Research Trends is a Western Producer story series exploring agricultural research at the University of Saskatchewan and other publicly funded research institutions in Western Canada.
Feeding farm animals used to mean trudging to the feed bin, scooping out a few pails full of whatever was available and throwing it in a trough.
But today’s feeding industry is not the feeding industry your grandfather knew.
Times are changing, and University of Saskatchewan feed researcher Tom Scott is at the centre of that change.
Read Also
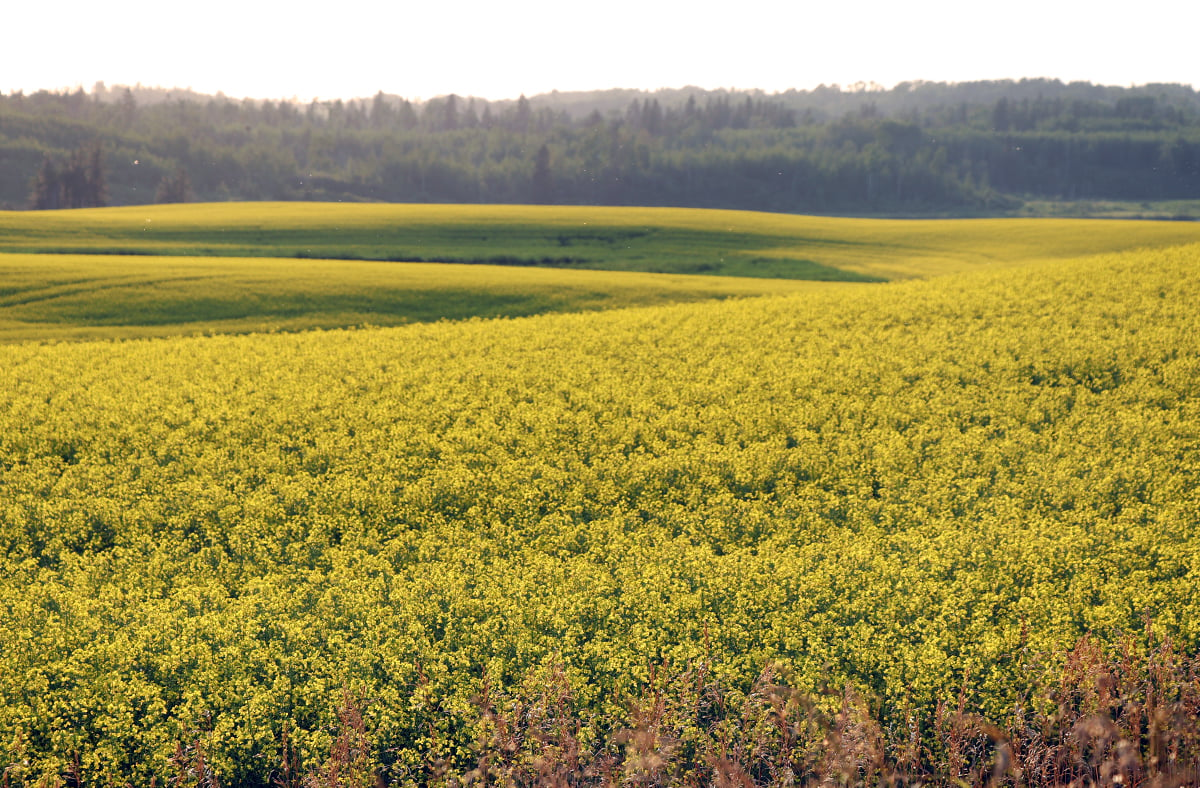
Agriculture ministers agree to AgriStability changes
federal government proposed several months ago to increase the compensation rate from 80 to 90 per cent and double the maximum payment from $3 million to $6 million
“Right now, when it comes to feed research and processing, we are shooting in the dark,” said Scott.
“Much of what’s being done is an art. This (our research) is really aimed at putting some science into that.”
Beginning this year, Scott and other feed experts at the U of S will conduct advanced feed research in a state-of-the- art processing facility at North Battleford, Sask.
