LOUISVILLE, Ken. — Three Canadian companies have won agricultural engineering awards from the American Society of Agricultural and Biological Engineers this year.
The annual awards recognize the top 50 innovations in machines or processes that had a significant effect on agricultural or food production and were introduced in the past year.
This year, Winnipeg’s MacDon Industries won for its new crop cutting and conveying system in the MacDon R85 Rotary Disc Header.
The hay header uses a full width, over-shot, feed auger mounted behind 10 co-rotating cutting discs. The auger is in two sections with a centre mounted support that is attached to the back of the cutter-bar cradle.
Read Also
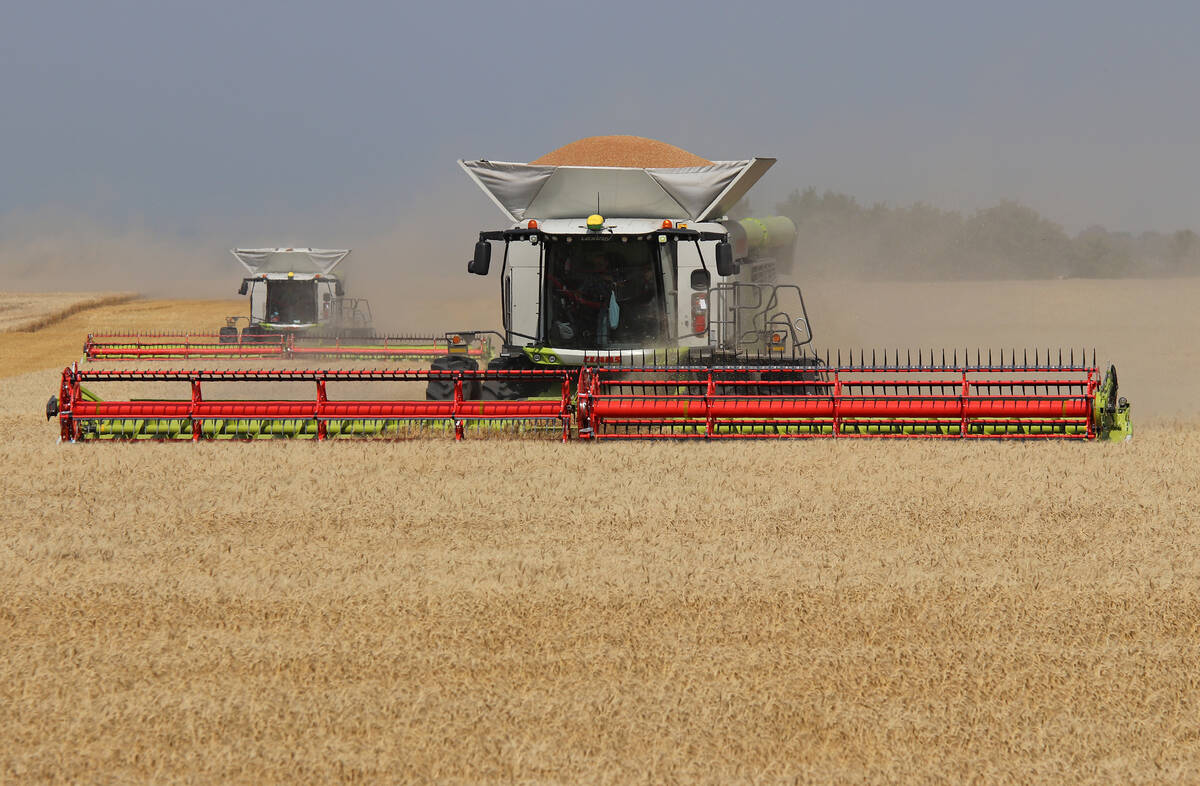
China’s grain imports have slumped big-time
China purchased just over 20 million tonnes of wheat, corn, barley and sorghum last year, that is well below the 60 million tonnes purchased in 2021-22.
At 16 feet wide, the unit can flex to accommodate variations in the field. Because the feed auger covers the entire header width, the cutting discs are set up to maximize the crop throughput, adding capacity and cutting quality.
The other two awards went to Quebec companies.
One, by Dion of Boisbriand, was for a rotary corn head for pull-type forage harvesters including New Holland’s 900, FP230 and 240, Deere 3955 and 3975 and Gehl 75 and 85 series, as well as Dion’s own machines.
The Dion F64 provides uniform crop feeding, without regard for row spacing or direction, by using a set of unique gathering drums and conveying chains.
