
“We’re a little way away from that, until everything aligns, and the OEMs would be ready for that. But this year’s version will have a recommendation window that will pop up and give you recommendations on things (adjustments) to do,” Ganssle said.
The Harvest Vision system works without cellular connectivity, but in areas with connectivity a farm manager can receive the readings.
“You will be able to check in on the other combines and tell them ‘hey, you’re losing five bushels off the left side of the header, what are you doing?’ Or, ‘slow down and change your reel speed,’ ” Ganssle said.
Cellular connectivity also allows Farmwave to improve Harvest Vision.
“As people harvest, we will collect that imagery and we use that to retrain models, and so by the end of the first week (of harvest), it could jump inaccuracy by 10 to 20 percent — that quickly just because we take imagery live in the field and we continuously retrain the algorithms,” Ganssle said.
“We don’t sell shares or do anything else with the customers’ data. It’s not ours. We use it anonymously, so we strip out a lot of the metadata, and we just use it to help retrain the algorithms.”
He said dust blocking the cameras has not been an issue, although it might become more of an issue as the system is calibrated for dustier crops.
The system is also limited by light conditions, but extra lights can be added if needed.
Harvest Vision can be ordered with only one camera for US$16,000 and each additional camera costs an extra $4,000.
There will be 500 units sold in the 2023 season, either direct to farmers or through dealerships.