FARGO, N.D. – When people are asked to name the first 4 x 4 tractor that had mammoth hydraulic capacity, topping the list is often the 90 gallon per minute New Holland scraper tractor.
In reality, however, the scraper tractor hydraulics can almost be termed an afterthought, says David Susag, a hydraulic engineer with Case New Holland in Fargo.
“These massive hydraulics systems really came out of the ag world, not the construction world,” said Susag, who added that New Holland worked closely with Flexi-Coil in Saskatoon when designing the TJ series.
Read Also
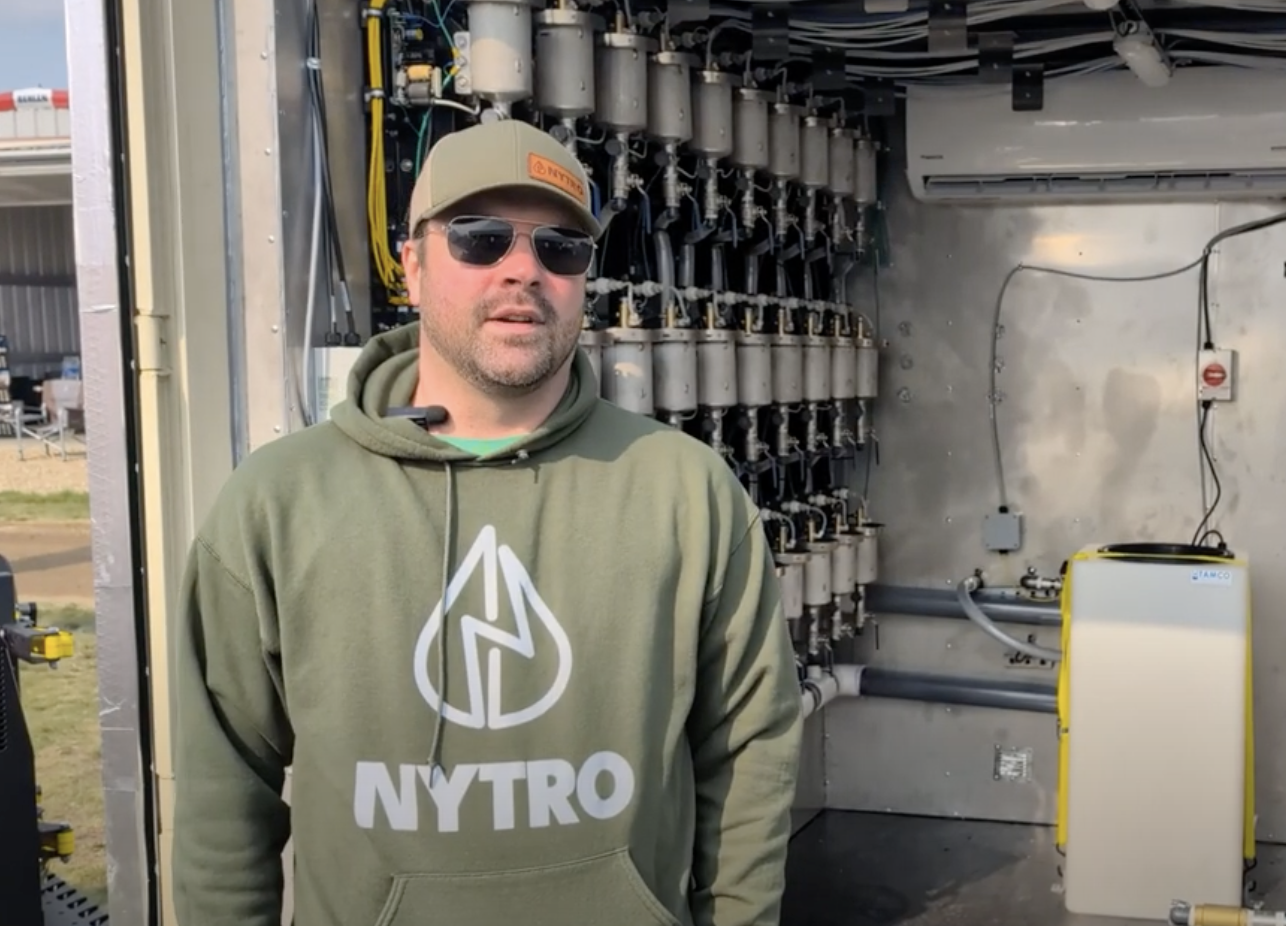
VIDEO: Green Lightning and Nytro Ag win sustainability innovation award
Nytro Ag Corp and Green Lightning recieved an innovation award at Ag in Motion 2025 for the Green Lightning Nitrogen Machine, which converts atmospheric nitrogen into a plant-usable form.
He said Flexi-Coil required extreme high flow hydraulics for the bigger air drills it was developing and had mapped out its long-term plans for a decade or more in advance.
“From our point of view, designing a new tractor like this was a big investment, so we had to work closely with our seeding group to make sure it would serve farmers needs well into the future. As a result, a lot of the work on that 90 g.p.m. system took place up in Saskatoon, not down here in Fargo.”
The first 90 g.p.m. MegaFlow systems were optional on the 2003 TJ series. New Holland achieved the high capacity by adding a separate hydraulic system with a dedicated pump to meet the fan demands of big air drills.
The regular high output pump on the TJ puts out 55 g.p.m. The second pump puts out an additional 35 g.p.m.
It’s called MegaFlow on New Holland TJ tractors and TwinFlow on Case STX tractors.
Susag said TJ and STX transmissions don’t have an output for a second pump, so they install it where the p.t.o. clutch would normally go. That means p.t.o. isn’t available with 90 g.p.m. on the TJ or STX.
“When the TJ first came out, the scraper guys looked at the specs and told us that’s what they needed to run those big scrapers,” Susag said.
“They need really massive flow to lift two scrapers at the same time and dump two scrapers at the same time.”
However, scraper operators don’t need two individual systems. So for the scraper tractors, CNH still uses the same two pumps but plumbs them parallel so both pumps feed into a single control.
For seeder tractors with MegaFlow or TwinFlow, the two systems are kept separate. Parallel flow for scrapers connects the two pumps to form a single system.
“A lot of our customers use their big seeding tractor for drainage work as well,” Susag said.
“We tell them to get the MegaFlow option to make best use of their seeding implement. And then when they hook up to the scraper, make sure you put it on the optional, separate pump. That gives them everything they need for both implements.”
On MegaFlow and TwinFlow tractors, an additional set of valves is installed at the back of the tractor to run the seeder fan. The parallel system for scrapers does not have the extra valves. The latest generation of electronic-hydraulic valves is standard on all tractors.
“The old bang bang valves are gone for good,” Susag said.
“That’s what everyone used to call those crude electronic controls prior to the TJ and STX. They were simply on or off. No in between. The laser said to raise or lower the scraper and the valve would instantly go full open or full closed – bang bang. The hoses jumped. The scraper jumped. The tractor jumped. And of course the operator jumped. It was hard on equipment and people.”
Susag said it took a lot of electronic tuning to get the valves to delicately feather open and feather closed.
“It’s very gentle now. Very smooth.”