The Canadian Feed Research Centre will be a feed research facility unlike any other in Canada.
Its equipment will include hammer mills, roller mills, flakers, screening machines, mixers, cooking and conditioning equipment, extruders, pelleters, vacuum coaters and a $400,000 near infrared seed sorter that can sort seeds according to their nutritional characteristics.
The $13.3 million facility will conduct research that enhances the nutritional value of bulk feedstocks such as cereal grains, canola meal, pea hulls and dried distillers grain.
“One of the main targets is to identify if we can more closely match processing conditions to changes in ingredients and thereby produce more consistent feed that will lead to (better) animal production, better health and less reliance on additives such as antibiotics,” said Scott.
” The research will also reduce the impact of the whole industry on the environment.”
The facility will include a pilot processing line for developing and testing experimental feed rations and have a direct link to a commercial line that will help move research to applied applications.
The commercial line, which is already operational, is licensed to Cargill.
Scott said the new facility has the potential to take animal nutrition studies and feed processing research to a new level. He estimates that only five other facilities in the world have similar processing capabilities and none are linked to a commercial production line.
“There are a lot of facilities that have small mixers and small grinders, but very few have the hydrothermal capacity that this facility will have,” he said.
“This is the only feed mill in Canada that would have all of those resources, together with the flexibility of doing small to large batches of research diets.”
Hydrothermal refers to the use of temperature, moisture and time during conditioning and before pelleting and extrusion.
One of the keys to the North Battleford facility is its ability to analyze the nutritional variability in feed sources that are abundant on the Prairies.
Conditioning feed with heat, moisture and time can reduce risks associated with feed borne disease such as salmonella, enhance feed-use efficiency and alter an animal’s feeding behaviour. However, conditioning is also costly and can have negative effects on animal performance if done incorrectly.
Cooking feed at 80 C can kill potentially harmful microorganisms in some feedstuffs without destroying beneficial enzymes.
Alternately, cooking at more than 100 C can denature protein, making it unusable to some livestock.
Similarly, a conditioning regime that uses the proper combination of time, temperature and moisture can gelatinize starch in a common feedstock such as wheat, which generally improves digestibility.
A different conditioning regime can be used to retrograde starch, making it unavailable to monogastric livestock species such as chickens but available to ruminants.
Mixers, pelleters and vacuum coaters can combine dozens of feed ingredients into a single ration.
Vacuum coating may have the potential to infuse pellets or extruded feed with probiotics or vaccines and help them survive the harsh environment of the stomach.
Pelletized or extruded feed particles contain tiny air pockets or pores. When the particles are placed in a vacuum and liquid vaccines or coating agents are added, releasing the vacuum will automatically suck the liquid into the pores.
“This is potentially an opportunity for protecting delivery of things like vaccines, probiotics or other enzymes that improve digestibility,” Scott said.
“In some cases, particularly with poultry, it is very difficult to vaccinate billions of birds manually but if you could do it (through diet), there’s a potential to really improve the health of those animals.”
Even a factor as simple as particle size can significantly affect animal performance, he added.
“There’s some evidence to suggest that grind size in pigs, for example, can make a 20 percent difference in animal performance.”
Scott said research conducted at the centre could lead to significant improvements in feeding practices and animal performance.
One study will begin with three simple feed formulations.
Different processing techniques will transform the formulations into 144 specialized rations.
The nutritional characteristics of those rations will be analyzed and eight will be selected for animal feeding trials.
“You can do all the analysis and measurements you want, but we still have to do animal trials to validate.”
Research at the centre will ultimately be aimed at improving animal health and the profitability of the feeding industry.
“Feeding is a very low margin industry, but it’s also a very big industry so a one percent increase in feed value could result in significant benefits,” Scott said.
“Right now, the cost of processing is somewhere between three and five percent of the cost of feed.… That means that in order for it to be valuable to the feeding industry, processing activities have to improve animal performance by more than five percent. The issue now is that most people who are doing feed research are doing it hit and miss.”
The North Battleford facility, which is due to open late this year, will eliminate much of the guesswork in feed processing.