WINNIPEG – Scientists around the world are trying to solve the puzzle of how to turn hog manure into a valuable commodity that can be profitably transported away from the hog barn.
Those working on the problem are searching for ways to separate phosphorus-rich solids from nitrogen-rich liquids in raw hog manure.
A Quebec engineering firm called Horizon Environmental Technologies, or HET, is tackling the challenge by using natural bacteria and accelerating its activity with a flocculent agent. The system processes a batch of raw manure in 12 hours.
Read Also
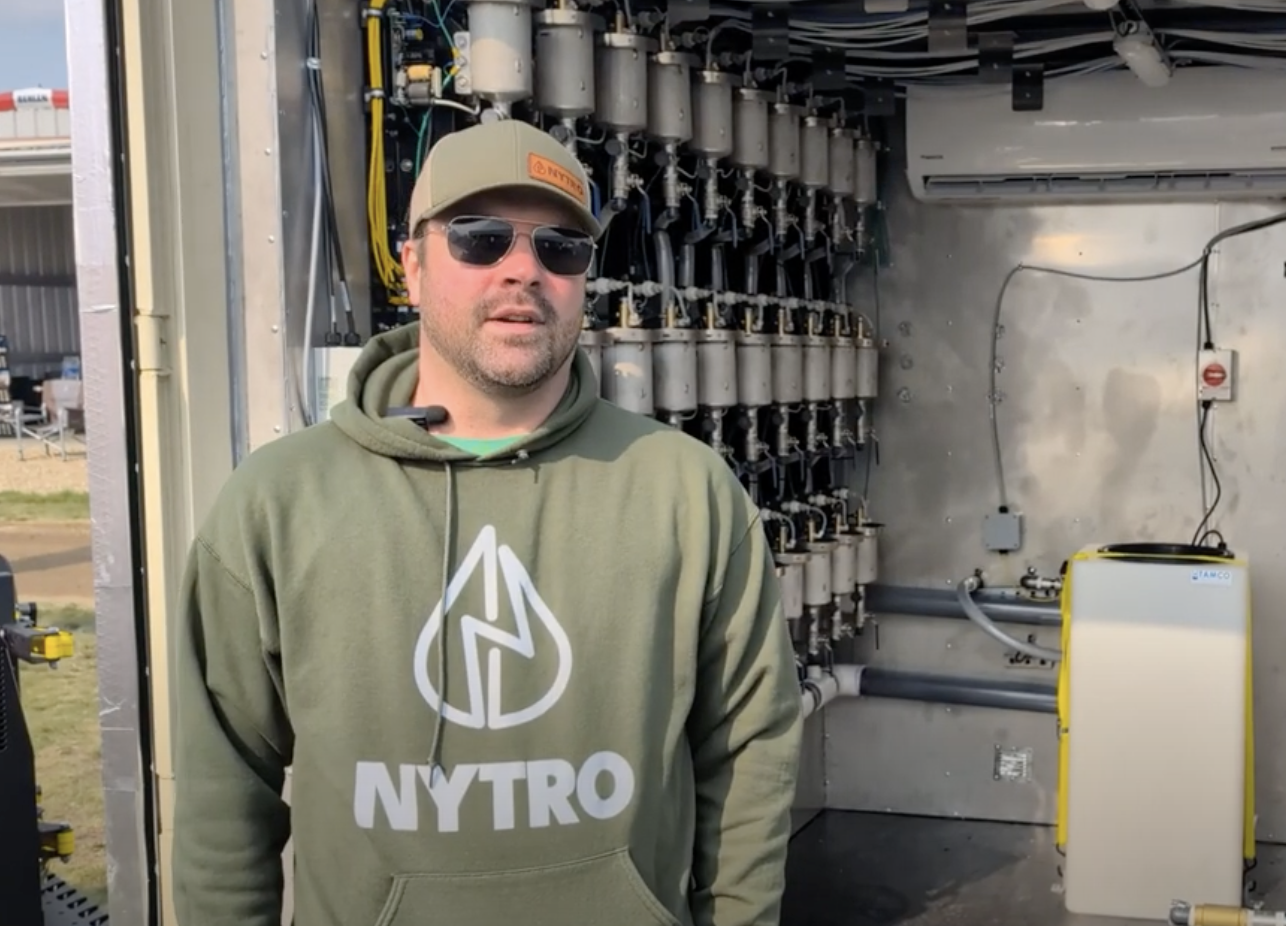
VIDEO: Green Lightning and Nytro Ag win sustainability innovation award
Nytro Ag Corp and Green Lightning recieved an innovation award at Ag in Motion 2025 for the Green Lightning Nitrogen Machine, which converts atmospheric nitrogen into a plant-usable form.