The Development Forage Equipment header uses heavy-duty O-ring type chains for crop gathering, and the hardened steel cutter knives are driven by belts for smooth operation.
The unit is sold as a user installable kit.
For more information, visit www.dionmachineries.com.
Sync2 pump
A piston pump from GEA Houle in Drummondville won for its ability to move manure liquid that contains solid content.
The Sync2 is a twin cylinder, reversible hydraulic driven pump that uses a pair of cylinders to run two, three or four-inch pistons.
The twin pump provides a pulse-free flow that can be managed in downstream separating, storage or placement into a digester.
The ability to vary the hydraulic flow provides variable flow rates that make it possible to install the pump into existing barn operations without significant re-plumbing.
The pumps are capable of high evacuation line pressures of up to 111 pounds per sq. inch in the four-inch model, resulting in the ability to move material several kilometres. The three-inch model, when paired with a 7.5 horsepower motor, can reach flow rates of more than 500 litres per minute at 63 p.s.i. The two-inch version with a variable rate hydraulic pump can flow as little as 75 litres through the six-inch discharge.
The units are easily serviced with basic hand tools and feature steel flapper doors under each piston for reduced plugging and service.
For more information, visit www.gea-farmtechnologies.com.
Good fit on Prairies
Many of the AE50 winners for 2012 are a good fit for prairie agriculture.
Douglas Prairie of Raven Industries said the introduction of Omniseed fulfills his company’s goal of developing a multi-product, variable rate, towerless RTK system.
The company from Sioux Falls, South Dakota, began as a weather balloon company in the 1950s and now manufactures electronics, plastic films and precision agriculture tools. It still makes balloons, but they are now used for military surveillance.
Raven also builds many of the valves and flow controls used by other manufacturers for fertilizer application.
ASABE recognized Omniseed as one of the few variable rate systems that could manage the complex, single pass seeding requirements in the Canadian West, Australia and the Washington Palouse region.
The system combines the Omniseed software with up to five small, $600 hydraulic piston product metering motors and drives it with the Raven Viper Pro 10.4 inch screen field computer. Raven won an AE50 award last year when it put the metering motors on corn planters.
The company has collaborated with Saskatoon’s Agtron to add up to 240 of that company’s daisy-chained run-blockage sensors.
It has also added low bin and shank down-pressure sensors, fan and shaft sensors, liquid and anhydrous ammonia systems and eight runs of sectional control when paired with a Seed Hawk drill.
Raven is offering variable rate retrofit kits for Morris, Bourgault, Flexicoil, New Holland, Case, Seed Master and Deere.
Omniseed can be monitored from the farm office when put on the Slingshot, cellular RTK and telematics systems, with field maps sent directly to the Viper Pro console.
Hypro improves shut down time
Hypro’s AE50 award started with the realization that there was a problem with wet boom systems.
“They took too long to shut down when small orifice tips were installed,” said company spokesperson John Lang.
“Ten seconds from the time you cut them off until they stop spraying is a lot of distance at 14 m.p.h. … Even at 10 m.p.h., five seconds is 73 feet.”
He designed an end of boom unit that bleeds off the air without losing pressure.
“The air collects at the end of the booms, sometimes large bubbles build around a nozzle body. It all adds up to variability in the rates and cutoff times,” he said.
The Hypro Express end cap improves boom shut down from two to 10 times and also has a plug that can be removed for boom flushing and cleaning.
Hypro also won for its Scorpio solenoid nozzle body valve.
It mounts on the wet boom using three-quarter inch plumbing and can provide instant on and off control.
The simple, two-wire system doesn’t need to have reversed polarity or other wiring to control the highly serviceable valve. A rare earth magnet does most of the holding when it’s open, meaning the valve draws little power. The valve closes when the power stops, ensuring that it fails safe if there is a wiring issue on the boom.
The valve unthreads from the housing and can be cleaned with the seat replaceable.
“It can attract some small metal fines and seats will wear, so we made it fully serviceable,” he said.
The Minnesota-made Scorpio can run 2.5 times as much product through its body, uses 1,600 times less power than other nozzle mounted valves and can be used with most of the available controllers capable of sectional control without the need for separate power and control circuits.
The units have an LED light that indicate they are functioning.
Smartphone controls
Loadout Technologies of Indiana, another winner in Louisville, has a yellow box that is capable of many things.
It won an AE50 award for making it possible to remotely control slides and other electrically actuated grain loading equipment with an Apple or Android/Google smartphone.
A built-in camera connection provides a wireless feed to the smartphone, allowing the truck operator to watch the box or trailer loading and shut down the grain or fertilizer flow without leaving the cab.
