Ted Dyck thought it was a shame that drain oil from diesel engines couldn’t be used to heat his shop. That was back in the mid-1980s before anyone imagined $140 per barrel crude.
By 1987, Dyck was heating his shop with drain oil from diesel engines. His chimney was smokeless and there were no filters to change or to become plugged.
The same oil burning system he put together in 1987 has heated his 50 x 50 foot shop and his home for 20 years without a problem. It also provides hot water for the house in the winter. Heating both buildings takes about 1,600 gallons of waste oil per year.
Read Also
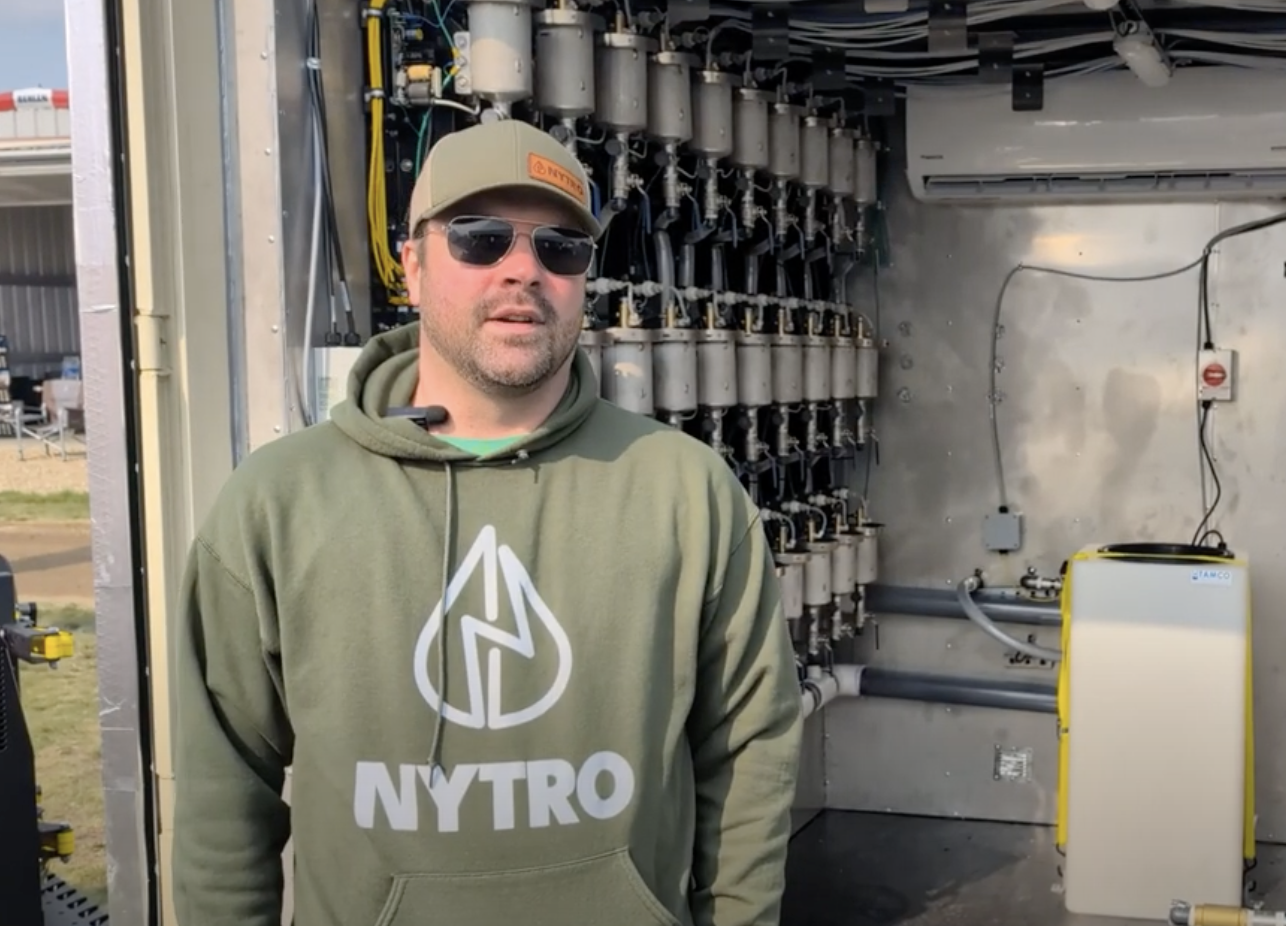
VIDEO: Green Lightning and Nytro Ag win sustainability innovation award
Nytro Ag Corp and Green Lightning recieved an innovation award at Ag in Motion 2025 for the Green Lightning Nitrogen Machine, which converts atmospheric nitrogen into a plant-usable form.
“If you look at the chimney on a cold winter day, you’d think I was burning natural gas. All you see is clear heat waves coming out the top. No smoke,” said Dyck, who farms 1,000 acres at Winkler, Man.
The key to this success was finding the right combination of components and then adjusting and tuning to create the right burn in the chamber. He didn’t want to be bothered with filters and blockages.
“I’ve got a 2,000 gallon tank behind my shop. I’ve got the thickest, blackest, dirtiest oil you can find anywhere.
“I get oil from my own farm and from a local implement dealer and a couple of local garages. I’ve never used a screen or filter of any kind. The oil goes into the furnace just the way it came out of the diesel drain plug. It’s really dirty.”
Dyck said part of the secret to burning dirty oil is finding a nozzle that will handle it without plugging. He finally discovered a large nozzle that doesn’t need a restriction to achieve atomization, so there are no screens or filters in his system.
“It’s an agricultural nozzle originally intended for low-drift pre-emergent chemicals. It’s an old design, but it’s still in the TeeJet catalogue.
“It’s a two-piece nozzle that has a disc with two slotted holes. Product goes through the disc and comes out spinning. There’s a large hole in the end cap. That’s why it works with waste oil.”
The oil is gravity-fed from the bulk tank down to a small electric gear pump that automatically switches on when the burner goes on.
As the dirty oil approaches the unique nozzle, it mixes with a small volume of compressed air.
“I found it works best at six psi. The air pressure makes the oil spin in the nozzle. Plus you need the air for combustion, so it makes sense to inject it along with the fuel. The oil also passes over a small pre-heater so it atomizes better at the nozzle. It comes spraying out the nozzle and it ignites with a spark from the igniter.
“It burns less than one gallon per hour.”
Dyck considered having the kits manufactured under licence. He had the plans and the conversion kit analyzed by the University of Waterloo.
However, the total investment to convert an existing oil furnace to waste oil is only $200 to $300 for parts. It’s all off-the-shelf components, so it didn’t make sense to sell the kits.
He decided to sell the plans and instructions.
“I sell about 75 sets of plans per year. The cost is $50.”
Depending on the basic furnace converted, heat output can exceed 200,000 BTUs.
For more information, call Ted Dyck at 204-325-8428 or visit www.tmdenterprises.ca.