The additive also eliminates foul odours associated with hog manure, according to HET president Paul Boudreault, who has been an engineer on the project since the early concept stages five years ago.
“This is brand new technology. Nothing like this has ever been done before,” he said.
“We end up with a solid substance that smells like freshly cultivated soil and a liquid with a slight ammonia smell. And that’s the only odour we have. The flocculent agents we have developed are responsible for removing the odours. This is the first technology in Quebec to gain government accreditation for removal of odour at the source.”
Boudreault refused to divulge what goes into the patented flocculent agent.
HET calls its system the Lisox Separator. Although it may not separate phosphorus from nitrogen to the degree other systems achieve, the process is complete enough to create two distinct, commercially viable fertilizers.
Boudreault also points out other advantages of the HET system.
“The Lisox Separator has the lowest energy cost of any system on the market. Our energy input cost for processing raw manure is not more than $1.25 per cubic metre, because we let bacteria do the job. The scientific name we have for the process is bioflotation.”
Boudreault said bioflotation involves letting solid particles float to the top of the processing tank where they are removed by scrapers.
“If we let bacteria do the work for us, then we do not need to apply very much energy. It takes 12 hours to process each batch of manure as it goes through the tanks.”
The special flocculent is mixed in as the manure enters the machine. A different chemical flocculent is used for each different type of manure, such as maternity, nursery or fattening.
“Anyone could build a machine like this,” said Boudreault. “But without the chemical formula for the flocculent, it won’t work.”
The solid material coming out of the Lisox represents only 15 to 20 percent of the raw manure volume, but holds 80 to 85 percent of the total phosphorus content. The relatively lightweight material has a higher commercial value as fertilizer and is easier to transport.
“It ends up dry enough to be manipulated with conventional farm machinery such as buckets and conveyors and trucks. That means we can move it to a customer who needs phosphorus fertilizer.
“We’ve found that for potato producers, this solid phosphorus substance makes a very nice fertilizer. They really like it.”
Liquid makes up the remaining 80-85 percent of the raw manure volume. Since it no longer carries the high phosphorus content, it can safely be applied as a liquid nitrogen fertilizer.
“The liquid still retains 10 to 20 percent of the phosphorus, so it’s a well balanced fertilizer product. We can safely apply 13,000 gallons per acre and still be within government guidelines,” said Boudreault.
“It’s a clear liquid, so it’s easy to handle with conventional equipment you would use for any liquid fertilizer product. It doesn’t plug nozzles, so you can apply it through irrigation or with a field sprayer.”
He said that, like the phosphorus solid product, the liquid nitrogen can be sold to farmers who need it.
Boudreault said his company has three Lisox Separators running in Quebec. The first machine has been in operation on a pig farm since August 2004, where it handles 3,000 to 3,700 imperial gallons per day.
Although the early Lisox machines have a processing capacity of about 20 cubic metres of raw manure per day, he said the system can be expanded to any required capacity.
As a size comparison, Boudreault said a typical 2,000 sow, farrow-to-finish operation produced roughly 100 cubic metres of raw manure per day.
He said a Lisox system for a 6,000 sow, farrow-to-finish operation would cost $500,000 to $900,000. This cost depends on the extent of automation incorporated into the design.
For more information, contact Paul Boudreault or visit the website at www.corporationhet.com.