Neil Mylet designed the system in his family’s barn.
“After university I wanted to farm, but needed something else as well. My family farms 5,000 acres of corn and beans in Indiana. I wanted a business that is based on the farm and could still be involved in agriculture,” he said.
“I have bad allergies to grain dust and so being able to stay in the (truck) cab makes life better and it means faster loading times with less labour too.”
The tool is able to run slides on an overhead hopper bin or auger.
The compact WiFi driven system comes in a yellow poly case, hence the name Yellow Box, and mounts wherever the camera and wiring for the grain handling equipment can be mutually located.
“We are getting interest from other sectors, such as mining and forestry, wherever there are industrial processes that could be controlled remotely more efficiently or safely while still giving some visual feedback,” he said.
“Its communication with the smartphone is encrypted and can’t become confused with other phones or units. It fails safe in any situation, and the technology is capable of learning some of the commands and processes on its own.
“Inside the Yellow Box are more than 700 components. And yes, it’s smaller than a breadbox.”
Variable rate motor planter
AE50 winner Jerry Graham, who farms in eastern Colorado, had tried a twin-row system that staggered his corn plants.
He liked the precision of the staggering but wanted to have variable rate planting so that he could increase and decrease his plant populations across the seeder and from side to side.
“You want different populations along a waterway, around a (slough), along a road or field edge,” he said.
“And you want to vary the population for different soil or field topography or cut it off completely in an overlap. You can do that, and without replacing sprockets or putting on huge hydraulic setup.”
His son had been a data specialist with General Motors’ racing division. His systems collected and relayed live data from race cars, including dragsters covering quarter miles in five seconds.
“That was until GM when broke,” said Graham.
“So he started solving some problems for his dad.”
Graham replaced the chain and hex shaft drives on his 16-row Monosem planter with variable-rate electric motors.
Each seed run gets a motor and can be set in relation to a master or target plant population.
The 5,000-hour duty cycle motors receive their instructions from a control box, one for every four motors. It communicates wirelessly with the interface box in the tractor’s cab.
That box can be hooked to any ISOBUS compatible controller or to the available touch-screen controller from Graham Equipment.
“The wireless system isn’t subject to any interference. The technology was developed for the racing industry,” he said.
“So if two units are in the field, they don’t cross-talk. And there is no bulky harness to run to the tractor.”
The motors draw three to 4.2 amps, so he offers and recommends a supplemental 65 amp, hydraulically driven alternator in any application above 12 rows.
The farm-based business has sold 1,200 units since it started development three years ago.
“All of the folks who installed the prototypes bought more units this year,” said Graham.
Monosem will be offering the Graham variable rate drives as a factory option on its planters next season.
Kits are available to retrofit all six of the major planter brands.
Graham said the next step is to drive several seed rows with a single motor and use linear actuators to control the planting rate.
Priced at $950 per row and $950 for the touch screen controller, if needed, the system makes variable rate planting affordable, said Graham.
“We’ve got a good idea that is cheaper and easier than installing multiple electric clutches, hydraulic units and it gets rid of all those chains,” he said.
“Something the zero-tillers can appreciate as they get off the tractor to replace for the umpteenth time. I guess that’s why we got the (AE50) award.”
Other notable winners of AE50 awards this year
AGCO
- Rogator RG1300
- Smart cooling on Gleaner combines
- Terragator TG8400
- WR series of Massey swather
Capstan Ag Systems
- Pinpoint individual spray nozzle control
Case IH
- Independent combine grain tank cross-auger control
- Magnacut fine cutting chopper
- Steiger 600 tractor
Claas
- CEMOS computer controller and operator interface
- Quadrant 3300 square baler
DuPont
- Precision Pac herbicide dispensing unit, which was in Canada for a few years ahead of the U.S. introduction.
GEA Houle
- Sync2 modular piston pump for manure
John Deere
- 4940 self-propelled sprayer
- 7R series tractor
- 9R/9RT tractors
- 600 series combine flexible draper headers
- S series combines
New Holland
- Mowmax 2 cutterbar for mower conditioner headers
- Syncroknife centre drive for the 880CF flex draper header
- T8 series tractors
- T9.560 tractor
Oxbo International
- 4334 self-propelled hay merger
Spectrum Technologies
- Waterscout SMEC soil moisture, temperature and salinity probe
Sukup Manufacturing
- Single-phase powered centrifugal grain dryer
Sy-Klone International
- RESPA CF Vortex Hyperflow cab air filtration system
Vermeer Corp.
- VR1428 high capacity wheel rake